-
- News
- Books
Featured Books
- design007 Magazine
Latest Issues
Current IssueProper Floor Planning
Floor planning decisions can make or break performance, manufacturability, and timelines. This month’s contributors weigh in with their best practices for proper floor planning and specific strategies to get it right.
Showing Some Constraint
A strong design constraint strategy carefully balances a wide range of electrical and manufacturing trade-offs. This month, we explore the key requirements, common challenges, and best practices behind building an effective constraint strategy.
All About That Route
Most designers favor manual routing, but today's interactive autorouters may be changing designers' minds by allowing users more direct control. In this issue, our expert contributors discuss a variety of manual and autorouting strategies.
- Articles
- Columns
- Links
- Media kit
||| MENU - design007 Magazine
Estimated reading time: 3 minutes
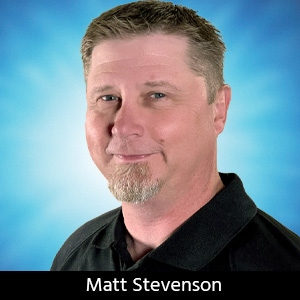
Connect the Dots: New Landing Design to Reduce Thermal Pad Failure
You’ve finally finished your design. All the traces are correct and the integrated circuit (IC) landings are to the manufacturer’s specifications. A short run of test boards performs perfectly. For best results, you select a reputable domestic board house for production and a quality assembly shop to do the soldering. When the finished boards arrive, everything looks great. You’re in high spirits and congratulate yourself on a job well done.
Then the reports start coming in:
- “My board worked for a week but won’t boot up now. I need a replacement.”
- “We’re seeing a high percentage of failures during quality assurance.”
- “My order is dead on arrival. Did you test it before you sent it?”
You’ve done everything by the book and passed every preliminary test but things are still going wrong. What’s happening here?
I found myself in a similar situation while working on a client project. The failure rates were only a small percentage, but in volume, those costs quickly run into thousands of dollars. We poured over every possibility and traced the problem down to a single high-power quad flat package IC where the center thermal pad was not being soldered consistently. Nothing was wrong with the board or the soldering process; the default method for soldering heat slugs to boards was just inherently flawed. Looking at the costs and reliability problems, we knew we had to do better.
After testing a variety of different designs, we found one that was vastly more reliable and did not add to the cost of manufacturing. The solution translates well to similar IC packages. We were back up and running again, but what was the problem in the first place?
Problem: Uncontrollable, Unpredictable Solder
At first, we used the standard, manufacturer-recommended method for heat sinking. We placed large copper pads on both sides of the board under the chip, connected them with vias to conduct heat, and applied full solder paste coverage for the best thermal contact. As straightforward and intuitive as the standard approach is, it obviously has some problems.
In this case, the culprit is solder’s unpredictable behavior once melted, which puts every board at risk of a poor heat sink connection. We’ve all seen the result of bad solder connections: Failures in quality assurance or worse—shortened life and failure in the field. The problem is so pervasive you might be tempted to accept it as the unavoidable cost of doing business. But if we look at the causes of the chaos, we can find ways to offset them. There are two main mechanisms that cause these failures: Solder wicking through vias and solder movement under large pads.
Figure 1 shows (a) a top layer—solder mask and paste mask opening; (b) a plated through-hole with no solder mask opening placed very close to, but not tangent with, the solder mask opening; and (c) a copper pad, top layer. Note that the solder mask opening should be greater than or equal to one-half of the thermal area of component body for efficient transfer of heat. Further, all plated through-holes should be vias tied to the same net as copper pour. Vias should not have thermal relief on any layer or have a solder mask opening on the top or bottom layer. Figure 2 shows a different view.
Figure 2: A side view of the board in Figure 1 illustrating placement of joints, mask openings, and vias.
Implementation
The most efficient way to implement this design is to make it part of your package definition so it is uniformly applied to all similar parts. Unfortunately, many CAD packages do not support the direct addition of vias and copper planes to package designs. An easy workaround is to create square surface mount device (SMD) pads to act as the top and bottom copper sinks, as well as small plated through-hole pads to act as the vias. These can then be set as unconnected pins in your component definition. You may have to create custom paste and solder masks for these pins, but this is usually not too difficult.
Try this design out for your next project and you will be happy with the results. The benefits of this design speaks for itself: Fewer failures and phone calls, a more consistent product, and (of course) a fatter bottom line.
This column originally appeared in the October issue of DESIGN007 Magazine.
More Columns from Connect the Dots
Connect the Dots: Sequential Lamination in HDI PCB ManufacturingConnect the Dots: The Future of PCB Design and Manufacturing
Connect the Dots: Proactive Controlled Impedance
Connect the Dots: Involving Manufacturers Earlier Prevents Downstream Issues
Connect the Dots: Stop Killing Your Yield—The Hidden Cost of Design Oversights
Connect the Dots: Designing for Reality—Routing, Final Fab, and QC
Connect the Dots: Designing for Reality—Surface Finish
Connect the Dots: Designing for Reality—Solder Mask and Legend