-
- News
- Books
Featured Books
- design007 Magazine
Latest Issues
Current IssueProper Floor Planning
Floor planning decisions can make or break performance, manufacturability, and timelines. This month’s contributors weigh in with their best practices for proper floor planning and specific strategies to get it right.
Showing Some Constraint
A strong design constraint strategy carefully balances a wide range of electrical and manufacturing trade-offs. This month, we explore the key requirements, common challenges, and best practices behind building an effective constraint strategy.
All About That Route
Most designers favor manual routing, but today's interactive autorouters may be changing designers' minds by allowing users more direct control. In this issue, our expert contributors discuss a variety of manual and autorouting strategies.
- Articles
- Columns
- Links
- Media kit
||| MENU - design007 Magazine
Estimated reading time: 4 minutes
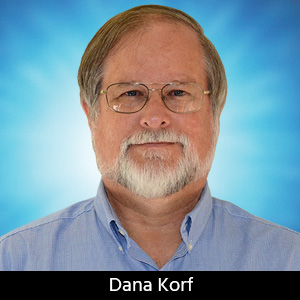
Dana on Data: How Can the PCB Industry Improve From COVID-19 Responses?
The PCB industry reacted very favorably to the global COVID-19 pandemic. Employee protection was a priority. Essential businesses reacted and continue the production of both PCBs and required medical supplies and equipment. Businesses were brought back online quickly in a very safe manner.
I watched the world transform a very slow medical approval process into the equivalent of a concurrent NPI process by removing many regulatory requirements and enhanced both government and private partnerships to reduce the cycle time from years to months (hopefully). This was achieved by challenging some of the golden rules.
I think that it is a good idea for us to re-evaluate the PCB industry to see where we can improve. Here are a few thoughts on four areas where we can do so. After 40+ years, I do not work for any company except for my home-based consulting firm. I am not a member of any political party, so my suggestions are from a personal standpoint. This industry is my passion, and I have dedicated my remaining years to help fix the poor design-to-manufacturing data transfer issues.
1. Why do we need so many quality systems to which PCB plants must audit and qualify?
We have ISO9001, TS16949, IECQ QC080000, ISO 14001, AS9100, etc., along with many OEM and EMS specific quality systems. They all have the same core requirements, and they just vary on documentation requirements and how process change notifications and qualification occur. These all cost money to support, and most plants will pick the toughest one to design their quality system around.
Why can’t all these organizations get together and create one standard with different qualification classes, much like IPC specifications do? After all, all these standards allow bad and/or un-manufacturable data to be sent by customers to be built. How can designers pass ISO9001 requirements when their PCB design documentation is bad or un-manufacturable? The manufacturing plants cannot pass if 90+% of their shipped product was bad.
Proposal: Merge all these quality standards and create approval levels.
2. Why does UL require every PCB fabricator to qualify every material combination when the materials are approved independently?
Don’t they trust the material supplier qualifications? Every fabricator has pages of material combinations that are approved. UL should be able to trust that each fabricator knows how to build a board with these materials because they all have 4+ quality system approvals from other organizations. This requirement costs the industry millions of dollars each year with no clear benefit.
Proposal: UL should remove PCB fabricator material and process approvals that have UL approval for fabricators with one or more quality system certifications.
3. Improve IPC standards.
I have worked on IPC standards for decades, and they have been extremely helpful to the industry. But it has become a large organization, and I propose to use this time to fundamentally improve in the following areas:
a. Standards used to be free to members. It costs a lot of money to join IPC. The standards are all web-based and can easily be downloaded from the IPC store. There should be much less cost incurred by IPC than when paper copies had to be mailed to everyone. Now, they are locked so that members cannot even print them for those who want to mark them up with a writing instrument.
Proposal: Let all standards be free to members to put onto their networks.
b. There are too many standards.
Proposal: They should try to merge these into 50% fewer standards and obsolete old ones that aren’t in use.
c. Get rid of Class 1. Nobody uses it.
Proposal: Eliminate Class 1 from all procedures.
d. Get rid of AABUS. It is not a specification; it is guidance.
Proposal: Move AABUS to design guides.
e. Let retired or semi-retired folks have free access to IPC documents if they are working on that document. It is called in-kind work. Buying IPC specifications are expensive to a retired person, who is paying $800 to give the industry their knowledge. I think that we all would gain so much more knowledge.
Proposal: Rebate member fees for retired folks to gain more knowledge from them globally.
4. Reduce data transfer complexity and improve the transfer quality.
Let’s standardize on the IPC-2581 format for fabrication and assembly and get rid of the older non-intelligent or less-intelligent formats. Let’s quit saying, “Please send the “Gerber files,” and change it to, “Send the 2581 file.” The use of non-intelligent data is a root cause of data transfer issues because of the conflict between different provided documents (e.g., Gerber file and netlist, Gerber file and fabrication print, fabrication print, and specifications).
Proposal: Everyone switch to IPC-2581 to improve data transfer quality.
Conclusion
Let’s use this opportunity to radically challenge some of our industry golden rules to reduce operating costs and increase knowledge transfer to future generations. As Oren Harari is quoted as saying, “The electric light did not come from the continuous improvement of candles.”
Dana Korf is the principal consultant at Korf Consultancy LLC.
More Columns from Dana on Data
Dana on Data: Best Practices in Interpreting Drawing Notes—‘Use Latest Revision’Dana on Data: The Missing AI-NPI Link
Dana on Data: Merging 2D Electrical, 3D Mechanical Worlds
Dana on Data: Resurrecting IPC Class 1
Dana on Data: The Evolution of Fabrication Drawing
Dana on Data: The Insane PCB DFM Process
Dana on Data: eCAD PCB Design Deficiencies
Dana on Data: Nuke the Netlist