-
- News
- Books
Featured Books
- pcb007 Magazine
Latest Issues
Current IssueInventing the Future with SEL
Two years after launching its state-of-the-art PCB facility, SEL shares lessons in vision, execution, and innovation, plus insights from industry icons and technology leaders shaping the future of PCB fabrication.
Sales: From Pitch to PO
From the first cold call to finally receiving that first purchase order, the July PCB007 Magazine breaks down some critical parts of the sales stack. To up your sales game, read on!
The Hole Truth: Via Integrity in an HDI World
From the drilled hole to registration across multiple sequential lamination cycles, to the quality of your copper plating, via reliability in an HDI world is becoming an ever-greater challenge. This month we look at “The Hole Truth,” from creating the “perfect” via to how you can assure via quality and reliability, the first time, every time.
- Articles
- Columns
- Links
- Media kit
||| MENU - pcb007 Magazine
Estimated reading time: 4 minutes
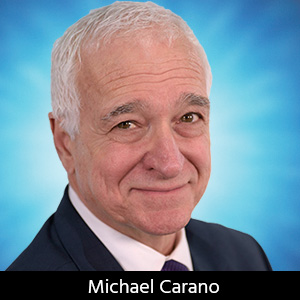
Contact Columnist Form
Trouble in Your Tank: Building Reliability into the PCB, Part 2
In Part 1 of this column on reliability, I presented the common PTH failures encountered when reliability is less than robust. PTH reliability is influenced by several factors including the quality of the PTH after drilling, plating thickness and plating distribution in the PTH. In this column, I will present additional factors, including the Coffin-Manson model in the context of understanding reliability failures.
Explaining the Failures
Many engineers have been in this situation: Process audits are completed. Personnel who have direct influence are properly trained. Analytical controls are in place. Great! Yet there are boards that are not meeting specification (IPC 6010 Series, IPC 600, IPC 610). And now the team has to deal with the rejects and provide corrective actions.
In the case of the PTH failures presented previously, reliability experts have long sought to frame and predict these failures with different models. One popular model is the Coffin-Manson model. This model functions on the premise that cycles to failure in a PTH is predicated on the resistance of the plated copper to fatigue and the overall strain imposed on the copper during the thermal cycles[1]. For ductile materials such as copper, the majority of the strain is plastic strain. While the thermal expansion of individual materials is reversible, the majority of the plastic strain that is found in the copper PTH barrel is not reversible.
The PTH acts like a rivet, which resists this expansion, but the copper barrel is stressed and may crack, causing electrical failure. There is increasing strain on the barrel associated with a high-temperature excursion. Failure may occur in a single cycle or may take place by initiation and growth of a fatigue crack over the course of a number of cycles. For high-aspect ratio through-holes subject to repeated thermal shocks from room temperature to solder reflow temperatures (220–250°C) during board fabrication (e.g., hot-air solder leveling) and assembly (reflow, wave soldering, rework), it is not uanheard of to encounter failures after 10 or fewer of these thermal cycles. While the Coffin-Manson model works fairly well in explaining failures, it does not take into account several other issues that may affect PTH reliability. These are:
- Poor copper plating distribution in PTH
- Poor leveling leading to thin areas of copper plating (Figure 1)
Figure 1: Inadequate leveling leading to thin plating in the PTH (Source: IPC, Bannockburn, Illinois).
- Glass fibers protruding from poor drilling (Figure 2)
- Resin interactions with glass weave
- Changes in copper grain structure from lot to lot
- Rough plated copper
- Copper ductility variations from lot to lot, board to board
Figure 2: Rough and/or poorly drilled PTH. Glass fiber protrusions are evident.
The majority of the issues listed above can be controlled while others depend on other factors such as circuit board design, resin material properties and copper foil thickness, to mention a few. Process design, robust chemical processes and equipment will also influence the reliability of the PTH through various interactions.
Protruding glass fibers (Figure 2) affect PTH reliability in several ways. As an example, poor drilling practices cause the glass fiber bundles to be ripped out from the hole wall. These fibers then can act as a high spot leading to poor plating distribution within the hole wall. These areas are stress points that can lead to PTH failure during thermal loading.
Additionally, a critical concern with respect to PTH reliability is the wedge void. Obviously, there are a number of possibilities leading to this type of defect. First, one should note (although it is not exclusive) that the wedge originates at the B-stage side. The mechanism of the “wedge void” formation discussed below will illustrate the significance of the defect and the genesis of a plating void.
Figure 3: Wedge void (Photo courtesy of Dr. Karl Dietz, formerly with DuPont).
One often overlooked cause of wedge voids is the drilling operation. During the drilling operation, vibration of the drill bit can create microfractures in the copper/dielectric interface. Of course, dull drill bits, excessive chip loads, extremely high heat generation during drilling and poor quality entry and back-up material will increase the likelihood of a wedge void. Figure 3 shows an extreme example of a wedge void caused mainly by poor drilling practice. (Note evidence of gouging in the hole wall and turn-out glass bundles.) This type of drilling will generate significant heat leading to the opening of the interface between the B-stage and the copper. Copper plating subsequently is unable to “level” out the wedge leading to copper plating folds. These folds typically are very thin in the plated copper and thus more susceptible to cracking from thermal stress. Keep in mind, thickness of the plated copper in the PTH does matter (Figure 4).
Figure 4: Effect of PTH plating thickness on number of thermal cycles to failure for thermal cycles with the indicated peak temperatures. For acid-sulfate copper and FR-4 170 Tg boards. (Source: Printed Circuits Handbook, Clyde Coombs, 2006.)
Summary
The integrated nature of printed circuit fabrication requires that engineers recognize the influence of up and down stream processes.
Information presented in this month’s column underscores the fact. When poor drilling or lack of control of plating processes causes low copper plating thickness, long-term reliability is compromised.
Editor's Note: This article originally appeared in the August 2016 issue of The PCB Magazine.
More Columns from Trouble in Your Tank
Trouble in Your Tank: Metallizing Flexible Circuit Materials—Mitigating Deposit StressTrouble in Your Tank: Can You Drill the Perfect Hole?
Trouble in Your Tank: Yield Improvement and Reliability
Trouble in Your Tank: Causes of Plating Voids, Pre-electroless Copper
Trouble in Your Tank: Organic Addition Agents in Electrolytic Copper Plating
Trouble in Your Tank: Interconnect Defect—The Three Degrees of Separation
Trouble in Your Tank: Things You Can Do for Better Wet Process Control
Trouble in Your Tank: Processes to Support IC Substrates and Advanced Packaging, Part 5