-
- News
- Books
Featured Books
- design007 Magazine
Latest Issues
Current IssueShowing Some Constraint
A strong design constraint strategy carefully balances a wide range of electrical and manufacturing trade-offs. This month, we explore the key requirements, common challenges, and best practices behind building an effective constraint strategy.
All About That Route
Most designers favor manual routing, but today's interactive autorouters may be changing designers' minds by allowing users more direct control. In this issue, our expert contributors discuss a variety of manual and autorouting strategies.
Creating the Ideal Data Package
Why is it so difficult to create the ideal data package? Many of these simple errors can be alleviated by paying attention to detail—and knowing what issues to look out for. So, this month, our experts weigh in on the best practices for creating the ideal design data package for your design.
- Articles
- Columns
- Links
- Media kit
||| MENU - design007 Magazine
New EDA Tool Company Embraces AI and Code
February 19, 2025 | I-Connect007 Editorial TeamEstimated reading time: 10 minutes
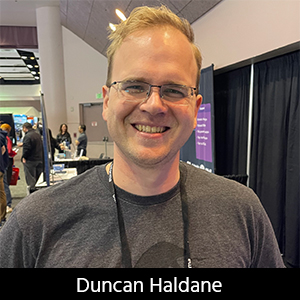
At DesignCon 2025, we met with Duncan Haldane, CEO and co-founder of the EDA software company JITX, based in Berkeley and San Jose, California. This PCB design tool runs on AI and software code, which Duncan says can accelerate your design cycle by up to 25x.
We asked Duncan to explain how this software came to be, how it works, and what this could mean to the future of PCB design. The industry is lucky to have young people like him who don’t know that launching an EDA company is supposed to be difficult.
Andy Shaughnessy: Duncan, it’s nice to meet you. Tell us about JITX, walk us through how “code-led” software functions, and how the tool uses AI.
Duncan Haldane: JITX is a code-based EDA tool. It's a full-stack tool. Basically, you put in the requirements as a code: “Your design should do this and shall comply to this.” When you run that code, it produces a schematic and a layout, solving all the problems of circuit design and supply chain, as well as now layout as part of that automation. We don't treat this as a “push button AI expert to make my whole design for me.” It's much more like an interactive tool meant to be used by experts to help them be better. A new aspect of AI has been coming into these tools lately. These large language models like ChatGPT or DeepSeek can write code for you, and read PDFs and emails. You can take all the data that usually sits around during the board design process, across different teams and sites, and use that data to write code, which then creates your design.
That code part is really important because it’s where you get precision. It is not good to have a board design that's not manufacturable, or doesn't meet SI or PI. The AI models do not give you that explainability or precision, but code does. So, you have this flow where you go from high-level design through AI into code, and then on the layout side, we have a bit more AI that helps with physical design optimization. We've been doing things like showing 10x productivity on memory layouts, and also making designs more miniaturized than humans are able to complete on their schedules. We can do a lot more optimization behind the scenes.
Shaughnessy: Do you need to know how to use code, or do you have an editor for it?
Haldane: It's a mixture of both, sort of like a scripting interface. Many electrical engineers will script whatever they can in their CAD tools, so we made it like a simplified interface. If you use AI, then you just have a natural language to see this design. I'm not a software guy. I was in mechanical engineering, before I got into electrical. I'm not a software developer, but I can very easily use this interface.
Kelly Dack: Can people come to you and request solutions for a certain application that may not be related to designing the circuit board? For instance, we’re looking for a best-value panel solution for our customers’ PCBs. At my job, we’re collecting data from our suppliers, manufacturers, and other stakeholders in the PCB industry. We'd like to take that data and put it all together so that we press a button and develop a solution that will provide the best value for all PCB manufacturing stakeholders.
For instance, what is the best way to put a panel configuration together based on material thickness, density, and components? Should it be a 6 x 8 array, or a 2 x 4 array? A larger array may reduce the cost of the assembly work but it may lower the yield on the supplier’s manufacturing panel and drive up the cost of the individual bare boards. Each supplier has different cost adders for routing, punching, and V-score. These variables play into a matrix of trade-offs that could be analyzed and modeled for lowest cost vs. manufacturing ease and performance, which for us equates to best value. We're thinking that we may be able to press a button and come up with the optimum, best-value panel solution. Is that possible?
Haldane: We are in a phase where we work really closely with our early customers and we have a large design platform. The goal is to take all design considerations from requirements through electrical, SI, PI, thermal, mechanical, DFM, and DFX, and just smoosh them into one tool that allows you to do an actual search. I have a demo that shows how a designer can say, “Here's my high-speed SERDES and I'll just pop a mounting hole in the middle.” Everything updates and all the phases are automatically compensated. You have SI closure, and it's live. If you think about electromechanical integration like that, it works really well.
Kelly, in your case, if you have your panels sketched out, then you're iterating live on the layout and saying, “Can I make this work?” You might want to iterate stackup, materials, and rule sets at the same time to figure out the best overall solution. That's what this tool is for. You should be able to optimize in a tool instead of on a whiteboard.
Dack: Is JITX something we subscribe to or purchase?
Haldane: We are an EDA tool company with term-based licensing, and for larger customers, we do site-based licensing. You don't have to work with us very closely, unless you want to. We also have what I call “self-serve” because many of the newer engineers don't want to talk to anyone. They say, “Just give me the tool.”
Shaughnessy: Does your tool integrate the relevant fab and assembly data as well?
Haldane: Yes. If you design a board that can't be fabricated, you haven't actually done anything useful. It turns out that your layer alignment at the factory will have a pretty big impact on some SI designs. Your ground plane might disappear, and if that's not in your model, then you actually don't have a design. It’s much worse when you find out about the problem at the factory. How far up they can kick that problem is a measure of how good your team is functioning. But I believe that if you want to actually do better hardware design, you have to include all of the fab and assembly information.
Shaughnessy: Does this tool start with the schematic?
Haldane: You can. You can import schematics into JITX, then we add some smarts from the code, saying, “You've done this memory schematic before. It's a big board with more than 30 layers, and we might have to do a bunch of pin swaps to make this happen.” Then we use AI to add that smarts, “What's the pin assignability on this memory controller?” We have live pin swaps in the router. Sometimes, we’re able to take the four memory layers we thought we needed and get it down to three. That level of optimization is what you get from code. You can import pre-existing data, add some smarts on top, and then start working with it. When we export, you can either send it to ODB++ or back into native CAD.
Shaughnessy: Is ODB++ the preferred output? What about Gerber?
Haldane: We don’t do Gerber. It looked like a pain and ODB++ worked so well. We wanted to do IPC-2581, but not enough people were using it, so we picked ODB++ first. We also write out the schematic as well. Like when we export to CAD, we write it out like a whole CAD package.
Shaughnessy: Does the tool have an autorouter? Many designers refuse to use them.
Haldane: Yes, we have a new autorouter that fixes the three primary problems with autorouting. The first problem is thinking, “I'll push a button, the board will be routed, and I've already done my placement perfectly.” That's not the way any human designs. The second problem is that it's a pain to set up. We’ve actually automated the setup. So now I can call a single line of code and it sets up like, “Here are all of the constraints for my six DDR7 memory chips.” The third is clean-up; we’ve made this zero cleanup. This router puts down extremely high-performance geometry, including for SI and RF, and it does so natively. It will do a better job of routing than you can do in any other CAD tool. You probably won't want to touch it, but of course, you can, it will just be native data. The autorouter does all the curves and the precise femtosecond length matching. It makes the job much easier.
Shaughnessy: Do experienced PCB designers need any special training to use JITX?
Haldane: We’ve tried to make it as “out of the box” as possible. We have a series of videos that help users go from zero knowledge to designing a gigabit ethernet switch in less than a week. We’ll offer as much support as users need.
Shaughnessy: Is this your first entrepreneurial endeavor?
Haldane: Yes. Before this, I was getting my Ph.D. in robotics at Berkeley. My was a research scientist, and spent all my time as a hardware designer, building robots as scientific tools, which I found really rewarding. But I did get a chip on my shoulder about hardware design because I had just enough smarts in my head to put shapes on the screen—but that was all I could do. I would draw stuff, and didn't get to reuse anything. I would draw my mechanicals, take my drawings to the shop, and I wanted to make this shape. But I had nothing about how it would be made, what made it good, or what I could reuse. Then I met my co-founders, and they were automating chip designs. They did a project called Chisel, which Google used to tape out the TPU. It's like a new way to do digital logic design with a modern programming language instead of something like Verilog or Spice.
I thought, what if we took that and applied it to all the design and manufacturing on the planet? You take hardware engineering and turn it into something reusable that actually enables optimization. If you look at all the papers about chip design optimization, it’s all about trade-offs. We may have power performance in one area and see, “Here are all the trade-off curves.” We don’t get that in the package and board. Instead, we'll take a sequence of steps, see that each one locally looks good, and then we'll try to make it through on schedule.
Shaughnessy: You’re doing this using AI?
Haldane: We use a lot of AI to make this happen. We use AI to build solvers that connect your entire design flow together. With this, I can say, “Length match is within a femtosecond” and it will put down a shape. Any technology is about what it does for you. The solvers are what let you actually put all that together. AI is one of those, and it's a big one on the front end, especially for writing code. AI is useful for something like taking an organization's worth of information about how to do design that they've collected over the years and turning it into an active design tool and a platform where people can collaborate. That's what AI is for.
Dack: That's where the data coming in from the other stakeholders makes the best value design.
Haldane: Yes. Then you put it all together. What if this design is impossible, and you have to change your requirements? I know you want 60dB here. It won’t happen, guys, and you can actually show the designer, “If you change this, you can do this, change this or do that, but this is what it will take to work.” That collaboration happens when you give everybody a place to land in a design platform that you can actually optimize.
Shaughnessy: What’s next for JITX?
Haldane: It's always more optimization. From talking to customers, we know that they always want to design more complex boards, so we've done things to help them like package/board co-optimization. How do you define everything for the signal integrity channel? Bigger designs, more automation. That will be our goal forever, because everybody wants to design complex boards better.
Shaughnessy: Thanks for speaking with us, Duncan. Best of luck.
Haldane: Thank you, Andy and Kelly.
Testimonial
"We’re proud to call I-Connect007 a trusted partner. Their innovative approach and industry insight made our podcast collaboration a success by connecting us with the right audience and delivering real results."
Julia McCaffrey - NCAB GroupSuggested Items
Elementary Mr. Watson: Closing the Gap Between Design and Manufacturing
07/23/2025 | John Watson -- Column: Elementary, Mr. WatsonModern PCB designers are not merely engineers or technicians. I believe that PCB design, at its core, is an art form, and modern PCB designers should be considered artists. Beyond the technical calculations and engineering rules lies a creative process that involves vision, balance, and a passion for what we do. Like any artist who works with brush and canvas or chisel and stone, a PCB designer shapes invisible pathways that bring ideas to life. Each trace, layer, and component placement reflects thoughtful decisions that blend form, fit, and function.
Designers Notebook: Basic PCB Planning Criteria—Establishing Design Constraints
07/22/2025 | Vern Solberg -- Column: Designer's NotebookPrinted circuit board development flows more smoothly when all critical issues are predefined and understood from the start. As a basic planning strategy, the designer must first consider the product performance criteria, then determine the specific industry standards or specifications that the product must meet. Planning also includes a review of all significant issues that may affect the product’s manufacture, performance, reliability, overall quality, and safety.
Microchip Enters into Partnership Agreement with Delta Electronics on Silicon Carbide Solutions
07/18/2025 | Globe NewswireThe growth of artificial intelligence (AI) and the electrification of everything are driving an ever-increasing demand for higher levels of power efficiency and reliability.
ESD Alliance Reports Electronic System Design Industry Posts $5.1 Billion in Revenue in Q1 2025
07/16/2025 | SEMIElectronic System Design (ESD) industry revenue increased 12.8% to $5,098.3 million in the first quarter of 2025 from the $4,521.6 million registered in the first quarter of 2024, the ESD Alliance, a SEMI Technology Community, announced in its latest Electronic Design Market Data (EDMD) report.
Beyond Design: Refining Design Constraints
07/17/2025 | Barry Olney -- Column: Beyond DesignBefore starting any project, it is crucial to develop a thorough plan that encompasses all essential requirements. This ensures that the final product not only aligns with the design concept but is also manufacturable, reliable, and meets performance expectations. High-speed PCB design requires us to not only push technological boundaries but also consider various factors related to higher frequencies, faster transition times, and increased bandwidths during the design process.