-
- News
- Books
Featured Books
- design007 Magazine
Latest Issues
Current IssueDesigning Through the Noise
Our experts discuss the constantly evolving world of RF design, including the many tradeoffs, material considerations, and design tips and techniques that designers and design engineers need to know to succeed in this high-frequency realm.
Learning to Speak ‘Fab’
Our expert contributors clear up many of the miscommunication problems between PCB designers and their fab and assembly stakeholders. As you will see, a little extra planning early in the design cycle can go a long way toward maintaining open lines of communication with the fab and assembly folks.
Training New Designers
Where will we find the next generation of PCB designers and design engineers? Once we locate them, how will we train and educate them? What will PCB designers of the future need to master to deal with tomorrow’s technology?
- Articles
- Columns
Search Console
- Links
- Media kit
||| MENU - design007 Magazine
Estimated reading time: 6 minutes
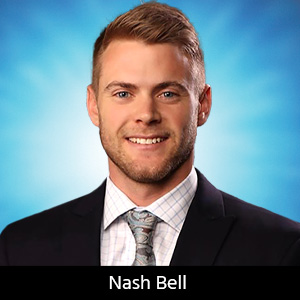
Knocking Down the Bone Pile: Basics of Component Lead Tinning
The component lead tinning process serves several critical functions, including removing gold plating, mitigation of tin whiskers, reconditioning of component solderability issues, and alloy conversion from lead-free (Pb-free) to tin-lead or from tin-lead to lead-free for RoHS compliance. We will cover each of these topics in more detail in upcoming columns.
Traditionally, some in the electronics assembly industry have utilized a single static solder pot for manual lead tinning. While typically performed as a secondary operation prior to board assembly, this may appear to be economical but has several disadvantages from a quality standpoint.
The use of a single static solder pot for both removal of an original alloy as well as component re-tinning should be avoided. This is not a recommended practice since dross, organic contaminants, flux residue buildup, and accumulation of gold can be transferred to the re-tinned component leads or terminations. Those using this practice rely on outdated standards and procedures that are not in compliance with the GEIA-STD-0006 component re-tinning industry requirements.
A manual re-tinning process typically involves a technician dipping a through-hole or surface mount device multiple times into a static solder pot to remove the original lead finish. This is followed by preheating the components on a hot plate, then manually applying RMA flux to the leads before moving each component into the same static solder pot for re-tinning.
When component leads are manually tinned, several issues can arise. The manual tinning process may not create a high-quality intermetallic bond on the lead, leading to a poor base metal and a rough surface finish. When soldering to a printed circuit board, the solder can initially wick up the lead and wet the plated through-hole. However, once the re-tinned surface becomes liquidus, the solder may partially run back down or migrate away from the lead, resulting in de-wetting at the targeted soldering temperature. Thus, the de-wetting at the joint site and poor solderability can often be traced to irregularities from the manual tinning process that negatively impact the intermetallic bond.
An additional disadvantage of using a single solder pot is the risk of contamination. Since there is no circulation within a static solder pot, the composition of the surface level solder is dependent on the specific gravity of the elements present. This is especially problematic when using a static pot to perform both alloy removal and refinishing of a component’s leads. If the original lead finish is gold-plated, the gold can dissolve into the static pot, potentially altering the composition of the solder alloy. Furthermore, a static solder pot, as seen in Figure 1, may contain other contaminants, such as dross, RMA flux residues, and oxidation on the surface, which can negatively impact solderability.
Another drawback of repeatedly using a single static solder pot is that organic contaminants, such as mold release agents, can float on the surface of the molten solder. These agents will not be driven off by heat unless temperatures exceed 500°C. The presence of these organic contaminants in the static solder pot can be verified using either atomic absorption (AA) analysis or infrared spectrophotometry with Fourier transform (FTIR).
The surface of manually re-tinned pins often appears to have a rough finish as seen in Figure 2. This is indicative of an uncontrolled lead tinning process due to impurities such as excessive dross, flux residues, and non-optimized immersion dwell and extraction speed.
Figure 3 shows an example of random surface anomalies on the resulting solder joints. These irregularities can be described as alligator skinning, voids, and blow-holes which are more likely to occur with a manual tinning process and are considered solder defects per IPC J-STD-001.
The ideal method to facilitate re-tinning of surface mount or through-hole components is to use the robotic hot solder dip (RHSD) process. It is recommended that this re-tinning operation be carried out using a lead tinning machine utilizing precise flux application, controlled preheating, dual solder pots, nitrogen inerting, and defined process control. A defined process of this type is highly recommended in lieu of manually dipping components into a single static solder pot to reduce solder contamination, minimize non-wetting issues, and enhance solderability.
The RHSD component lead tinning process utilizes two separate solder pots. The first is a cleansing bath of molten solder to remove the original solder coating, unwanted plating, and any residual contaminants. Next, the component leads are preheated and fluxed, followed by a final immersion in a clean solder bath of pure eutectic solder. This provides a homogeneous intermetallic layer with the base metal of the component leads, which increases the overall solderability, thus facilitating improved reliability of printed circuit board assemblies.
All types of through-hole and surface mount components can be re-tinned using the robotic hot solder dip process.Surface mount components with terminations or pads without leads, such as chip components, SOTs, SOICs, LCCs, and PLCCs can be re-tinned using the solder drag process. In many cases fixturing may be required when automatically re-tinning surface mount components to ensure consistency is maintained during the re-tinning process.
Formed multi-side components such as FP and QFP devices, have very delicate leads that can be easily damaged. These are typically re-tinned using a side wave process with the components held in position by a multi-axis articulated robot equipped with a rotary vacuum head.
A key issue when re-tinning fine-pitch surface mount devices such as QFPs and no-lead QFNs is to maintain coplanarity across all leads to ensure consistent solder distribution and limit the potential for bridging. X-ray fluorescence (XRF) testing can be used to verify solder thickness, in addition to alloy composition, when determining if a coplanarity issue exists.
Fine-pitch QFPs pose certain challenges but can be successfully tinned with proper process controls in place. These components may range from 6 mm x 6 mm up to 50 mm x 50 mm with a lead pitch as small as 0.012" making the margin for error very small. Given the tight spacing and delicate nature of these leads, there is the potential for bridging and lead damage when tinning these types of components. Using a controlled automated system with these fine-pitch components will provide significant improvement in achieving consistent and reliable outcomes with limited defects.
Following the robotic hot solder dip process, all re-tinned devices should be cleaned in a batch wash or cleaning system, using the appropriate solvent or aqueous cleaning agent to remove any residual flux residues. Subsequently, components should be dry baked for the applicable component moisture sensitivity level (MSL). This should be followed by solderability testing per J-STD-002.
Ultrasonic cleaning is another common cleaning method that should be used cautiously. Semiconductor devices can be potentially damaged by cavitation resulting from certain frequencies in ultrasonic cleaners which is unsuitable for cleaning electronic components. Ultrasonic cleaners meant for other applications, such as cleaning of small mechanical parts, should not be used for cleaning these components. If an ultrasonic cleaner is used, it should be a continuous variable frequency (CVF) type designed specifically for cleaning of electronics.
In conclusion, the component lead tinning process is essential for enhancing solderability and ensuring the reliability of electronic assemblies. While traditional manual methods using a single static solder pot may seem cost-effective, they are fraught with challenges that can negatively impact the quality of work, including the transfer of contaminants and the creation of de-wetted solder joints.
To achieve optimal results, employing advanced techniques like the robotic hot solder dip process is strongly recommended. This method provides better control over the re-tinning process, safeguards against contamination, and ensures a consistent, high-quality intermetallic bond. By adhering to industry standards and utilizing proper equipment, manufacturers can significantly improve solderability and reliability, ultimately leading to more dependable electronic components and assemblies.
Future columns will delve deeper into each aspect of the lead tinning process, providing further insights, and best practices to enhance quality and performance in the assembly of electronic devices.
This column originally appeared in the April 2025 issue of SMT007 Magazine.
More Columns from Knocking Down the Bone Pile
Knocking Down the Bone Pile: Package on Package Rework—Skill RequiredKnocking Down the Bone Pile: 2023’s Top Challenges in BGA Rework
Knocking Down the Bone Pile: Eliminating Solder Balls in Hand Soldering
Knocking Down the Bone Pile: Opening a Trace on the Surface of a PCB
Knocking Down the Bone Pile: Soldering for QFPs and Other Gull Wing Leaded Parts
Knocking Down the Bone Pile: Reworking of SMT Connectors with Center Ground Connection
Knocking Down the Bone Pile: Solder Mask Repair Techniques for PCB Repair
Knocking Down the Bone Pile: Humidification for ESD Control in PCB Rework/Repair