-
- News
- Books
Featured Books
- design007 Magazine
Latest Issues
Current IssueTraining New Designers
Where will we find the next generation of PCB designers and design engineers? Once we locate them, how will we train and educate them? What will PCB designers of the future need to master to deal with tomorrow’s technology?
The Designer of the Future
Our expert contributors peer into their crystal balls and offer their thoughts on the designers and design engineers of tomorrow, and what their jobs will look like.
Advanced Packaging and Stackup Design
This month, our expert contributors discuss the impact of advanced packaging on stackup design—from SI and DFM challenges through the variety of material tradeoffs that designers must contend with in HDI and UHDI.
- Articles
- Columns
Search Console
- Links
- Media kit
||| MENU - design007 Magazine
Estimated reading time: 5 minutes
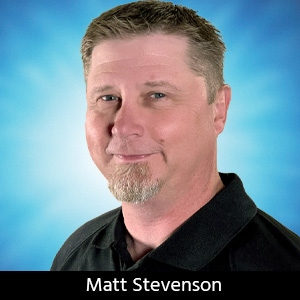
Connect the Dots: Designing for Reality—Surface Finish
In the previous episode of I-Connect007’s On the Line with… podcast, we discussed the solder mask and legend process, one of the final steps in the PCB manufacturing process. The board is nearly complete. We just need to wrap up production by applying a surface finish to protect the copper from oxidation and facilitate soldering components onto the board.
Copper oxidizes quickly, so all the exposed solderable pads are susceptible to oxidation. This can limit the effectiveness of component soldering. Applying surface finish to the solder pads will affect solderability during assembly to a limited extent, but today’s surface finishes are produced with solderability in mind and are needed to sustain the productive life of the board.
Surface Finishes
Designers should consider the following when establishing surface selection criteria:
- Cost
- Restriction of hazardous substances (RoHS)
- Flatness of the board surface
- Solder joint integrity
- Shelf life
- Wire bondable (if applicable)
With more boards needing to accommodate larger components and more leads over multiple edges or surfaces, flatness becomes one of the more critical manufacturability considerations. Surface finish plays a large role in those instances.
There are five commonly used surface finishes, plus several others used for specialty applications. The five are:
Hot Air Solder Leveling (HASL)
HASL has been around for a long time and many industries rely on it, most notably the defense industry. HASL’s long and successful history is associated with the adage, “Nothing solders quite like solder.” HASL has been around the longest and is still one of the most widely used surface finish methods. It is cost-effective, durable, and reliable. It also has a long shelf life (the duration that the board can sit in inventory waiting for assembly) and provides great solderability.
However, HASL does have drawbacks. It often leaves a lack of flatness on the board that can be problematic during assembly. There is also lead (Pb) in the HASL surface finish, which is not compatible with RoHS requirements. However, there is also a Pb-free HASL option. Designers should also consider the number of surface mount components their board must accommodate before choosing HASL. If there are more than eight pads per side on an integrated circuit with a lot of leads, flatness becomes an issue.
Immersion Silver
Immersion silver provides a very flat surface finish. It is a thin deposit that closely follows the contours of copper. It has a good grain structure, creating exceptional flatness and planarity.
Comparing HASL with immersion silver is essentially contrasting old school with new school. We often recommend immersion silver over HASL because it creates the best solder joint. It can withstand vibrations, is hospitable to surface mount components, and is cost-effective.
Like your grandmother’s silver flatware, boards treated with immersion silver surface finish can be susceptible to heat, humidity, or UV light. They will tarnish if left out in the elements. You should store and package boards with an immersion silver surface finish that won’t be going directly to assembly as you would a moisture-sensitive component.
Electroless Nickel Immersion Gold (ENIG)
ENIG is a two-layer coating. The first layer is nickel, electrolessly deposited atop the copper, and then a layer of gold is immersion plated on top of the nickel. It includes two layers because nickel is a metal that, in its pure form (like it is here), passivates (becomes unreactive) in oxygen. The layer of gold on top protects the nickel from oxidation.
Tin from the solder and nickel from the surface finish create the solder joint. This intermetallic is different from the copper–tin created with other finishes and has pluses and minuses, but it does produce solid solder joints for most applications. Like immersion silver, ENIG creates a flat surface but is slightly thicker than immersion silver. The main issue with ENIG is cost. Gold is among the most expensive raw materials, and the electroless immersion process is more costly than other surface finish application processes.
Electroless Nickel Electroless Palladium Immersion Gold (ENEPIG)
ENEPIG is essentially the same surface finish as ENIG, but with a layer of palladium added between the nickel and the gold. ENEPIG allows gold leads to be wire-bonded to the pads. This method is used for specialized applications that require wire bonding and is typically called out in the design specs. ENEPIG has the same cost considerations as ENIG, plus those associated with adding the palladium layer, which can also create solderability issues that may impact board durability and operability.
We recommend using ENEPIG surface finish only on the parts of the board where it is necessary and using ENIG for all other solderable surfaces. This can help contain costs, improve manufacturability, and avoid issues with board function.
Immersion Tin
This method is like immersion silver. The result is a very flat and very thin surface finish that is cost-effective and has a relatively long shelf life. Immersion tin has low insertion friction, making it a viable option where you have press-fit connectors. Though “nothing solders like solder,” the introduction of tin makes this a very solderable surface finish.
Immersion tin is more vulnerable to environmental conditions than immersion silver surface finish. Use boards treated with immersion tin promptly or store them with environmental concerns in mind.
People use other surface finish methods beyond these five for more specialized applications or to keep production costs down. Some of the more noteworthy ones are:
- Electrolytic nickel with hard or soft gold
- Electroless palladium immersion gold (EPIG)
- Organic solderability preservative (OSP)
For a deeper dive into these three specialty surface finishes, listen to the Designing for Reality: Surface Finish episode of On the Line With… and keep an eye out for my last article in this series that discusses routing, final fab, and quality control. If you can’t wait to learn how the story ends, check out Episode 12.
One Board, Multiple Surface Finishes
Designers can direct manufacturers to use multiple surface finishes. In the print, you can specify one surface finish for a specific area on the board and use one or more additional finishes on the balance of the board.
A surface finish combination makes sense in several situations, such as when a board uses press-fit connectors rather than soldering in one area and gold wire-bonding components in another.
Download Matt's book, The Printed Circuit Designer’s Guide to… Designing for Reality and listen to the podcast here. You can view other titles in the I-007eBooks library, here.
This column originally appeared in the January 2025 issue of Design007 Magazine.
More Columns from Connect the Dots
Connect the Dots: Designing for Reality—Solder Mask and LegendConnect the Dots: Designing for Reality: Strip-Etch-Strip
Connect the Dots: Designing for Reality—Pattern Plating
Connect the Dots: Designing for Reality—Outer Layer Imaging
Connect the Dots: Designing for Reality—Electroless Copper
Connect the Dots: Navigating the Intricacies of PCB Drilling
Connect the Dots: Designing for Reality—Lamination and Materials
Connect the Dots: Designing for Reality—The Physical Manufacturing Phases