-
-
News
News Highlights
- Books
Featured Books
- design007 Magazine
Latest Issues
Current IssueLearning to Speak ‘Fab’
Our expert contributors clear up many of the miscommunication problems between PCB designers and their fab and assembly stakeholders. As you will see, a little extra planning early in the design cycle can go a long way toward maintaining open lines of communication with the fab and assembly folks.
Training New Designers
Where will we find the next generation of PCB designers and design engineers? Once we locate them, how will we train and educate them? What will PCB designers of the future need to master to deal with tomorrow’s technology?
The Designer of the Future
Our expert contributors peer into their crystal balls and offer their thoughts on the designers and design engineers of tomorrow, and what their jobs will look like.
- Articles
- Columns
Search Console
- Links
- Media kit
||| MENU - design007 Magazine
Estimated reading time: 3 minutes
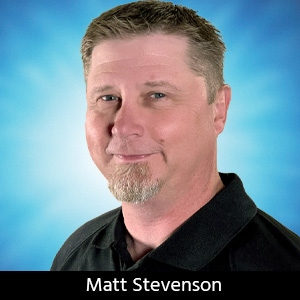
Connect the Dots: Designing for Reality—Routing, Final Fab, and QC
In the previous episode of I-Connect007’s On the Line with… podcast, we discussed several commonly used surface finishes, laying out the unique properties, the application process, and the associated pros and cons. Our final steps in the manufacturing process include routing, final inspection, and shipment.
Boards are ready for assembly, except they are still in panel form. How do we break all these boards apart? PCBs usually need to be removed from the manufacturing panel. Even if some boards stay in a sub-panel for assembly, we need to remove the outside frame.
There are instances where the customer prefers to receive their order in panel form and break the boards out down the road, but most of the time, this is done after the manufacturing process. This enables us to put finished edges on the PCBs and add tabs for tab-routed boards.
Routing Options
The most common method is to rout the individual board into its singulated format. For example, if the design calls for 3x3 boards, we cut them to meet those specifications, and the customer receives stacks of individual 3x3 boards.
Routing boards is like routing wood. We use a spinning cutter on a computerized numerical control (CNC) machine that cuts into the panel following the outline of the board. This is the most cost-effective and efficient way to break apart a panel of PCBs.
For smaller production runs where assemblers work by hand one at a time in a shop, routing individual boards is fine. Assemblers manufacturing at scale are always looking for production efficiency. They often prefer to receive the boards in panel form or at least with some real estate around the edges of the boards because they need to clamp the boards into their conveyor system for the automated placement of components.
Individual boards do not run through their pick-and-place (P&P) machines effectively. If there is circuitry and assembly near the edges, there is no room to clamp the boards to these conveyors. The assembler can use a jig or fixture to hold the board during assembly, and this often requires multiple manual setups that can slow an automated assembly process.
Partial or tab routing is an option. We add a frame around a handful (or more) of boards on the panel and rout around the group. This allows the assembler to clamp onto the frame, cut into it, and have fiducials that allow their vision systems to align to the board registration for automated assembly.
V-scoring is another option that allows multiple boards to be assembled. Adding a score line along the board outlines allows the boards to be broken or cut apart after assembly. This doesn’t apply to parts that overhang the board edge unless someone adds them after singulation.
Designers should communicate their routing preferences to the manufacturer at the outset and document those requirements in the design notes and fabrication and assembly prints.
Laser De-paneling
Lasers are accurate, and laser routing is an excellent option when a customer’s requirements are ±1 mil on the board dimension or slot width. This can be expensive and time-consuming, but it’s useful with the tight dimensional tolerances often present in smaller, more complex board designs.
Verification and Inspection
We have now reached the final stages of production. The boards or panels head to the quality control department. This team is responsible for verifying the boards meet all the print requirements, the IPC class requirements, have the right surface finishes, are the correct dimensions, and comply with any other material requirements.
The shipment includes inspection results (testing and impedance data) and other verification forms. Boards undergo a final visual inspection to confirm:
- No copper is exposed
- All pads have a surface finish
- There is no dewetting (solder losing surface adhesion)
- The correct cutouts are added
- There is no damage to the board
Once we are certain all the design requirements and quality standards have been met, it is ready for shipment. The boards are then packaged to ensure they don’t get damaged, and then head to the customer or assembler.
I encourage you to explore the PCB manufacturing process in greater depth by reading my book, The Printed Circuit Designer’s Guide to… Designing for Reality. You can listen to the podcast here.
This column originally appeared in the February 2025 issue of Design007 Magazine.
More Columns from Connect the Dots
Connect the Dots: Designing for Reality—Surface FinishConnect the Dots: Designing for Reality—Solder Mask and Legend
Connect the Dots: Designing for Reality: Strip-Etch-Strip
Connect the Dots: Designing for Reality—Pattern Plating
Connect the Dots: Designing for Reality—Outer Layer Imaging
Connect the Dots: Designing for Reality—Electroless Copper
Connect the Dots: Navigating the Intricacies of PCB Drilling
Connect the Dots: Designing for Reality—Lamination and Materials