-
- News
- Books
Featured Books
- design007 Magazine
Latest Issues
Current IssueProper Floor Planning
Floor planning decisions can make or break performance, manufacturability, and timelines. This month’s contributors weigh in with their best practices for proper floor planning and specific strategies to get it right.
Showing Some Constraint
A strong design constraint strategy carefully balances a wide range of electrical and manufacturing trade-offs. This month, we explore the key requirements, common challenges, and best practices behind building an effective constraint strategy.
All About That Route
Most designers favor manual routing, but today's interactive autorouters may be changing designers' minds by allowing users more direct control. In this issue, our expert contributors discuss a variety of manual and autorouting strategies.
- Articles
- Columns
- Links
- Media kit
||| MENU - design007 Magazine
Estimated reading time: 5 minutes
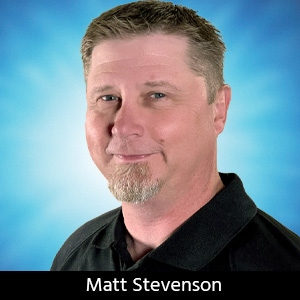
Connect the Dots: Finding Value in Gerber Files
Quick turns are standard operating procedure in the PCB industry, but “measuring twice and cutting once” ahead of the quote process can get your boards into production faster and eliminate costly rework down the line. Gerber files remain a proven method for establishing an uncluttered view of the board design, one that illustrates each layer lined up together, and potentially reveals issues that can slow the quote process or even send designs back for rework.
What Is a Gerber File Anyway?
I am sure that everyone involved in PCB designing, manufacturing, and procurement has heard the term Gerber files at least 100 times. But what is a Gerber file and where did it come from?
The origin of the Gerber file can be traced to Gerber Systems Corp., and founder Joseph Gerber. The company first released Gerber Format: A subset of EIA RS-274-D; Plot Data Format Reference Book in 1981 to promote their vector photoplotters. Later in the 1980s, other plotter companies and CAM systems began to adopt what became the “Standard Gerber” format in the PCB manufacturing industry. Shortly thereafter, Gerber became the de facto data format.
As plotting technology continued to develop to more capable raster photoplotters, the “Standard Gerber” format was extended in 1991 to include polygons and other parameters. With this improvement, users were also able to create shapes of various sizes and shape and polygon area fills without having to draw them in; they could simply be defined with apertures.
In April 1998, Gerber Systems Corp. was acquired by Barco. In September 1998, Barco released the RS-274X format, also known as Extended Gerber Format, to consolidate and unify all the sub-versions that were present in the industry for specific plotter models. This new version quickly took over as the new de facto data format.
Over the years, the 274X format has undergone revisions, improving the format and functions. The most current upgrade to the Gerber format has been the addition of the PCB metadata, giving the data more intelligence than the simple image representation. This current intelligent format is known as X2 and was developed in 2015 by Karel Tavernier, Ludek Bruckner, and Thomas Weyn of Ucamco, the PCB division of Barco.
Gerber may not be the only game in town for designers these days, but the format has been in widespread use for years and it is worthwhile to have an understanding of how Gerber files provide value.
Before You Convert to Gerber, Design Rule Check
You can prevent many issues by using the design rule check (DRC) tool in your CAD software. If you’ve properly configured the DRC tool, it answers questions that would often send a quote request back for more information. Are the layers all there? Are the spaces big enough? Do you have more drill files than copper layers? How are your tolerances?
These answers provide a good foundation for manufacturability, but just because your software will let you design a board in a certain way, that doesn’t mean your fabricator can build it. Think about manufacturability in terms of fabricator capability as you perform your design rule check before converting to Gerber.
Check Your Gerber Files
Converting to a Gerber format provides a more holistic, simplified view of your design. Here are some categorized items you can more easily check for and make changes where needed when viewing Gerber files.
Minimum Feature Size
When you scrutinize minimum feature size and question what the DRC permits, you can:
- Find unintentional neck downs
- Locate places where traces just barely touch pins
- Discover breaks in traces or where ends just barely touch
- See where pads are too small
- Eliminate small traces or features that can needlessly drive up costs
- Validate minimum drill size, locating unnecessarily small drill holes that can also significantly increase costs
Feature Spacing
Solve clearance problems before they occur. Upon viewing the Gerber file, you’ll have a sharper view of spacing types and be better able to recognize clearance problems for:
- Trace/trace
- Pad/pad
- Copper/copper
- Drill/drill
- Drill/copper
- Pad/pad
Look at Each Layer
This is really the only way to visually confirm each is correct. And by doing so, you accelerate the quote process and avoid cost overruns during production of the boards. Before submitting your quote request, consider:
- Does each layer import at correct scale and size?
- Is the number of copper layers correct?
- Are the silkscreen and solder mask layer counts accurate?
- Did the drill file read as intended, as a single file or multiple files? If not, why?
- Was the drill file updated at the same time as Gerber files?
- Do drill holes line up with artwork?
- Were all area fills refreshed just prior to generating Gerber files?
- Did you intend to have potentially expensive blind or buried vias?
Even one misstep in this category can create problems down the road. Though the list may seem long, the potential return on investment of a few minutes can be significant.
Check Solder Mask Layers
When you are double-checking each board layer, pay careful attention to solder mask layers. Oversights here not only can cause delays but result in boards that do not function properly or at all.
- Do all pins have mask openings?
- Vias under components should not have mask openings. Do they?
- Are solder mask openings slightly larger—at least 0.004”—than component pads?
- Are plated through-hole pads 0.015” larger than drill and therefore large enough to avoid breakout?
Leave Plenty of Breadcrumbs for Your Fabricator
Fabricator notes can make the difference between a quick turn and a protracted delay. If file names are just a jumble of numbers or it is unclear about what services are required, the notes are where we can go for guidance.
- Will the fab notes conflict with your order form?
- Do notes call for unnecessary services?
- Do you reference documents that the fabricator does not have access to?
- Does the design service you selected include a technician checking your notes?
Not all quick turn prototyping services offer human intervention. So, if you chose to convert to Gerber, please invest a few minutes in your design and check your files before you engage your manufacturing partner.
This column originally appeared in the October 2021 issue of Design007 Magazine.
More Columns from Connect the Dots
Connect the Dots: Sequential Lamination in HDI PCB ManufacturingConnect the Dots: The Future of PCB Design and Manufacturing
Connect the Dots: Proactive Controlled Impedance
Connect the Dots: Involving Manufacturers Earlier Prevents Downstream Issues
Connect the Dots: Stop Killing Your Yield—The Hidden Cost of Design Oversights
Connect the Dots: Designing for Reality—Routing, Final Fab, and QC
Connect the Dots: Designing for Reality—Surface Finish
Connect the Dots: Designing for Reality—Solder Mask and Legend