-
- News
- Books
Featured Books
- design007 Magazine
Latest Issues
Current IssueProper Floor Planning
Floor planning decisions can make or break performance, manufacturability, and timelines. This month’s contributors weigh in with their best practices for proper floor planning and specific strategies to get it right.
Showing Some Constraint
A strong design constraint strategy carefully balances a wide range of electrical and manufacturing trade-offs. This month, we explore the key requirements, common challenges, and best practices behind building an effective constraint strategy.
All About That Route
Most designers favor manual routing, but today's interactive autorouters may be changing designers' minds by allowing users more direct control. In this issue, our expert contributors discuss a variety of manual and autorouting strategies.
- Articles
- Columns
- Links
- Media kit
||| MENU - design007 Magazine
Estimated reading time: 7 minutes
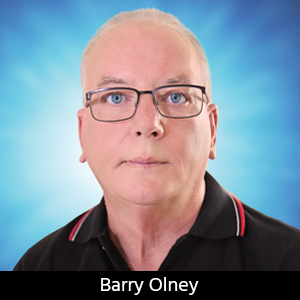
Beyond Design: Copper Pours in High-speed Design
The most common question I get asked by PCB designers is, "Do you need copper ground pours on digital multilayer PCBs?" The short answer is, "It depends." Unfortunately, the myth of copper pours is fueled by reference designs that seem to persistently use this old RF design technique. Copper pours are sometimes used, incorrectly, simply to fill in the unused space on a board. However, in some cases ground pours may be an advantage. In this month’s column, I will look at where to use and where not to use ground pours.
There are three reasons for using copper pours on multilayer PCBs:
- PCB fabrication: The primary reason is to provide a uniform copper distribution across a layer to make etching and plating more predictable, and to reduce the amount of etching fluid used (hence cost) during PCB manufacturing.
- RF and microwave design: Ground pours contain the electromagnetic (EM) radiation in a localized area thus reducing spurious coupling, radiation, and dispersion.
- Digital design: A ground plane improves noise immunity, gives much greater grounding uniformity, and provides a low inductance current path to devices.
Please note the distinction between copper pours and ground (GND) pours/planes. A copper pour per se is an isolated copper plate. This is not a good idea since it buys you little benefit, whereas a ground plane is connected to the distributed ground net.
During the PCB pre-fabrication process, the CAM engineer will generally add copper pours to individual layers of a multilayer PCB. This is referred to as copper thieving and involves placing a pattern of repeated simple geometrical shapes or cross-hatched regions into large void areas of a PCB. But this is not ground—it is floating copper. Copper thieving is best placed outside the board outline to avoid influencing the functionality of the design.
Some designers advocate leaving the copper thieving decisions up to the PCB fabrication shop, but this may not necessarily be the best design decision. While the fab shop will create thieving that will best fit the plating needs of the board, they will not necessarily have all the tools available to determine the electrical impact of adding metal to the design. Floating (unconnected copper) is a real hazard for signal integrity. All copper pours must be connected to ground or power net. A ground pour that is not accompanied by grounding vias can become a conduit for crosstalk between the traces on either side of the ground shape. The CAM engineer could inadvertently be creating antennae that radiate with the application of short wavelength signals. It is crucial that any metal changes to the board be done by the PCB designer so that all the potential effects can be taken into account. You can ensure this by stipulating in the PCB specification that no copper features be added or modified without permission.
PCB designers also can use these copper pours as more than just thieving patterns. By creating the copper thieving as part of the ground net, and configuring it as a solid plane, you can assist with providing a well-defined return current path. The caveat, however, is that this must be done in conjunction with the overall signal performance requirements of the design. Any additional planes must be positioned and spaced correctly, so they do not have a negative effect on the signal integrity of the board. The processor board (Figure 1), for instance, has what I call random copper GND pours on the outer layers. Many of these pours are totally unnecessary.
Applying this concept in RF circuits, grounded metal is sometimes used as fill between the signal traces on outer layers. The grounded areas should be connected to the ground plane with vias (stitched) at less than one-quarter wavelength (Figure 2). This technique changes the
transmission lines from microstrip to grounded coplanar waveguide. The characteristic and differential impedance of the transmission line is lowered by using this technique because the copper pours increase the capacitance between the signal trace and ground.
The coplanar waveguide (CPW) is the transmission medium of choice above 20GHz. CPW combines the EM fields in a more localized manner than does microstrip, thus reducing spurious coupling, radiation, and dispersion. Also, the CPW provides a precisely defined signal return path.
Internal stripline configuration has an advantage over outer layer microstrip. Microstrip can radiate. However, with the fields confined between ground planes, stripline does not. Signals can be shielded by placing the traces on internal layers between copper planes. These form stripline transmission lines. Such techniques are recommended for signals above a few hundred megahertz.
Grounded (guard) traces are sometimes used to surround digital clock signals, which tend to have fast edge rates. In addition to having a ground plane below the signal trace, copper traces are placed on either side of the trace and are stitched to the ground plane in multiple locations. For digital systems, this technique is only useful for traces on outer layers. On inner layers, it makes more sense to just leave some empty space around the trace. However, if microstrip is very closely coupled to the reference plane (
When copper pours come into proximity with critical signal traces (Figure 3), the impedance is reduced by 2–3 ohms. So, on the copper side of the differential pair, the impedance will be lower than the other side free of copper. This will convert differential mode signals into common mode signals at these points, impacting signal integrity. If a differential pair is well balanced, then tight coupling will achieve an effective degree of field cancellation. However, if they are not perfectly balanced, then the degree of cancellation is not determined by the spacing but rather by the common mode balance of the differential pair. This copper pour needs to be bordered by ground stitching vias and pulled back from the signal traces by at least 20 mils. Better still, it’s left out altogether.
Electromagnetic emissions from digital circuits can occur as either differential mode or common mode radiation. Differential mode is typically equal and opposite and therefore any radiating fields will cancel. Conversely, common mode radiation from two coupled conductors is identical. It does not cancel but rather reinforces. Unfortunately, differential mode propagation can be converted to common mode by parasitic capacitance, any imbalance caused by signal skew, rise/fall time mismatch, or asymmetry in the channel.
My recommendations for pours:
- All copper pours should be connected by stitching vias to the distributed ground net
- Do not use isolated copper pours
- Critical signals should be routed in the inner stripline layers with no pours
- Closely coupled differential signals can be routed on the outer microstrip layers without GND pours
- Critical single-ended signals can be routed on the outer microstrip layers if converted to CPW
- However, if microstrip signals are very closely coupled to the reference plane (< 3 mil) then radiation is minimal and providing ground shielding on outer layers has little benefit
PCB designs that are generally well-grounded (that is, there are ground vias connecting the planes in multiple places) create a Faraday cage that functions to contain internal resonances and energy that might be available to radiate from the edge of the board. Power distribution networks that are well-bypassed across the entire area of the planes also help suppress resonance. Copper pour and via stitching are unnecessary in many digital designs. Copper pour is not the magic bullet that will solve all your EMC problems. Pouring copper randomly to fill up space may create additional issues. Proper design practice should be applied rather than just random copper.
Key Points
- The myth of copper pours is fueled by reference designs that seem to persistently use this old RF design technique.
- Copper pours are sometimes used, incorrectly, simply to fill in the unused space on a board.
- The CAM engineer may add copper thieving patterns to balance the copper distribution on a layer.
- Floating (unconnected copper) is a real hazard for signal integrity. All copper pours must be connected to ground or power net.
- A ground pour that is not accompanied by grounding vias can become a conduit for crosstalk between the traces on either side of the ground shape.
- By creating the copper thieving as part of the ground net and configuring it as a solid plane, you can assist with providing a well-defined return current path.
- Any additional planes must be positioned and spaced correctly, so they do not have a negative effect on the signal integrity of the board.
- A ground pour on a microstrip layer changes the transmission line from microstrip to grounded coplanar waveguide.
- The characteristic and differential impedance of the transmission line is lowered by using this technique.
- CPW combines the EM fields in a more localized manner than does microstrip, thus reducing spurious coupling, radiation, and dispersion.
- Microstrip can radiate. However, with the fields confined between ground planes, stripline does not.
- When copper pours come into proximity of critical signal traces (Figure 3) the impedance is reduced by 2–3 ohms.
- This will convert differential mode signals into common mode signals at these points, impacting signal integrity.
Resources
Beyond Design: “To Pour or Not to Pour,” “Common Symptoms of Common Mode Radiation,” by Barry Olney.
An Altium Designer blog, “Copper Pour and Via Stitching: Do You Need Them in a PCB Layout?”
This column originally appeared in the June 2022 issue of Design007 Magazine.
More Columns from Beyond Design
Beyond Design: Effective Floor Planning StrategiesBeyond Design: Refining Design Constraints
Beyond Design: The Metamorphosis of the PCB Router
Beyond Design: Radiation and Interference Coupling
Beyond Design: Key SI Considerations for High-speed PCB Design
Beyond Design: Electro-optical Circuit Boards
Beyond Design: AI-driven Inverse Stackup Optimization
Beyond Design: High-speed Rules of Thumb