-
- News
- Books
Featured Books
- design007 Magazine
Latest Issues
Current IssueProper Floor Planning
Floor planning decisions can make or break performance, manufacturability, and timelines. This month’s contributors weigh in with their best practices for proper floor planning and specific strategies to get it right.
Showing Some Constraint
A strong design constraint strategy carefully balances a wide range of electrical and manufacturing trade-offs. This month, we explore the key requirements, common challenges, and best practices behind building an effective constraint strategy.
All About That Route
Most designers favor manual routing, but today's interactive autorouters may be changing designers' minds by allowing users more direct control. In this issue, our expert contributors discuss a variety of manual and autorouting strategies.
- Articles
- Columns
- Links
- Media kit
||| MENU - design007 Magazine
Estimated reading time: 4 minutes
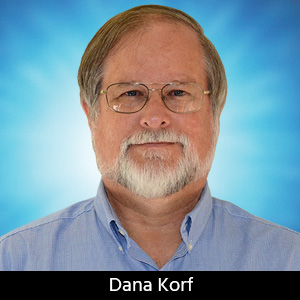
Dana on Data: PCB Data Transfer Non-evolution
Recently I was updating my family genealogy database. My family first arrived in America from England in the 1620s before eventually settling in the Dedham, Massachusetts, area. In one of our family history books, written in the 1880s, there is a picture of a land grant map of the Boston area that was created sometime in the late 1600s on either parchment or paper. Boy, do I wish we still owned all those properties.
Seeing such an old map still intact made me think about how much progress we have made in accelerating communication with each other. We’ve transitioned from hand-written parchment, to printing presses, typewriters, punch cards, word processing, faxes, and finally to direct computer-computer communication that doesn’t require any manual intervention.
Well, except for the PCB industry. We still send scanned copies of paper documents, which I have termed “ePaper,” back and forth to each other; this process requires humans to interpret the information on the electronic copy of a document before manually entering it into a computer. As many as 90% or more of all design data packages sent to manufacturing are still Gerber file-based with additional ePaper files.
So much for the concept of continuous improvement.
There is a significant number of publications discussing and working to implement Industry 4.0 automation that modernizes the use and analysis of data. Yet the intelligent/automated bi-directional design-to-manufacturing knowledge transfer is slow because we require humans to read and type information into a computer. Design files are transmitted at multi-gigabit data transfer speeds while humans read approximately 200 to 300 words per minute when transcribing ePaper files. For example, a 10-page PDF specification can take 10 to 15 minutes to read and interpret, and then another 30 to 60 minutes to load into an engineering system.
The industry has two data formats that provide the ability to send a significant amount of information in an intelligent, machine-readable format: IPC-2581 and ODB++. But less than 25% of the industry is estimated to be migrating to these formats. We also have direct IPC-2581 to CFX bi-directional connectivity for PCB assembly.
So, the current software development/user feature requirement process isn’t working. This hesitancy to adopt these new formats seems to be driven by fear of change. Many large and small companies have moved to intelligent data to reduce data transfer errors and improve productivity over the last 20+ years. On the manufacturing side, the data transfer/tooling time and resources, in my experience, adds 2–5% to a manufacturer’s operating cost; not to mention hours to days of input cycle time to read, resolve issues, and create tooling using this semi-manual process.
Couple this semi-automated process with a very serious shortage of PCB fabrication front-end engineers, who are needed to ramp up to proposed significant capacity increases, and you have the makings of a serious resource gap in the near future. There are limited formal education centers providing this training in conjunction with the industry. We will need to eliminate data errors and resolve design for manufacturability (DFM) issues to support the large amount of new part numbers required for this future production ramp.
So, let’s think out of the box and look at some alternative approaches.
The U.S. government has passed the $52 billion CHIPS Act to support adding additional integrated circuits (IC) fabrication capacity into the U.S. There is a U.S. House bill—Supporting American Printed Circuit Boards Act of 2022 (HR 7677)—that aims to provide $3 billion for the PCB fabrication industry for additional equipment to increase production capacity. But none of this funding has been specifically earmarked to help automate data transfer and tooling processes.
There are occasional competitions, funded by private companies and government organizations, that encourage out-of-the box projects. These are generally $1 million+ rewards for novel projects like autonomous vehicles, reusable spaceships, etc. But again, I’m not aware of any data transfer automation project awards.
Maybe NIST, NASA, DARPA, or another large private company that releases hundreds of designs per year could offer a $5 million prize to the first team that can demonstrate a fully automated, bi-directional PCB design-to-manufacturing data transfer for both fabrication and assembly/test. The goal would be to release intelligent information from designers and transmit that information to the manufacturing facility, where it would be automatically tooled with DFM changes before being returned to the designer to auto-update the original design. The information would include the PCB graphical data, specifications, BOMs, tolerances, special conditions, etc. The manufacturing facility would need to provide an intelligent electronic file detailing their process capability and rules to eliminate CAM edits.
An alternative to this approach would be to fund university research facilities to create this capability by modifying existing CAD and CAM software tools to both use and modify an existing intelligent data format, such as IPC-2581.
The industry needs a different approach to complete this 50+ year journey toward fully automated design in manufacturing; we need manufacturing to design information/knowledge that can be seamlessly integrated into the evolving Industry 4.0 activities.
Dana Korf is the principal consultant at Korf Consultancy LLC.
More Columns from Dana on Data
Dana on Data: Best Practices in Interpreting Drawing Notes—‘Use Latest Revision’Dana on Data: The Missing AI-NPI Link
Dana on Data: Merging 2D Electrical, 3D Mechanical Worlds
Dana on Data: Resurrecting IPC Class 1
Dana on Data: The Evolution of Fabrication Drawing
Dana on Data: The Insane PCB DFM Process
Dana on Data: eCAD PCB Design Deficiencies
Dana on Data: Nuke the Netlist