-
- News
- Books
Featured Books
- design007 Magazine
Latest Issues
Current IssueProper Floor Planning
Floor planning decisions can make or break performance, manufacturability, and timelines. This month’s contributors weigh in with their best practices for proper floor planning and specific strategies to get it right.
Showing Some Constraint
A strong design constraint strategy carefully balances a wide range of electrical and manufacturing trade-offs. This month, we explore the key requirements, common challenges, and best practices behind building an effective constraint strategy.
All About That Route
Most designers favor manual routing, but today's interactive autorouters may be changing designers' minds by allowing users more direct control. In this issue, our expert contributors discuss a variety of manual and autorouting strategies.
- Articles
- Columns
- Links
- Media kit
||| MENU - design007 Magazine
Estimated reading time: 3 minutes
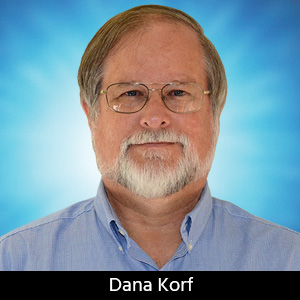
Dana on Data: Understanding Mechanical Drill Size Capability and Cost
“Information is not knowledge.” — Albert Einstein
Fabricator capabilities are generally provided initially on a one-page summary as part of the general marketing presentation. The technical values that are presented provide the “check mark” information so the potential customer can determine if the fabricators capability is greater than the design requirements. Often, this is the only method used for design rule knowledge transfer.
Design documentation provides finished hole sizes (FHS) versus drilled hole sizes (DHS) for plated through- or blind/buried holes. The FHS will typically be 0.05 – 0.127 mm less than the DHS. DHSs are provided for non-plated guide pin or tooling holes and some press-fit connector styles.
Mechanical drill hole specifications are often provided by the fabricator as a single variable value in the capability matrix. They may provide both standard capability and advanced capability guidance for a higher cost option. Table 1 shows a typical capability table that is provided in the initial marketing presentation.
Table 1: A list of typical capabilities.
The minimum drill diameter is used by the designer to select the via finished hole size and via pad size, based on the IPC class that is used. The maximum drill diameter provides the limit for tooling or guide hole sizes. The aspect ratio is derived from the PCB overall thickness divided by the drill diameter. Abiding by the aspect ratio specification is critical to ensure that the hole can be copper plated thick enough to meet the minimum IPC or application requirement.
A common mistake is when the designer uses the minimum drill diameter with the maximum aspect ratio because the table implies that they can be used together. In reality, the maximum aspect ratio varies with the drill diameter. Table 2 shows how the aspect ratio decreases as the drilled hole size decreases.
Table 2: The relationship between aspect ratio and drilled hole size.
The maximum aspect ratio per drill hole size will vary between fabricators based on their specific capabilities. The designer should ask for this table prior to determining the routing strategy. Some fabricators will provide the following design rules to present the aspect ratio to drilled hole diameter relationship (Table 3).
Table 3: Typical aspect ratio design guidelines.
There are other factors that will impact the maximum aspect ratio. Common items are:
- The total copper thickness for all layers in the hole may limit the minimum drilled hole size and or significantly affect the PCB cost. Removing non-functional pads for vias significantly affect the drilled hole cost.
- Drill bit diameters are generally metric and standardized through the world. Custom drills can be tooled at a higher cost. FHS’s that are close to each other, e.g., 0.025 mm different, may be combined into a single drill diameter to save cost. Drilled hole sizes that are non-metric, e.g., 10 mils, will generally be converted to a metric size, 9.8 mils, in this example.
- Buried vias are generally used on a double-sided core or on a thinner sub-laminated PCB. This via will generally have a low aspect ratio.
- Via filled holes in which the plated diameter is the critical dimension. There is a limitation on the maximum plated diameter where the epoxy will remain in the hole and not slump out of the other end. If it is too large, the mask will leak out the bottom of the hole. Conversely, it will not fill the hole when the aspect ratio and diameter are too small.
- Via plugged holes have the same limitation as via filled holes. The via plug is not intended to completely fill the hole. It is intended to cover the top surface. A maximum FHS should be provided. The via plug will sag and not properly coat the hole if the diameter is too large.
- The glass weave style may have limitations for small drill diameters.
- Surface finishes may have drilled hole aspect ratio limitations to ensure that the plated hole is large enough to allow for proper coating and cleaning. This is common for immersion and OSP surface finishes.
Similar limitations are also applicable to punched holes used in thin FPC or rigid PCBs. The aspect ratio limitation is not restricted by the copper plating process but from the die used to punch the holes.
The designer should ask for the drill diameter to aspect ratio limitations prior to starting the layout to ensure that the design is not outside of that fabricators capability or pushing it into their higher cost advanced capability. Most design and DFM software do not currently have the ability to load aspect ratio versus drilled or finished hole size rules, so the rules must be manually checked.
Dana Korf is the principal consultant at Korf Consultancy LLC.
More Columns from Dana on Data
Dana on Data: Best Practices in Interpreting Drawing Notes—‘Use Latest Revision’Dana on Data: The Missing AI-NPI Link
Dana on Data: Merging 2D Electrical, 3D Mechanical Worlds
Dana on Data: Resurrecting IPC Class 1
Dana on Data: The Evolution of Fabrication Drawing
Dana on Data: The Insane PCB DFM Process
Dana on Data: eCAD PCB Design Deficiencies
Dana on Data: Nuke the Netlist