-
- News
- Books
Featured Books
- design007 Magazine
Latest Issues
Current IssueProper Floor Planning
Floor planning decisions can make or break performance, manufacturability, and timelines. This month’s contributors weigh in with their best practices for proper floor planning and specific strategies to get it right.
Showing Some Constraint
A strong design constraint strategy carefully balances a wide range of electrical and manufacturing trade-offs. This month, we explore the key requirements, common challenges, and best practices behind building an effective constraint strategy.
All About That Route
Most designers favor manual routing, but today's interactive autorouters may be changing designers' minds by allowing users more direct control. In this issue, our expert contributors discuss a variety of manual and autorouting strategies.
- Articles
- Columns
- Links
- Media kit
||| MENU - design007 Magazine
Estimated reading time: 4 minutes
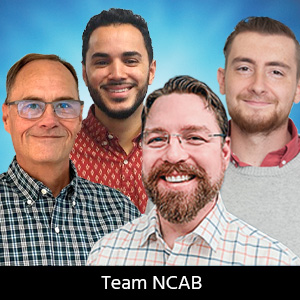
Fresh PCB Concepts: Does the Assembly Process Damage a PCB? (Part 3—Phenolic Epoxy Systems)
In part 2 of this series, I explained how the T260 and T288 material datasheet values could be used as an indicator of how durable a laminate system (FR-4) shall be when exposed to heat. The higher the temperature applied, the less time it takes to delaminate the FR-4. Traditional dicey cured epoxy systems do not stand up to lead-free assembly temperatures as well as one would think. The phenolic cured epoxy systems are much better suited and able to withstand the higher temperatures applied with lead-free assembly temperatures for longer periods of time.
Great! Problem Solved!
Not exactly.
There are some potential challenges to phenolic epoxy systems. Understanding some material properties is the first step in preventing non-conformances or scrap. To begin with, some phenolic cured FR-4 systems can be mechanically weaker than their traditional dicey cured FR-4 counterparts. Table 1 is a comparison between two grades of laminate. Values are taken from a uniform test sample. The values do not represent a finished PCB. These values are as good as it gets. The values you shall see on a finished board shall be lower after you add variables such as the bare board manufacturing process and the actual board design.
Table 1: A comparison between two grades of laminate.
Flexural strength is defined as a material’s ability to resist deformation or rupture under load. It is also referred to as the modulus of rupture, bend strength or fracture strength.1
Peel strength is defined as the average load per unit width required to separate a flexible member from a rigid member or another flexible member.2
The values above are indicators of the materials durability and toughness when exposed to mechanical force or trauma. The phenolic materials can be slightly more brittle and fracture a little more than their dicey counterparts. They can have an increased potential for mechanically induced delamination.
What does this have to do with the assembly process? Quite a lot, actually.
Understanding that the phenolic materials can be weaker and easier to fracture is important.
What operations are affected?
Standoff or Fastener Insertion
There are many different types of standoffs and fasteners that are pressed or swagged into a plated or non-plated hole. The forces applied in the installation process may result in an increased occurrence of haloing about the circumference of the hole. Haloing is mechanically induced fracturing or delamination on or below the laminate surface. In extreme cases, the hole may even rupture or delaminate entirely. Potential solutions may include slightly increasing the hole size, using a different tool or applying gradual amounts of force.
Depanelization
Small printed circuit boards are typically provided to assemblers in the form of a connected pallet or array. Rails may be attached along the edges of the boards with drilled perforations at a break-away tab, a V-score or nothing at all (punched). The process of de-panelizing the board out of the pallet may result in an increased occurrence of non-metallic burrs or haloing along the break edge. In extreme cases the edge may rupture or delaminate entirely. Potential solutions may include applying a deeper V-score or changing the spacing of the drilled perforations at the break point. Use of a CNC routing system to rout through tabs holding the pieces of the array together is an option. The CNC routing process post assembly is becoming more and more popular. The interconnecting tabs can be provided without V-score or drilled perforations. This helps to strengthen and stabilize the array through the assembly process. After component assembly is complete, the array is loaded onto the CNC system, and a router bit is used to cut through the tabs.
Pad Cratering
After a ball grid array collapses in the assembly operation the solder cools down and solidifies. When materials cool down, they contract. The BGA device and board expand in size at different rates when heated. When the BGA device and board cool down they contract at different rates. Lead free solders are also less forgiving regarding elasticity when compared to their tin/lead solder counter parts. This places stress on the connection points. The larger the BGA device, the higher the stress. The stress may result in a laminate fracture that may fail outright or later in the field when the devices is cycled on and off. The pad being soldered can peel from the PCB surface. The potential solution here depends heavily on the design and assembly process. Design changes may include adding as much continuous copper around and under the BGA as possible for dimensional stability to adding stack vias in pads located in the corners of the BGA.
Another source of pad cratering is from the depanelizing process. Breaking a V-scored rail off an assembled PCB requires a bending motion to snap the rail off along the V-scored cutting path. The bending motion can cause the PCB to bow. The bowing motion of the PCB can cause the cratering as the BGA may not bow as easily as the PCB. Placing components further in from the edge of the PCB away from the bow can reduce this from occurring. Cutting the V-score deeper will reduce the amount of force required to snap a rail off and lower the amount of bow on the PCB. Saw cutting through the remaining V-score can eliminate the bow.
Although phenolic cured epoxy systems function better to withstand the higher temperatures than traditional FR-4, the challenges with this material in the assembly process need to be recognized and addressed. The tips I noted above can help during assembly, but if there are further concerns, I always recommend reaching out to your PCB supplier for guidance.
References
- Flexural strength, Wikipedia.com.
- Peel strength, Wikipedia.com.
David Duross is an engineering director for NCAB Group USA.
More Columns from Fresh PCB Concepts
Fresh PCB Concepts: Designing for Success at the Rigid-flex Transition AreaFresh PCB Concepts: More Than Compliance—A Human-centered Sustainability Approach
Fresh PCB Concepts: Assembly Challenges with Micro Components and Standard Solder Mask Practices
Fresh PCB Concepts: The Power of a Lunch & Learn for PCB Professionals
Fresh PCB Concepts: Key Considerations for Reliability, Performance, and Compliance in PCBs
Fresh PCB Concepts: Traceability in PCB Design
Fresh PCB Concepts: Tariffs and the Importance of a Diverse Supply Chain
Fresh PCB Concepts: PCB Stackup Strategies—Minimizing Crosstalk and EMI for Signal Integrity