-
- News
- Books
Featured Books
- design007 Magazine
Latest Issues
Current IssueProper Floor Planning
Floor planning decisions can make or break performance, manufacturability, and timelines. This month’s contributors weigh in with their best practices for proper floor planning and specific strategies to get it right.
Showing Some Constraint
A strong design constraint strategy carefully balances a wide range of electrical and manufacturing trade-offs. This month, we explore the key requirements, common challenges, and best practices behind building an effective constraint strategy.
All About That Route
Most designers favor manual routing, but today's interactive autorouters may be changing designers' minds by allowing users more direct control. In this issue, our expert contributors discuss a variety of manual and autorouting strategies.
- Articles
- Columns
- Links
- Media kit
||| MENU - design007 Magazine
Estimated reading time: 4 minutes
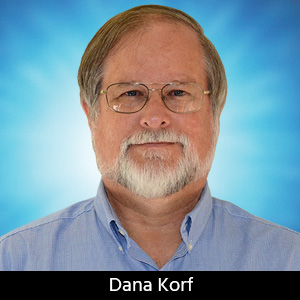
Dana on Data: Factory 4.0 NPI Compatible Industry Specification Format
IPC APEX EXPO’s emphasis on the Connected Factory Initiative based on CFX and IPC-2581 is underway in a virtual mode this month. The industry is moving down the path of connecting, via bi-directional automation, the data that is input and created during the fabrication and assembly process. This will significantly reduce cycle times and improve quality once it can be automatically analyzed.
One area that has not been addressed is the automation of industry technical specifications from organizations like IPC, ASTM, UL, IEC, etc.
Industry specifications are typically released as a PDF file that is manually reviewed by a front-end engineer. They interpret the requirements, create/update their software, then release this into their engineering system for DFM reviews and for incorporating the requirements into the production traveler or batch card. Companies with properly sized automation programmers will load these into the automation.
Most companies do not have sufficient programming resources. So, the requirements are added into a spreadsheet along with plant design rules and customer specification requirements. This method tends to have higher defect rates because they rely on a human to remember to check and implement the requirements. The manual intervention could be eliminated by providing the technical information in an XML format that is compatible with the intelligent IPC-2581 data format.
Figure 1: Technical specifications have two primary content groupings: guidelines/tutorials, used as a reference; and design/manufacturing requirements.
Specification Functional Content
How much of an industry specification is required to be automated? Technical specifications have two primary content groupings: guidelines/tutorials, used as a reference, and design/manufacturing requirements (Figure 1).
Guidelines and Tutorials
Process Control: Recommended, or sometimes required, equipment settings, process line flow and settings are provided to ensure the stated requirements are achieved. This information is obtained from current manufacturing companies, equipment manufacturers or material suppliers. These requirements are generally incorporated into work instructions vs. product specific travelers.
Tutorials: The information provides background knowledge supporting the reasoning behind the requirements or suggestions on how to apply the requirements. This information can be as short as one line or multiple paragraphs. Tutorials can be incorporated into a company’s training program.
Qualification criteria: These requirements are provided for qualifying the product and manufacturing/inspection process prior to being released for production. These requirements are only applicable for the qualification build and must be tested and certified prior to the product transitioning volume production. This information is not generally automated because it is not used that often and it is easier to manually add it to the travelers.
Design guidelines: This information is intended to be used by the PCB designer to ensure the design complies with the stated requirement. These are generally not “shall” requirements, meaning that they are not required be met, but “should” information in that it may make the design more manufacturable, reliable, or cost effective.
Documentation guidelines: This provides suggested methods on how and where to document the requirements. This typically may indicate which design drawings or in process data collection methods should be used to indicate the requirement or collect data for process control feedback.
Design and Manufacturing Requirements
Acceptability requirements: Information is provided for in-process or final inspection. This is typically provided by text, charts, and graphics. These may be included in the traveler when the requirements are not used on every PCB design. Many of these can be added into the IPC-2581 attributes. These requirements will be included in procedures or work instruction if they are generic in nature.
Inspection methods: Compliance to a specification requirement is often tied to a specified inspection method when different test methods can yield differing results. A good example of this is magnification settings. A lower magnification may not indicate a defect that higher magnification will. This will be added to a traveler as a note in the specific operations where the inspection is performed.
Production tolerances: This is a common specification requirement. These may be physical, such as the board outline length; or electrical, such as impedance tolerances. This information is generally manually added as a fabrication drawing note, referencing the applicable industry standard. Tolerances are already included in the IPC-2581 data definition.
Material Specifications: Material specifications have a table listing of the key technical requirements. These are used by PCB designers, fabricator front-end engineers and incoming material inspectors. This data could easily be converted to an XML format so automated acceptance and design tool loading can occur. For example, many impedance modeler software packages have tables for materials and industry specifications that are manually loaded.
A couple of new companies have combined their resources and knowledge to work with the industry specification companies to create XML based summaries. They will be testing industry acceptance soon. The move to a fully automated bi-directional process will significantly improve design reliability, stability, and cost by reducing the manufacturing variation and risk. The industry is moving in the right direction and we can now focus on automating secondary information transfer that is critical to a successful new product introduction.
Dana Korf is the principal consultant at Korf Consultancy LLC.
More Columns from Dana on Data
Dana on Data: Best Practices in Interpreting Drawing Notes—‘Use Latest Revision’Dana on Data: The Missing AI-NPI Link
Dana on Data: Merging 2D Electrical, 3D Mechanical Worlds
Dana on Data: Resurrecting IPC Class 1
Dana on Data: The Evolution of Fabrication Drawing
Dana on Data: The Insane PCB DFM Process
Dana on Data: eCAD PCB Design Deficiencies
Dana on Data: Nuke the Netlist