-
- News
- Books
Featured Books
- design007 Magazine
Latest Issues
Current IssueProper Floor Planning
Floor planning decisions can make or break performance, manufacturability, and timelines. This month’s contributors weigh in with their best practices for proper floor planning and specific strategies to get it right.
Showing Some Constraint
A strong design constraint strategy carefully balances a wide range of electrical and manufacturing trade-offs. This month, we explore the key requirements, common challenges, and best practices behind building an effective constraint strategy.
All About That Route
Most designers favor manual routing, but today's interactive autorouters may be changing designers' minds by allowing users more direct control. In this issue, our expert contributors discuss a variety of manual and autorouting strategies.
- Articles
- Columns
- Links
- Media kit
||| MENU - design007 Magazine
Estimated reading time: 4 minutes
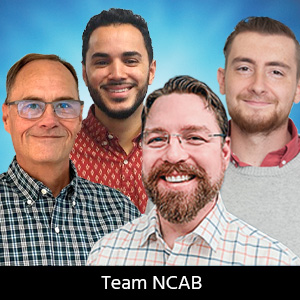
Fresh PCB Concepts: PCB Design Essentials for Electric Vehicle Charging
Electric vehicles (EVs), powered by electricity rather than fossil fuels, are transforming transportation and reducing environmental impacts. But what good is an EV if it can't be easily charged? Let's dive into the role of printed circuit boards (PCBs) in electric vehicle charging (EVC)—and the design considerations.
PCBs in Electric Vehicle Chargers
PCBs are critical to EVC systems, ensuring that charging infrastructure meets the demands of modern EVs. Responsible for power distribution, they make high-power, high-efficiency charging possible. This guide covers current trends in EVC PCBs, the types of EVCs and design considerations.
First, I want to mention the two main types of EV charging systems: AC and DC chargers. AC charging and DC charging can be distinguished by the location of power conversion. Unlike AC chargers, which convert AC power inside the vehicle using the onboard charger, DC chargers have the converter integrated within the charger unit. As a result, DC chargers can supply power directly to the car’s battery without relying on the onboard charger for conversion. AC chargers are specifically designed to operate with alternating current, the type of electricity typically provided by power grids. In contrast, DC chargers are tailored to function with direct current, which is commonly stored in batteries or generated by solar panels.
The standard for EV charging connectors or plugs varies among different regions and vehicle models. Although there isn’t a universal plug technology agreed upon, there is a significant number of global automakers supporting the Combined Charging System (CCS) in North America and Europe. Despite the existence of different standards, there is a growing consensus in various regions to promote the adoption of harmonized EV standards worldwide. Additionally, there are notable global standards and regulations for EVC, such as IEC 61851, which covers charging modes, connectors, and electrical safety. Another standard is ISO 15118, which focuses on the communication between electric vehicles and charging infrastructure. It is essential to recognize that specific regulations and standards may vary in different countries and regions.
Current Trends in EVC PCBs
Miniaturization and High-Density Designs
With fast-paced advancements, EVCs are becoming smaller, lighter, and more compact. This trend means that PCBs must evolve to make the most of limited space, resulting in:
- Higher layer counts and circuit density to accommodate more complex functions.
- Thinner materials (PP/CCL)
- Reduced space for connectors and 3D installs
- Laser drilled microvias and buried vias that are smaller and connect selected layers rather than going through the entire PCB. This in turn increases number of interconnections rather than traditional PTH design.
- Smaller components and smaller features
The miniaturization and complex design trends result in greater demands on the factories, in turn reducing the number of factories which can manufacture the product reliably.
Another notable trend in EVC relates to the speed in which the vehicle is being charged. This is a more essential need than in many other applications. Think about it: If you’re on a long trip and stop to recharge, more often than not, you don’t have the luxury of waiting hours for a full charge before hitting the road again. With increasing demand for faster charging times, PCB technology is also evolving to support efficient and reliable high power charging operations.
This requires the need for the PCB to handle higher currents and voltages for high-speed charging systems. This is where specific material and more copper is essential to facilitate this current flow and dissipate the heat created.
The design of high-speed charging PCBs is another factor that should be taken into consideration. For example, ensuring that the conductor width and insulation distance are properly positioned.
I’ve mentioned the need for increased copper, but with increased copper thickness we encounter challenges with fine details on the circuitry. The design must be balanced with the need for thick copper with the size and spacing for conductive tracks. As a rule of thumb, for 3-ounce copper thickness on external layers, the minimum trace width must be approximately 350 µm.
Solder mask also needs to be considered. In any high-power PCB, solder mask plays an essential role in providing insulation between tracks, particularly when heavy copper layers are used. This necessitates the need for increased solder mask thickness to fill the spaces between tracks. Designers should consult IPC recommendations, such as IPC-SM-840, to determine appropriate solder mask specifications.
We then come to the topic of thermal management. It’s essential to prevent failures due to overheating, and in this case, we need to position heat-generating components away from the board edge to allow for even heat distribution. I also recommend considering adding heat sinks and/or copper coin technology to facilitate heat distribution from high-heat generating components. This must be considered early in the design process. As I can tell you from experience, if you decide to add them in afterward, you almost have to start your design over from scratch.
These are the key factors to keep in mind when designing a PCB for EV charging. However, I always recommend consulting with your PCB supplier from the start to ensure you’re considering and addressing all the complex aspects of designing EVC PCBs, and to ensure high-reliability manufacturability.
Ramon Roche is a field applications engineer with NCAB Group.
More Columns from Fresh PCB Concepts
Fresh PCB Concepts: Designing for Success at the Rigid-flex Transition AreaFresh PCB Concepts: More Than Compliance—A Human-centered Sustainability Approach
Fresh PCB Concepts: Assembly Challenges with Micro Components and Standard Solder Mask Practices
Fresh PCB Concepts: The Power of a Lunch & Learn for PCB Professionals
Fresh PCB Concepts: Key Considerations for Reliability, Performance, and Compliance in PCBs
Fresh PCB Concepts: Traceability in PCB Design
Fresh PCB Concepts: Tariffs and the Importance of a Diverse Supply Chain
Fresh PCB Concepts: PCB Stackup Strategies—Minimizing Crosstalk and EMI for Signal Integrity