-
- News
- Books
Featured Books
- design007 Magazine
Latest Issues
Current IssueProper Floor Planning
Floor planning decisions can make or break performance, manufacturability, and timelines. This month’s contributors weigh in with their best practices for proper floor planning and specific strategies to get it right.
Showing Some Constraint
A strong design constraint strategy carefully balances a wide range of electrical and manufacturing trade-offs. This month, we explore the key requirements, common challenges, and best practices behind building an effective constraint strategy.
All About That Route
Most designers favor manual routing, but today's interactive autorouters may be changing designers' minds by allowing users more direct control. In this issue, our expert contributors discuss a variety of manual and autorouting strategies.
- Articles
- Columns
- Links
- Media kit
||| MENU - design007 Magazine
Estimated reading time: 4 minutes
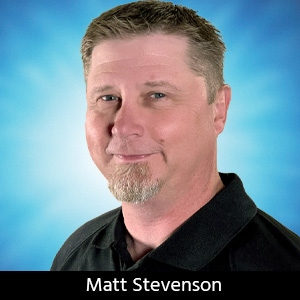
Connect the Dots: Six Key Considerations for Designers New to PCB Layout
Demand continues to increase for boards used in consumer electronics, intelligent machines used in manufacturing, and smart devices for health services applications. Our industry needs more smart people designing PCBs to help drive artificial intelligence (AI) initiatives and power the Internet of Things (IoT), which is why we are welcoming new designers into the fold every day.
The PCB layout process is, at its core, a seemingly simple one—connect all the points of the components to their necessary endpoints. In practice, it can get complicated in a hurry. For those new to design, it’s important to recognize there is much more to it than just routing traces from point A to point B.
So, what are the important design considerations you should be sure to consider?
The following are six design considerations to help ensure your design is reliable, includes all the necessary connections, is optimized for manufacturability, and dissipates heat away from the electronics.
1. Separation
In most design applications, it’s important to maintain separation of signal types. The most common example is keeping analog and digital signals and their associated grounds separate. A good design technique for keeping signals separate involves grouping the sections of the schematic—digital and analog that share a common ground—together in proximity and then placing the ground plane directly below this grouping. Similarly, running only analog lines over or under the analog ground layer will help reduce capacitive coupling of signals.
2. Four-Tips-in-One for Minimizing EMI
Electromagnetic interference (EMI) can really mess with board performance. EMI is a disturbance created by electromagnetic induction and electrostatic coupling or conduction. Here are four tips for reducing EMI from your design:
- Choose surface mount device (SMD) components over through-hole parts. Generally, the leads on the through-hole parts create higher levels of inductance and thus an opportunity to create EMI.
- Design with multilayers, adding a ground plane on the layer directly below the external signals (2 and n-1). The presence of these planes near the signal will effectively reduce the return path, keep signals clean, and reduce EMI emission. Connecting decoupling or bypass capacitors to these planes offers another effective technique for reducing EMI because you are creating short and logical return paths.
- Limit the operating current and/or the rise times of the signals to help reduce larger fluctuations in current. This creates lower EMI emission rates.
- Match the impedance on signals. This is a critical design practice, especially at higher signal speeds that will reduce the opportunity for signal reflection, harmonics, ringing, and overshooting digital signals, all of which increase the EMI radiation.
3. Manage Heat
If not properly managed and mitigated in the design phase, heat can diminish board performance and durability. Most electronic components generate heat during use. Most have some tolerance threshold beyond which they can fail.
To manage heat effectively, identify which components generate the most heat in your design. You should distance them from other heat generators and any heat-sensitive components during layout. Use design components such as heat sinks, cooling fans, or thermal vias to remove the excess heat from the board. If you are unsure of heat tolerances, the information on heat generation and sensitivity to heat can usually be found on the component datasheets.
4. Component Placement
After considering functionality, signal separation, EMI, and heat, it’s time to place components on your layout. Here are several important placement considerations:
- Seek to optimize component placements from a design integrity standpoint and increase the assembly yields.
- Shorten the distance of the trace runs as much as possible. This results in less signal loss, faster speeds, and a cleaner overall signal.
- Orient parts in a similar fashion and perpendicular to at least one edge of the PCB if possible and consider the height and width of components.
- When it is feasible, use a stair-step approach to placement to avoid trapping a short component between two taller components.
- If you can, place all SMD components on one side of the PCB unless you really need to use both sides.
- Place all through-hole components on the top side.
5. Power Delivery
Develop a plan for delivery of power to all the necessary parts. It is a good practice to draw power from a plane or a bus. You never want to simply run the power from one component to the next, as that practice can really cause lots of issues with your designs. Also, make sure to use bypass capacitors and low pass filters to ensure that there are no unwanted spikes or outages to critical components.
6. Verify Components’ Footprints
Measure twice, cut once.
You should verify—either on your own or through a library process—that the electronic versions of all components match the physical. Rely on your datasheet during this process to verify that the pad size and pitch are what is documented. The datasheet is also your best tool to confirm that hole size in the footprint not only matches but also considers maximum material condition. Everything has a tolerance so use the worst case for establishing the maximum material condition. There is nothing worse than receiving your boards from the manufacturer and thinking you are ready for assembly, then realizing that either the part in your hand will not fit onto the spot on the board or that the leads for the part will not fit into the hole.
PCB layout isn’t as easy as it might seem. By following a logical process and planning for the inevitable you can increase the likelihood that your prototype will come out as you had designed.
This column originally appeared in the March 2022 issue of Design007 Magazine.
More Columns from Connect the Dots
Connect the Dots: Sequential Lamination in HDI PCB ManufacturingConnect the Dots: The Future of PCB Design and Manufacturing
Connect the Dots: Proactive Controlled Impedance
Connect the Dots: Involving Manufacturers Earlier Prevents Downstream Issues
Connect the Dots: Stop Killing Your Yield—The Hidden Cost of Design Oversights
Connect the Dots: Designing for Reality—Routing, Final Fab, and QC
Connect the Dots: Designing for Reality—Surface Finish
Connect the Dots: Designing for Reality—Solder Mask and Legend