-
- News
- Books
Featured Books
- design007 Magazine
Latest Issues
Current IssueProper Floor Planning
Floor planning decisions can make or break performance, manufacturability, and timelines. This month’s contributors weigh in with their best practices for proper floor planning and specific strategies to get it right.
Showing Some Constraint
A strong design constraint strategy carefully balances a wide range of electrical and manufacturing trade-offs. This month, we explore the key requirements, common challenges, and best practices behind building an effective constraint strategy.
All About That Route
Most designers favor manual routing, but today's interactive autorouters may be changing designers' minds by allowing users more direct control. In this issue, our expert contributors discuss a variety of manual and autorouting strategies.
- Articles
- Columns
- Links
- Media kit
||| MENU - design007 Magazine
Estimated reading time: 4 minutes
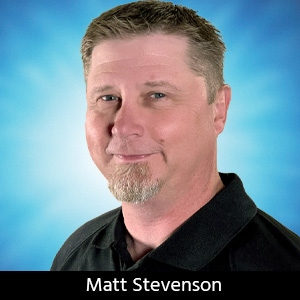
Connect the Dots: Reassessing the Risk of Offshore PCB Manufacturing
Offshore board production has long been considered an effective way to reduce the cost of producing electronic devices here at home, but those savings often demand a higher tolerance for delivery issues and come with lowered expectations for quality. In addition, the risks associated with global supply chain logistics have increased in the wake of COVID-19, and the component costs of offshoring already were increasing due to rising wages abroad, persistent high overseas transportation costs, and uncertainty surrounding global trade policies.
These macro-factors are not unique to our industry. Their impacts can vary as market conditions evolve. Problems with quality assurance (QA) are a more persistent issue when it comes to PCBs, accelerating the reshoring trend. When quality issues occur, they are usually accompanied by an absence of transparency. Collaboration with offshore manufacturers is inherently limited by time zones, distance, and, sometimes, language. These impersonal relationships foster a “take what you get” transactional paradigm that device manufacturers should not and cannot tolerate.
Offshoring Production Can Onboard Problems
Along with the highly visible risks, there are some less apparent complications that will tangle up a manufacturer. If you plan to offshore PCB manufacturing, carefully examine the impact on your domestic operations in several key areas. Offshore manufacturing does not automatically equal savings and can disrupt cash flow. If you need the boards fast, expedited shipping might end up offsetting much of your potential cost savings. Most Chinese manufacturers require full payment for prototypes or small-volume orders before they begin production. If offshore PCBs fail to meet design specifications and you’ve already paid for them, you have limited leverage with the supplier—meaning the resources required to re-tool the boards yourself or adapt the product to accommodate them further masks the real cost of low yield.
Increased Risk Can Unleash Additional Costs
Risk mitigation isn’t free, and the resource burden required to manage it falls on your domestic production team. This creates additional hidden costs that can quickly add up to offshore manufacturing actually being more expensive than domestic.
An overseas manufacturer in a time zone 10–14 hours different from yours builds your board while you sleep. Unfortunately, if you need to speak directly with someone on the offshore team, one of you will be getting up in the middle of the night to do so. Disruptions to routines like this can lead to miscommunications, misunderstandings, and expensive mistakes (Figure 1).
Your IP Won’t Protect Itself While It’s Away
The threats to your IP are complex, vary from country to country, and require a substantial financial commitment to combat. Laws surrounding domestic patents, trade secrets, and mask work are antiquated and provide minimal protection. Little or no motivation exists in places like China to protect U.S. corporate IP. Their laws, aimed at protecting foreign IP, are mostly toothless and carry limited enforcement effort with them.
Your Production Volume May Not Justify the Journey
Volume is one critical factor in determining whether to use a domestic or offshore manufacturer. Offshoring favors simple or established PCB designs that require high-volume runs with long lead times. The larger, potential aggregate savings better insulate your bottom line against less apparent offshore manufacturing costs.
The return on offshore manufacturing investment diminishes quickly when dealing with a lower volume or prototyping production. This QA risk alone should give pause to lower volume producers. A domestic resource offers more transparency to the manufacturing process, and collaboration happens faster and with less effort. Issues resolve quickly, which minimizes risk to yield and PCB quality.
Excellence Is Not Relative
During the transition from design to manufacturing, you need effective communication and coordinated effort to succeed. Transition plans, phase-ins and phase-outs, and revision control demand immediate attention that is sometimes unavailable because of time zone differences. Respected PCB fabricators in the U.S. build their businesses by excelling in these areas, while offshore vendors simply aren’t structured to provide the responsive support often required in such situations.
For an overseas provider, it is hard for your small-run project to be a priority. Even if you have an established PCB design to manufacturing flow, larger production runs will take precedence over smaller ones. Unless you are prepared to overstock to accommodate your offshore vendor, this widely accepted practice impacts scheduling and can ripple through your supply chain—adding up to significant delays in getting the finished product out the door.
Domestic manufacturers are structured for better flexibility, can provide real-time support, and are more likely to better meet the needs of low-volume production. They are also more likely to adopt green manufacturing practices and provide a safe working environment for their employees—qualities increasingly important to members of our industry. And if you operate on a JIT basis, fabricators located in your hemisphere pose less of a scheduling risk.
Did You Get What You Paid For?
Once your boards arrive from the offshore fabricator, yields become your next concern. Again, we encourage multi-dimensional analysis of the production. Instead of targeting a percentage yield and checking a box, consider the consistency of yields over time, along with the boards’ functional reliability in the end product.
Long-term reliability is a key measure. Counterfeit components routinely find their way into PCBs manufactured offshore (Figure 2). Some substandard parts are easy to spot, but not so much with others. Counterfeit components in your offshore PCB may stand up to initial testing, and then fail after your product is in use. This can impact product performance, reduce customer satisfaction, and, eventually, tarnish your reputation in the marketplace.
Conclusion
Making the right decision about domestic versus offshore PCB manufacturing depends on a thorough cost-benefit analysis. Your results will vary depending on volume and design requirements. We encourage our customers to look for the hidden costs in offshoring and seriously consider its less quantifiable pain points.
This column originally appeared in the July 2020 issue of Design007 Magazine.
More Columns from Connect the Dots
Connect the Dots: Sequential Lamination in HDI PCB ManufacturingConnect the Dots: The Future of PCB Design and Manufacturing
Connect the Dots: Proactive Controlled Impedance
Connect the Dots: Involving Manufacturers Earlier Prevents Downstream Issues
Connect the Dots: Stop Killing Your Yield—The Hidden Cost of Design Oversights
Connect the Dots: Designing for Reality—Routing, Final Fab, and QC
Connect the Dots: Designing for Reality—Surface Finish
Connect the Dots: Designing for Reality—Solder Mask and Legend