-
- News
- Books
Featured Books
- design007 Magazine
Latest Issues
Current IssueProper Floor Planning
Floor planning decisions can make or break performance, manufacturability, and timelines. This month’s contributors weigh in with their best practices for proper floor planning and specific strategies to get it right.
Showing Some Constraint
A strong design constraint strategy carefully balances a wide range of electrical and manufacturing trade-offs. This month, we explore the key requirements, common challenges, and best practices behind building an effective constraint strategy.
All About That Route
Most designers favor manual routing, but today's interactive autorouters may be changing designers' minds by allowing users more direct control. In this issue, our expert contributors discuss a variety of manual and autorouting strategies.
- Articles
- Columns
- Links
- Media kit
||| MENU - design007 Magazine
Estimated reading time: 1 minute
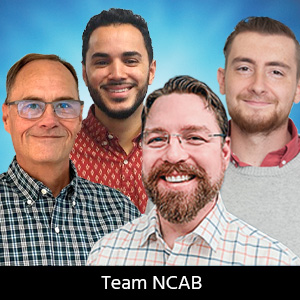
Fresh PCB Concepts: Recommendations for Track Welding and Open Circuit Repair
Track welding is what some factories may opt for if they find an open circuit. The technique is to attach/stick/weld a thin piece of copper across the broken track. Sounds okay, right? But how reliable is the repair? And how does IPC cover this subject?
Well, IPC doesn’t have too much to add on this subject other than mentioning that the customer and supplier should agree whether repairs are acceptable or not. Therefore, if the customer does not advise it is not acceptable, then it is acceptable by default. In my experience, the issue is rarely discussed between the supplier and customer. The lack of front-end discussions all too often comes to light after the fact when anomalies are detected on the finished PCB assembly.
Poor repairs can lead to open circuits being supplied; even a “good” repair has a risk of failure under load conditions (vibrations, etc.) leading to potential field failures.
To repair a PCB, the operator must remove the solder mask properly to expose the copper. Plus, the solder mask must be removed in the correct area without exposing the adjacent track and this can lead to a risk of short circuits. Then, copper must be welded very accurately to a thin track and ensure good enough registration. Finally, there must be enough contact to the original track. Even if the repair is reliable, many times the track is reduced by more than the acceptable IPC allowance for reduction limits.
We recommend having in place a strict policy when it comes to track welding: Do not allow repair of open circuits or track welding. Period. Any supplier utilized should also have track welding terms in their specifications. There’s too much risk. If you’ve ever experienced a field failure and all the effort, time, and costs that occur, you would know it’s worth it.
It’s a nightmare no one wants to go through. In this case, the best part if it’s not cost driven in the same way other things are such as via plugging or very thick copper.
Michael “Mike” Marshall is a field application engineer at NCAB Group.
More Columns from Fresh PCB Concepts
Fresh PCB Concepts: More Than Compliance—A Human-centered Sustainability ApproachFresh PCB Concepts: Assembly Challenges with Micro Components and Standard Solder Mask Practices
Fresh PCB Concepts: The Power of a Lunch & Learn for PCB Professionals
Fresh PCB Concepts: Key Considerations for Reliability, Performance, and Compliance in PCBs
Fresh PCB Concepts: Traceability in PCB Design
Fresh PCB Concepts: Tariffs and the Importance of a Diverse Supply Chain
Fresh PCB Concepts: PCB Stackup Strategies—Minimizing Crosstalk and EMI for Signal Integrity
Fresh PCB Concepts: PCB Plating Process Overview