-
- News
- Books
Featured Books
- design007 Magazine
Latest Issues
Current IssueShowing Some Constraint
A strong design constraint strategy carefully balances a wide range of electrical and manufacturing trade-offs. This month, we explore the key requirements, common challenges, and best practices behind building an effective constraint strategy.
All About That Route
Most designers favor manual routing, but today's interactive autorouters may be changing designers' minds by allowing users more direct control. In this issue, our expert contributors discuss a variety of manual and autorouting strategies.
Creating the Ideal Data Package
Why is it so difficult to create the ideal data package? Many of these simple errors can be alleviated by paying attention to detail—and knowing what issues to look out for. So, this month, our experts weigh in on the best practices for creating the ideal design data package for your design.
- Articles
- Columns
- Links
- Media kit
||| MENU - design007 Magazine
Preventing De-wetting Defects In Immersion Tin Soldering
January 4, 2023 | Britta Schafsteller, AtotechEstimated reading time: 7 minutes
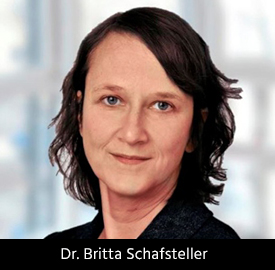
Immersion tin is well accepted as a high-reliability final finish in the industry. Due to its excellent corrosion resistance, it exhibits major market shares, particularly in the automotive industry. During the soldering process, an intermetallic compound (IMC) is formed between copper and tin. One remaining concern in the industry is the potential impact of the IMC on the solderability of the final finish.
In this article, typical failure modes in soldering immersion tin are described and correlated to potential root causes for the defects.
During aging, thermal exposure, or during the reflow process in the assembly, an intermetallic layer is formed between the copper substrate and the tin layer so that the tin deposit eventually consists of IMC and free tin covered by a Sn-Oxide layer. This layer consists of a mixture of SnO and SnO2, which is referred to as SnOx or Sn-Oxide. The assembly properties of the tin layer depend on the characteristics of IMC, Sn-Oxide layer, and free tin content, which was extensively studied and described by T. Hetschel et al. in 20091-2. Due to the growth of the IMC, which consumes most of the free tin, only islands of tin remain at the top of the layer, which are covered by a thin oxide layer. The properties of the Sn-Oxide layer, such as homogeneity and thickness, impact the solderability of the tin surface finish as well as other characteristics. Contaminations in the tin deposit or defects in the oxide layer can lead to poor wettability or discolorations, known as de-wetting defects.
IMC Growth and Tin-oxide Formation During Reflow Process
During the assembly process, the tin-plated panel must undergo multiple reflow cycles. During the reflow process, the IMC grows and the thickness of the oxide layer covering the tin deposit will increase. After the first reflow cycle, typically about 70% to 80% of the overall tin thickness is consumed by the formation of Cu6Sn5 and Cu3Sn intermetallic phase3. In the second reflow cycle, the IMC thickness further increases so that only single islands of pure tin remain at the deposit surface. At the same time, the reflow process leads to a growth of the oxide layer. While reflow aging under nitrogen has a minor impact, the reflow process under air will significantly increase the Sn-Oxide layer thickness. The interaction of IMC characteristics and Sn-Oxide layer properties will have considerable impact on the solderability of the immersion tin finish.
When looking at the assembly of immersion tin layers, the key root cause for soldering issues is contamination, which affects both the IMC growth and the oxide layer formation. Three different types of contamination can be considered:
- Contaminations on copper before the tin plating process
- Leach out of soluble organics into the tin electrolyte the plating process
- Condensation of organic volatile components onto the tin deposit during the reflow process
The soldering defects which can be observed on immersion tin finishes typically can be categorized into the following categories:
- Non-wetting: In this case, the solder does not wet the tin surface. This can occur when contaminations on top of the tin surface act as a physical barrier towards the solder.
- De-wetting: The molten solder wets the surface but then recedes. A possible reason for this can be inadequate cleaning or an inhomogeneous formation of the oxide layer.
- Self-de-wetting: the remaining free tin, which melts during the second reflow process, penetrates the Sn-Oxide layer and agglomerates on top. This defect typically occurs when the oxide layer is uneven leading to cracks during the second reflow cycle.
With regard to the de-wetting and self-de-wetting defects, the homogeneity and thickness of the Sn-Oxide layer is highly important.
In the following section, some examples will be given to explain how contaminations affect the solderability of the tin surface finish.
Residues on Copper
If residues from previous processes such as solder mask application remain on the copper surface before the panel is immersed in the tin plating solution, this can affect the solderability of the final finish. The residues cannot be removed during the wet plating process and remain at the copper/tin interface. During the first reflow cycle, such residues can migrate to the tin layer surface with the growing IMC. In the second reflow cycle, the residues can affect the stability of the tin oxide layer and lead to cracks, so that the liquid tin penetrates and reaches the layer surface. Figure 1 shows a schematic drawing that illustrates how the residues can move within the layer and reach the tin layer surface during the two reflow cycles.
Figure 1: Schematic drawing of the potential impact of contaminations on copper during reflow process.
Contamination on Tin
Also, the tin plating process itself can bear a risk for contaminations in the plated layer. This can be caused by either leach out of components of solder mask in the tin electrolyte, which are then co-deposited in the tin plating process, or residues of the tin chemistry, which are not properly rinsed after the tin plating step and remain on the tin surface. An easy method to identify organic contaminants on the tin surface is to use a fluorescence microscope. This enables the detection of fluorescent components that are not visible to the naked eye. Investigations of defect boards could clearly indicate a correlation between the areas of melting defect and UV fluorescence of the residues. Figure 2 shows an exemplary image of the contaminated areas, which are indicated by green markers.
Figure 2: Fluorescence-microscopic imaging of defect pads showing self-de-wetting.
Re-condensation of Volatiles
Finally, volatiles can be a third source for contamination, as they re-condensate on the tin layer during the reflow process. These can either evaporate from base material or improperly cured solder mask, or they can be from organic residues that accumulate over time in the reflow oven. If the solder mask is not properly cured, it exhibits a high risk to release volatiles during the reflow process. One countermeasure to reduce the evaporation of organic components is to apply a UV-bump treatment before the immersion tin plating process. A comparison test with a partially cured solder mask was conducted with varying reflow conditions. Results showed that UV treatment and oxygen atmosphere in the reflow oven lead to a significantly improved appearance of the immersion tin finish.
Figure 3 shows the appearance of the immersion tin surface after the second reflow cycle. A clear difference can be observed for the variation of the reflow atmosphere. A white and homogeneous appearance is observed for the samples treated in air atmosphere, while the samples processed under nitrogen appear yellowish. Air atmosphere leads to a stronger increase in the oxide layer thickness. This helps to ensure a homogeneous oxide layer and prevents the penetration of liquid tin through the oxide layer.
Figure 3: Tin layer appearance after the second reflow cycle with varied reflow conditions.
Beside that, the UV treatment of the panel before the tin plating process help to improve its appearance. The panels which were not UV-treated both show an uneven appearance and discoloration. The results indicate that organic contaminants evaporating from the soldermask can lead to local defect on the tin finish. The panels which were UV treated exhibit a very even and homogeneous appearance giving no indication for local defects.
Summary
The soldering defects that can appear on immersion tin finishes in the second reflow step are, in most cases, related to contamination issues. These can be either residues on copper, co-deposited contaminations in the tin deposit, or condensates or residues on top of the tin surface.
As the formation of the IMC and oxide layer during the assembly process also affects the soldering properties of the immersion tin layer, contaminations that affect the IMC growth and oxide layer formation will also impact soldering performance. To maintain a good solderability of the tin layer, all possible sources of contaminations should be reduced to a minimum by ensuring:
- Appropriate cleaning to remove residues on copper.
- Appropriate rinsing to remove chemistry residues after plating.
- Controlled solder mask process to prevent residues and copper from leaching out during the plating process, as well as re-condensation of volatiles during the assembly step.
Additionally strengthening the oxide layer can help to increase the process robustness. Post-treatment step options are available to significantly improve the appearance after reflow, as indicated by exemplary surface images.
Figure 4: Tin layer appearance after reflow with and without post-treatment.
References
- “Alterungsverhalten und Lötbarkeit der chemisch abgeschiedenen Zinn-Leiterplattenoberfläche,” dissertation by T. Hetschel at Technische Universität Dresden, 2009.
- “Wettability effects of immersion tin final finishes with lead free solder,” by T. Hetshel et al., 2nd Electronics System-Integration Technology Conference, 2008.
- “Soldering immersion tin,” by R. Nichols and S. Heinemann, IPC APEX 2017.
Britta Schafsteller is the Global Product Manager of Selective Finishing at Atotech.
Testimonial
"Our marketing partnership with I-Connect007 is already delivering. Just a day after our press release went live, we received a direct inquiry about our updated products!"
Rachael Temple - AlltematedSuggested Items
Weller Tools Supports Future Talent with Exclusive Donation to SMTA Michigan Student Soldering Competition
07/23/2025 | Weller ToolsWeller Tools, the industry leader in hand soldering solutions, is proud to announce its support of the upcoming SMTA Michigan Expo & Tech Forum by donating a limited-edition 80th Anniversary Black Soldering Set to the event’s student soldering competition.
Koh Young Appoints Tom Hattori as President of Koh Young Japan
07/21/2025 | Koh YoungKoh Young Technology, the global leader in True 3D measurement-based inspection solutions, announced the appointment of Tom Hattori as President of Koh Young Japan (JKY).
Silicon Mountain Contract Services Enhances SMT Capabilities with New HELLER Reflow Oven
07/17/2025 | Silicon Mountain Contract ServicesSilicon Mountain Contract Services, a leading provider of custom electronics manufacturing solutions, is proud to announce a significant upgrade to its SMT production capability with the addition of a HELLER 2043 MK5 10‑zone reflow oven to its Nampa facility.
Knocking Down the Bone Pile: Addressing End-of-life Component Solderability Issues, Part 4
07/16/2025 | Nash Bell -- Column: Knocking Down the Bone PileIn 1983, the Department of Defense identified that over 40% of military electronic system failures in the field were electrical, with approximately 50% attributed to poor solder connections. Investigations revealed that plated finishes, typically nickel or tin, were porous and non-intermetallic.
SHENMAO Strengthens Semiconductor Capabilities with Acquisition of PMTC
07/10/2025 | SHENMAOSHENMAO America, Inc. has announced the acquisition of Profound Material Technology Co., Ltd. (PMTC), a premier Taiwan-based manufacturer of high-performance solder balls for semiconductor packaging.