-
- News
- Books
Featured Books
- design007 Magazine
Latest Issues
Current IssueProper Floor Planning
Floor planning decisions can make or break performance, manufacturability, and timelines. This month’s contributors weigh in with their best practices for proper floor planning and specific strategies to get it right.
Showing Some Constraint
A strong design constraint strategy carefully balances a wide range of electrical and manufacturing trade-offs. This month, we explore the key requirements, common challenges, and best practices behind building an effective constraint strategy.
All About That Route
Most designers favor manual routing, but today's interactive autorouters may be changing designers' minds by allowing users more direct control. In this issue, our expert contributors discuss a variety of manual and autorouting strategies.
- Articles
- Columns
- Links
- Media kit
||| MENU - design007 Magazine
Estimated reading time: 2 minutes
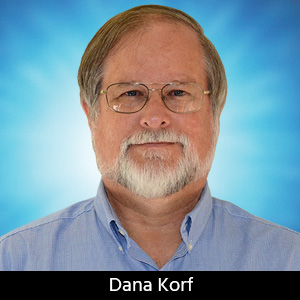
Dana on Data: Is the Customer Always Right?
Is the customer always right when it comes to customer PCB design data? Fabricators would be taking the design data and building the supplied data verbatim if this was true. The fabricator would only need to compensate conductors to account for etching processes and map finished hole sizes to drill sizes.
But, alas, the standard industry practice assumes that the customer data is wrong. Industry data transfer processes assume that the incoming data can’t be built per the supplied documentation. There are all sorts of quality systems, but none of them sufficiently had a positive enough effect on data quality improvement. The industry has accepted this low-quality level as the norm.
We need to fundamentally change our data transfer process. Here are a few reasonable improvement suggestions:
- OEMs create metrics to track data issues and create defect reduction plans for departments and designers
- Fabricator’s charge more for time spent correcting designer design and documentation issues
- OEMs add fabricator-provided design guideline completeness to their supplier qualification and yearly quality audit check lists
- Yearly OEM fabricator quality audit metrics should include a data package quality KPI
- Fabricators should create OEM quality audit metrics for a data package quality KPI
- Corrective actions should be given by the fabricator to the supplier of a bad data package, just like companies that order boards require when the fabricator ships a bad board
- IPC should form a committee to specify a common dielectric constant (Dk, Er) test method used by material suppliers, SI engineers, and fabricator impedance test operations. This would eliminate common impedance test method Dk issues and fabricator fudge factors
- OEMs should quit sending duplicate masters (e.g., Gerber files and fab print dimensions) and use intelligent IPC-2581 data instead
- Designers should update the Revision B design with the approved Revision A DFM comments from the fabricator. The current process assumes that the fabricator edits rev B the same as rev A
OEMs and designers should take this feedback as positive feedback. I don’t know of many designers who enjoy spending time addressing the issues rather than working on the next design. There are cycle time and PCB cost improvements to be made when the supplied database does not require editing.
Companies that implement a true digital twin relationship between design and manufacturing will create a significant amount of data that can be used to improve design manufacturing yields and cost. This will also provide significant feedback that can be used to improve future design rules.
There have many decades of articles written about how to reduce errors. There have been many excellent design software updates created to catch the issues during design. Unfortunately, in parallel with these improvements, fabricator CAM/DFM review systems are also being continually updated to find more complex issues and automate more editing because data is not improving.
The industry is stuck in this loop. It reminds me of the movie “Groundhog Day” in which Bill Murray’s character keeps reliving the same day over and over with the same result. We need leadership from all segments of the data creation, data formatting and data users to work together. We need to change the process to create motivation to break this cycle.
Dana Korf is the principal consultant at Korf Consultancy LLC.
More Columns from Dana on Data
Dana on Data: Best Practices in Interpreting Drawing Notes—‘Use Latest Revision’Dana on Data: The Missing AI-NPI Link
Dana on Data: Merging 2D Electrical, 3D Mechanical Worlds
Dana on Data: Resurrecting IPC Class 1
Dana on Data: The Evolution of Fabrication Drawing
Dana on Data: The Insane PCB DFM Process
Dana on Data: eCAD PCB Design Deficiencies
Dana on Data: Nuke the Netlist