-
- News
- Books
Featured Books
- design007 Magazine
Latest Issues
Current IssueTraining New Designers
Where will we find the next generation of PCB designers and design engineers? Once we locate them, how will we train and educate them? What will PCB designers of the future need to master to deal with tomorrow’s technology?
The Designer of the Future
Our expert contributors peer into their crystal balls and offer their thoughts on the designers and design engineers of tomorrow, and what their jobs will look like.
Advanced Packaging and Stackup Design
This month, our expert contributors discuss the impact of advanced packaging on stackup design—from SI and DFM challenges through the variety of material tradeoffs that designers must contend with in HDI and UHDI.
- Articles
- Columns
Search Console
- Links
- Media kit
||| MENU - design007 Magazine
BOOK EXCERPT: The Printed Circuit Designer’s Guide to... DFM Essentials, Chapter 2
November 14, 2024 | I-Connect007 Editorial TeamEstimated reading time: 1 minute
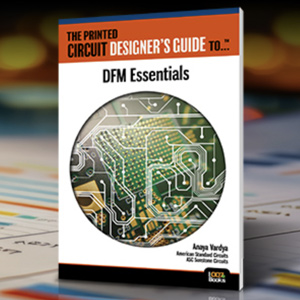
The Printed Circuit Designer’s Guide to... DFM Essentials
by Anaya Vardya, American Standard Circuits / ASC Sunstone Circuits
Chapter 2: Panelization
Panelization is the process of placing one or more PCBs on a manufacturing panel and incorporating features to assist manufacturing (such as tooling holes, fiducials, coupons, panel thieving, etc.). Panelization is one of the highest impact factors in the cost of a PCB.
The panel area available for circuit boards plus coupons is known as the usable area (Figure 2.1). Test coupons are added by the fabricator to the perimeter of the manufacturing panel outside the usable area. The number and type of coupons are based on the specs that the PCBs are being built to and requirements for controlled impedance. Coupons may sometimes further reduce the amount of a PCB panel that is available for the circuit boards. This is defined by the fabricator as required perimeter for coupons. This is typically about 1 inch or 25.4 mm and is a fixed area based on panel size. Panel utilization is measured as a percentage, defined by the total area for PCBs divided by the total panel area.
Cost-effective material utilization is defined by a target panel with greater than 75% panel utilization. Raw laminate is one of the primary cost constituents of a multilayer PCB. Optimizing panel structures around standard base materials while achieving maximum material utilization on one of the standard panel sizes can have a significant impact on multilayer board prices and deliveries. The three most preferred sizes in North America are 12x18 inches, 18x24 inches and 21x24 inches, with 18x24 inches being the most common. For special applications, other panel sizes can be provided. In Asia, typically the shops will process custom panel sizes in order to maximize utilization. The most effective cost per unit area processed is usually found with a larger panel size.
Visit the I-Connect007 library to continue reading The Printed Circuit Designer’s Guide to DFM Essentials.
Suggested Items
Global Smartphone Panel Shipments to Grow 11.4% in 2024, with Chinese Manufacturers’ Market Share Approaching 70%
02/26/2025 | TrendForceTrendForce’s latest findings reveal that global smartphone panel shipments reached 2.157 billion units in 2024, marking an 11.4% YoY increase—the highest in recent years.
Gaming Monitor Panel Growth to Slow in 2025—LCD Up 5%, OLED Up 40%
02/19/2025 | TrendForceTrendForce’s latest investigations reveal that global LCD gaming monitor panel shipments (>144 Hz) reached 32.42 million units in 2024, marking a 12% YoY increase. However, due to a lack of major demand catalysts and struggling profitability in mainstream gaming monitors, 2025 shipments are expected to grow at a slower rate of 5%, reaching approximately 34 million units.
Transparent Electronics Market to Reach $2611 Million by 2030
01/31/2025 | BUSINESS WIREThe Global Transparent Electronics Market was valued at $963 Million in 2023 and is anticipated to reach $2611 Million by 2030, witnessing a CAGR of 15.4% during the forecast period 2024-2030.
Taiwan Earthquake Shows Shows Minimal Impact on Wafer Fabs, But Tightness in the TV Panel Supply May Worsen in 1Q25
01/21/2025 | TrendForceA magnitude 6.4 earthquake struck southern Taiwan, with its epicenter in Chiayi, at 12:17 AM on January 21, 2025. TrendForce’s preliminary assessment found that nearby wafer fabs had not suffered significant damage.
Würth Elektronik at PEDC 2025
01/14/2025 | Wurth ElektronikOn January 29 to 30, 2025, the Pan-European Electronics Design Conference (PEDC) will convene leading experts from industry and research in Vienna.