-
- News
- Books
Featured Books
- design007 Magazine
Latest Issues
Current IssueProper Floor Planning
Floor planning decisions can make or break performance, manufacturability, and timelines. This month’s contributors weigh in with their best practices for proper floor planning and specific strategies to get it right.
Showing Some Constraint
A strong design constraint strategy carefully balances a wide range of electrical and manufacturing trade-offs. This month, we explore the key requirements, common challenges, and best practices behind building an effective constraint strategy.
All About That Route
Most designers favor manual routing, but today's interactive autorouters may be changing designers' minds by allowing users more direct control. In this issue, our expert contributors discuss a variety of manual and autorouting strategies.
- Articles
- Columns
- Links
- Media kit
||| MENU - design007 Magazine
Estimated reading time: 5 minutes
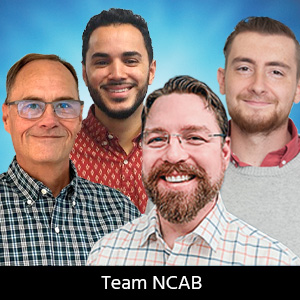
Fresh PCB Concepts: The Benefits of Being a PCB Producer Without Owning Any Factories
With our infrastructure and factory management team based in China, many of our customers ask us why we don’t own any factories. Wouldn’t owning a factory be more cost-efficient? Wouldn’t we have more control over the production process and, therefore, quality? The answer to these questions is simply no. It is part of our long-term strategy and an advantage to our customers that we don’t own any factories. We “own” what is most important: the relationship with the factory. As a result, we are not reliant on technologies and investment. The investments are significant in a factory with expensive equipment and liabilities. And as we don’t own factories, we can be truly impartial—always fitting the best factory to the project.
First, there is the factor of technology. When dealing with a high mix of various products, this comes with a variety of different types of circuit boards that need to be produced. PCB factories cannot produce every type of circuit board, and even if they say they can, it’s not possible for them to be proficient at producing every type of circuit board in a reliable way.
We can attest to this with our long tenure in the circuit board industry. We have seen factories claim they can produce any type of circuit board. However, when we audit the factory, we find they excel with certain types of technologies and within certain volumes. We pay particular attention to process issues or machine capability limitations. By contrast, we approve each factory for the technology and volume they can manufacture reliably, ensuring that we meet performance expectations (Figures 1 and 2).
Figure 1: An example of what PCB factory managers will claim to manufacture.
Figure 2: Once we have audited a factory, we discover there are differences in what they say they can manufacture and what they can manufacture reliably.
We feel it is critically important to stay abreast of emerging technologies. With technology developing exponentially, we have learned that it is impossible for factories to stay up-to-date in all areas. Not only are PCBs trending smaller and more condensed, but frequently, they also require smaller tracks, gaps, and drill hole sizes—all while layer count is increasing, becoming much more complex. A factory may focus on a few types of technologies and invest in new equipment for advanced capabilities, but they can’t be up with it all. To truly stay abreast with emerging technologies, we must always evaluate current factory quality and be on the lookout for new factories (Figure 3).
Figure 3: With tracks, gaps, and drill holes getting smaller and smaller, there are times the factory cannot produce these requirements consistently and reliably. Therefore, we cannot approve them for their promoted capabilities.
While we do diversify our factories, it’s also important to not work with too many. We need to retain our focus, control, and relationships within each one of them. Every year, in all our main factories, we carry out full quality audits that focus on the production process and other related aspects. These are intensive audits, covering eight different functional areas. Further, NCAB also carries out pre-production process audits that look at the front-end processes and associated controls as part of our continuous improvement process.
Within all of our main factories, we identify, evaluate, and select some of the best performing and most experienced employees, including production controllers, customer service resources, pre-production engineers, and inspection teams. Once selected, they will be part of the factories’ teams dedicated to handling, preparing, and controlling NCAB orders from the very start of production, all the way through to final inspection. Each team member receives a minimum of 40 hours of specialized training per year.
Of course, problems do arise. That is inevitable when working with a complex production process containing many steps and materials. And businesses have cycles. Priority number one when unforeseen problems arise is to keep your supply chain running without risk of further defects. When issues occur, NCAB performs an exhaustive analysis investigation in one of our laboratories and/or within the production process so we may identify the root cause and implement both corrective actions, as well as preventative actions to the eliminate risk of future reoccurrences. Being onsite means that we can provide continuous communication, so all parties are aware of the progress being made to resolve the problem and provide updates on recovery activities.
Why do our partners allow us all of this access? One major reason is that we, in turn, help them. When we identify a problem and act as consultants with them, their overall manufacturing and quality control processes will improve. Frequently, our quality audits will reveal issues that could cause problems down the road with not only us but other partners.
Then comes external, unexpected, or global factors. What if there’s a fire, natural disaster, government or political issue, or a virus outbreak, like the COVID-19 outbreak? You need flexibility. If a factory is not able to produce, then where do you go? We always make sure our factory base is diversified so that we have several factories to choose from for each type of technology to meet our customers’ needs at any time.
What about prototypes? We have found that there are a number of differences in capabilities between prototype-oriented factories and those that are volume-oriented factories. For example, we can see that the differences in the order mix, the engineering capacity, and even the type of equipment within the factories can be the difference between success and failure in the supporting of prototypes. Only through having such production knowledge within our factory team can we make the correct evaluation of who is best suited or set up to support prototype demands. We work seamlessly with our prototyping and volume production partners to ensure a smooth transition. We have 10 dedicated prototype/quick-turn partners among our 23 factories that complement the full range of our PCB portfolio.
We also aim to contribute to 10–30% of total capacity with all of the factories we work with. With our combined global presence in 45 different markets and $190M purchasing power, we are uniquely positioned to negotiate pricing, lead times, material selection, and quality standards on your behalf. We even have one of our largest global sales teams located in China. With all these added benefits, we are still able to sell PCBs directly to customers in China. They know from their own experience all the added value that comes from not owning a factory and our overall factory management strategy.
Jeff Beauchamp is a field application engineer at NCAB Group.
More Columns from Fresh PCB Concepts
Fresh PCB Concepts: Designing for Success at the Rigid-flex Transition AreaFresh PCB Concepts: More Than Compliance—A Human-centered Sustainability Approach
Fresh PCB Concepts: Assembly Challenges with Micro Components and Standard Solder Mask Practices
Fresh PCB Concepts: The Power of a Lunch & Learn for PCB Professionals
Fresh PCB Concepts: Key Considerations for Reliability, Performance, and Compliance in PCBs
Fresh PCB Concepts: Traceability in PCB Design
Fresh PCB Concepts: Tariffs and the Importance of a Diverse Supply Chain
Fresh PCB Concepts: PCB Stackup Strategies—Minimizing Crosstalk and EMI for Signal Integrity