-
- News
- Books
Featured Books
- design007 Magazine
Latest Issues
Current IssueProper Floor Planning
Floor planning decisions can make or break performance, manufacturability, and timelines. This month’s contributors weigh in with their best practices for proper floor planning and specific strategies to get it right.
Showing Some Constraint
A strong design constraint strategy carefully balances a wide range of electrical and manufacturing trade-offs. This month, we explore the key requirements, common challenges, and best practices behind building an effective constraint strategy.
All About That Route
Most designers favor manual routing, but today's interactive autorouters may be changing designers' minds by allowing users more direct control. In this issue, our expert contributors discuss a variety of manual and autorouting strategies.
- Articles
- Columns
- Links
- Media kit
||| MENU - design007 Magazine
Estimated reading time: 4 minutes
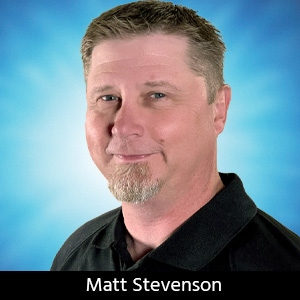
Connect the Dots: Examining the Benefits of Laser Direct Imaging
One of the most amazing advances in PCB manufacturing technology has been the advent and usage of laser direct imaging (LDI) technology. For PCB manufacturers, this technology has been a game changer, helping to reduce costs, speed production, and improve quality.
Though the LDI revolution began more than 20 years ago and usage of film for image transfer has reduced by half in that time, there’s still room for more PCB manufacturers to invest in this powerful tool. As an image department team leader and ISO process owner, I have seen firsthand the benefits of laser direct imaging for both my team and our customers.
Imaging is a key production step where the PCB design is transferred from its original digital format onto the physical manufacturing panel. This process ultimately defines all the copper features on a given layer, everything from pads to traces and plane areas.
As the name implies, LDI transfers the digital design data directly to the manufacturing panel without the use of an intermediary. The result is sharper and more precise features, with better registration and the ability to place smaller features more effectively.
We make higher quality, more reproducible boards with LDI. The higher resolution transfer makes the final board closer to the digital design. Figure 1 compares the LDI imaging process with that of a traditional approach. As we can see, Figure 1a illustrates that LDI uses a photo-based method to transfer the image to the panel, much like the traditional imaging processes. Figure 1b demonstrates that the LDI imaging process does not require a phototool as an intermediary during the exposure step.
Eliminating the photo tool and mylar or glass layer from the exposure process allows the light source to expose the photoresist more directly. This reduces interference and limits opportunity for the creation of air gaps in either of those two extra layers. By eliminating the mylar layer, the quality of the image process improves. The thickness of the clear mylar layer being present does two things: scatters light source (as it transfers between multiple different types of layers) and increases the effective distance between the light source and its ultimate destination (the photoresist). By eliminating this layer, it gives a more direct path from the light to create a sharp and defined image.
Air gaps cause issues with the quality of the exposure and can cause defects by allowing exposure in areas where it is unwanted. LDI eliminates the part of the process that can cause air gaps, generating a sharper and truer representation of the data being transferred.
In traditional photo-based methods, the alignment of the image with the panel can be a very tedious, and in some cases, impossible task. The LDI process better aligns the image with the panel than with traditional methods. The LDI process uses aligning targets called fiducials to calculate any movement that has occurred in the panel and correct for it. We can also calculate and adjust for any stretch, shrinkage, or skew that has occurred during the previous manufacturing steps. The copper image is, for practical purposes, perfectly aligned with the drilled holes.
The LDI imaging process makes my team better at our jobs. We have realized improvement in numerous areas because we adopted this method for imaging. Most importantly, we have improved the quality of our output and that reverberates throughout the PCB manufacturing process. The result is better boards.
The boards are not just higher resolution, they take less time to produce. We don’t spend time plotting, cleaning, and punching image films. What was once a two-hour process now takes 30 minutes, and we’re not going through 150 films a day, which results in cost savings.
LDI eliminates much of the error potential present using traditional methods. We’re not handling film, moving it from place to place and potentially damaging it, so there is less scrap. Inspection and quality assurance take less time because there are fewer defects to find.
Since less production time is spent on imaging, other production teams are less apt to be rushed and they have more time to focus on quality and process improvement. This has made LDI a critical component of our continuous improvement efforts and Lean manufacturing adoption.
Improving just one of the hundreds of processes in our PCB manufacturing facility pays dividends. Yes, my team can produce better results more efficiently, and this is great for our customers. The process improvements created by LDI also offer everyone on the team more opportunities for professional development. With less time spent on tedious traditional imaging efforts, we can focus on learning new skills that can lead to career advancement.
Technology advancements like the ones created by LDI have opened doors and helped me grow professionally. I started as a part-time chip coordinator and now I’m the image department team leader. When measuring the value of tools like LDI, we tend to focus on improving the quality of the boards produced and increasing customer satisfaction.
These tools also improve the quality of our working lives and increase satisfaction with our professional development.
Trina Taylor is team lead, image department, at Sunstone.
This column originally appeared in the September 2022 issue of Design007 Magazine.
More Columns from Connect the Dots
Connect the Dots: Sequential Lamination in HDI PCB ManufacturingConnect the Dots: The Future of PCB Design and Manufacturing
Connect the Dots: Proactive Controlled Impedance
Connect the Dots: Involving Manufacturers Earlier Prevents Downstream Issues
Connect the Dots: Stop Killing Your Yield—The Hidden Cost of Design Oversights
Connect the Dots: Designing for Reality—Routing, Final Fab, and QC
Connect the Dots: Designing for Reality—Surface Finish
Connect the Dots: Designing for Reality—Solder Mask and Legend