-
- News
- Books
Featured Books
- design007 Magazine
Latest Issues
Current IssueProper Floor Planning
Floor planning decisions can make or break performance, manufacturability, and timelines. This month’s contributors weigh in with their best practices for proper floor planning and specific strategies to get it right.
Showing Some Constraint
A strong design constraint strategy carefully balances a wide range of electrical and manufacturing trade-offs. This month, we explore the key requirements, common challenges, and best practices behind building an effective constraint strategy.
All About That Route
Most designers favor manual routing, but today's interactive autorouters may be changing designers' minds by allowing users more direct control. In this issue, our expert contributors discuss a variety of manual and autorouting strategies.
- Articles
- Columns
- Links
- Media kit
||| MENU - design007 Magazine
Estimated reading time: 8 minutes
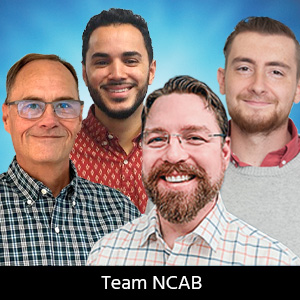
Fresh PCB Concepts: Don't Forget AABUS
Last spring, I wrote a column focusing on cosmetic issues and I asked, “Why does the electronics industry reject good products when it’s not always needed?” In my next column, I turned the coin around and asked if we have understood the workmanship rule correctly: “Printed boards shall be free of non-conformances in excess of those allowed in this specification.” I ended the column by asking, “So, what can we learn from this?”
The most important thing is to know the standard and how to use it. Most people read the measurable requirements, while a requirement like the workmanship rule is left out. Leaving out the workmanship can make it hard to agree, because it requires at least two parties to find a solution that works for both.
This, however, leads us here, where we shall discuss AABUS, what it means, how to handle it, and basically a list of issues that need AABUS.
Why Do We Even Need an Agreement?
First, AABUS means “As Agreed Between User and Supplier.” As already mentioned, an agreement needs two parties, and those two need to find a common solution. The problem with such cases is why we need that agreement. It can obviously be something that can be seen from two sides and end up with a very different understanding if you don’t talk together. However, in the IPC standard it could even be a measurable parameter, but the standard has left the solution to be agreed upon.
So, let's go to the source. We look into IPC-6012E, the performance specification for rigid PCBs and supported by the acceptability standard IPC-A-600K. Reading the first pages of IPC-6012E, the document scope, we find the first reference:
1.3.1.1: Requirement Deviations: Requirements deviation from “these heritage classifications” SHALL be as agreed between user and supplier.
This means, anything you want that is different from IPC Class 1, 2, or 3 shall be specified. Then in 1.3.3.1 we read:
“The procurement documentation SHALL specify those requirements that are a result of the selection process within this specification. This includes ALL references to AABUS. If the requirement selection is not made in the procurement documentation including all related documents, then the default requirements in IPC-6012E Table 1-2 SHALL apply.
Then the standard gives us a selection system, and the default requirements. But frankly speaking, a lot of the requirements are not what you expect or are at least still open for discussion. As an example, the IPC-6012E still specifies solder coating as Sn63/Pb37.
A Burden for the Buyer’s Knowledge
If we now jump to A-600K, the acceptability of the boards you receive, the “approach of this document” says, “This document cannot cover all of the reliability concerns encountered in the Printed Board Industry, therefore attributes not addressed in this issue SHALL be AABUS.” So, using IPC standards for PCBs leaves a substantial burden on the buyer to know the standard and to specify requirements not clearly written in the standard.
Quite a few attributes need to be discussed, unless you simply trust that your chosen supplier will be kind and accept a remake if the boards cannot be used as a result of wrong hole tolerances, or surface finish solderability—just because you did not mention the usage of those boards.
Back to the Workmanship requirement. We find this both in IPC-6012E and A-600K. Where IPC-6012 says, “Printed boards shall be free of non-conformances in excess of those allowed in this specification,” A-600K takes it to the next level stating, “Acceptance of imperfections not specifically covered by this document SHALL be AABUS.”
For the discussion of those imperfections typically referred to by the PCB supplier as “cosmetic issues,” please read my last column, “Attacking the Loophole That Does Not Exist.”
In IPC-6012E you find the term AABUS around 50 times (some are repeated in tables, etc.). In IPC-A-600K, it is mentioned 22 times. What does this tell us? It tells us that we have to be aware. Some of the attributes are not that important for all of us, but you can be sure that you will find some attributes impacting almost every printed board design.
So, What Are the AABUS?
The General One
We already mentioned the selection process within IPC-6012E, paragraph 1.3.3.1, that includes all references to AABUS and any requirement deviation—anything you need that is not mentioned in the standard. Or, if you want to combine IPC classes such as general requirements to Class 2, but copper plating to Class 3.
The Most Important Ones
3.3.1: “When edge spacing is not designed in accordance with IPC-2222, nicks, crazing, delamination and haloing SHALL be AABUS.” If you overlook this rule, you could easily be forced to pay for boards that basically don’t meet your reliability requirements. Many designers are forced to utilise the space to the limit, placing traces closer to the outline that brings the design and the final PCB into this situation. The supplier should warn you, but not if the design meets their capabilities.
3.4: “Printed Board Dimensional Requirements SHALL be defined as per IPC-6012E 3.4 unless otherwise AABUS.” You cannot come after delivery and call for tighter tolerances, or you may end up with a higher unit price based on requirements revealed in the EQ process.
3.4.2: “Annular Ring and Breakout external: The use of teardrop designed pads for class 3 SHALL be AABUS. The same is 3.6.2.9 for inner layer pads.” If you fail to add teardrops, you could end up with inner layer trace-to-pad junction breakout. This could be a true reliability issue causing field error.
3.4.3: “Bow and twist requirements for the array SHALL be AABUS.” This is probably the most overlooked rule in IPC-6012. Most of us believe the bow and twist rule is for the customer panel but it is not, unless this is part of your requirement specification. This also means panel frame design is critical to secure a flat panel even after the first soldering process. And, if you shall be 100% sure, you should specify that bow and twist assessment shall be done after one thermal process. This is even more important if the construction is unbalanced, as mentioned in paragraph 2.3.4, and such requirements will lead your supplier to check the construction.
3.6: “Structural Integrity: A/B coupons shall be used unless AABUS.” This paragraph also leads us to the evaluation of Table 4-2 sampling plan and Table 4-3 acceptance testing and frequency. The supplier will probably not use A/B coupons unless you specify it, or if the supplier has a focus on defense and other industries where customers typically have a focus on these coupons. Coupons are widely used in the U.S., less in Europe, and very seldom in Asia. That means you need to specify if you want the IPC A/B coupons to be used. I would argue for using the PCB itself for lot qualification microsections.
3.6.2.11: “Plating thickness. Deviations to Tables 3-3 through 3-6 of IPC-6012E SHALL be AABUS.” This may very well happen in tight HDI designs! In such cases it is important that your design calculates for thinner copper, and that this is agreed upon with your supplier.
3.6.2.11.3: “Requirements to bumps and dimples in copper filled microvias SHALL be AABUS.” It is quite strange that IPC has chosen not to specify the requirements to a flat surface of copper-filled blind vias. The requirement is there for resin-filled vias, so why not for copper-filled? If your assembly requires a flat surface, you should specify the requirement, or you can refer to IPC-6012EM, the Medical Addendum to IPC-6012, where this is specified.
3.7.1 f: “Solder mask encroachment on rectangular SMT pads with pitch less than 0.65 mm SHALL be AABUS.” Be aware of the challenge to avoid encroachment on rectangular SMT pads, especially when pitch is less than 0.65 mm. Many customers are not aware of this limit in the standard.
3.7.3: “Solder mask thickness requirements SHALL be AABUS.” This is the AABUS most used in PCB specifications and corporate requirements. It is damaging for solder paste printing when solder mask gets too thick, and of course we fear exposed copper if it gets too thin.
3.9.2: “Cleanliness testing after solder mask only when specified.” The standard asks the designer and buyer to specify if such a test is required. The challenge is, the test method specified in IPC-6012E, IPC-TM-650-2.3.25 was designed for process control, and not a proof test of cleanliness on the finished board. I suggest using the specification in IPC-6012DA (revision E comes in 2021).
3.11: “Repair—the allowance and requirements for repair of bare printed board SHALL be AABUS.” Many people, including PCB suppliers, claim that IPC-6012 accepts track welding. This is not correct. It has been the rule for many years that any repair shall be AABUS.
4.3: “Deviation from IPC-6012E Quality Conformance testing SHALL be AABUS.” Very few suppliers follow strictly the quality conformance test requirements as mentioned in IPC-6012E Table 4-4. I recommend checking with your factory to see whether they follow this requirement; if not, find out why. From my experience, some of these tests such as Dielectric Withstanding Voltage, and Moisture and Insulation Resistance, are done once only.
Some of the Rare Ones
Some of the AABUS requirements are very special and rarely used, such as: nickel barrier and electroless gold, electrodeposited tin, lead-free solder coating, and heat sink material. “Deviations to 6012E SHALL be AABUS,” which tells us there are many variations in the market and we cannot have all such variations into a general standard.
Lessons Learned—Good Product Specification
The lesson learned from reading all the AABUS references in IPC-6012E and A-600K tells me that the burden to secure a product in compliance with your requirements and expectations lies in a good product specification, where you have answered most of the AABUS references in the standard.
By doing this, you ensure that the quotation you receive is in compliance with your design and product requirements, and that you avoid unwanted surprises when you receive the first boards.
This column originally appeared in the April 2021 issue of PCB007 Magazine.
More Columns from Fresh PCB Concepts
Fresh PCB Concepts: Designing for Success at the Rigid-flex Transition AreaFresh PCB Concepts: More Than Compliance—A Human-centered Sustainability Approach
Fresh PCB Concepts: Assembly Challenges with Micro Components and Standard Solder Mask Practices
Fresh PCB Concepts: The Power of a Lunch & Learn for PCB Professionals
Fresh PCB Concepts: Key Considerations for Reliability, Performance, and Compliance in PCBs
Fresh PCB Concepts: Traceability in PCB Design
Fresh PCB Concepts: Tariffs and the Importance of a Diverse Supply Chain
Fresh PCB Concepts: PCB Stackup Strategies—Minimizing Crosstalk and EMI for Signal Integrity