-
- News
- Books
Featured Books
- pcb007 Magazine
Latest Issues
Current IssueInventing the Future with SEL
Two years after launching its state-of-the-art PCB facility, SEL shares lessons in vision, execution, and innovation, plus insights from industry icons and technology leaders shaping the future of PCB fabrication.
Sales: From Pitch to PO
From the first cold call to finally receiving that first purchase order, the July PCB007 Magazine breaks down some critical parts of the sales stack. To up your sales game, read on!
The Hole Truth: Via Integrity in an HDI World
From the drilled hole to registration across multiple sequential lamination cycles, to the quality of your copper plating, via reliability in an HDI world is becoming an ever-greater challenge. This month we look at “The Hole Truth,” from creating the “perfect” via to how you can assure via quality and reliability, the first time, every time.
- Articles
- Columns
- Links
- Media kit
||| MENU - pcb007 Magazine
Estimated reading time: 5 minutes
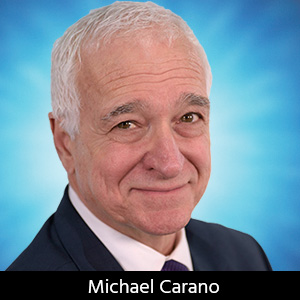
Contact Columnist Form
Trouble in Your Tank: Causes of Plating Voids, Pre-electroless Copper
In the business of printed circuit fabrication, yield-reducing and costly defects can easily catch even the most seasoned engineers and production personnel off guard. In this month’s column, I’ll investigate copper plating voids with their genesis in the pre-plating process steps.
Experienced engineers often say that many process steps and variables will influence the success or failure of obtaining a continuous void-free copper deposit in the hole. Everything in the process is critical to the success of the overall metallization process.
One of the obvious causes of voids, or at least inadequate copper coverage, is the result of poor drilling. Figure 1 shows rough hole walls and torn-out glass bundles. A closer look at this section shows a very poorly drilled hole wall, with glass bundles protruding from the resin, as well. This is a potential cause of voiding. The rough hole walls with broken glass fibers make metallization with electroless copper challenging. The result is often a plating void or a significant thinning of the metal deposit. Later, this may lead to the electroless copper being etched away by the micro-etching step prior to electrolytic copper plating.
One should immediately investigate the drilling operation, looking at the following:
- Drill bit quality: How many hits and what is the overall condition of the drill tool?
- Spindle feeds and speeds: Is the drill tool punching its way through the stack?
- Slow up feed causing the torn-out glass bundles: It should be 2x the infeed rate.
- Check chip loads: Experiment with different chip loads to improve quality.
- Stack height: How many PCBs are in the drill stack? Consider reducing number to improve quality.
Figure 2 shows a horizontal section of a plated through-hole (PTH). Again, note the poor quality in the hole wall and its effect on the plating process.
The desmear operation is another potential cause of PTH voids. The most effective desmear process available today is based on alkaline permanganate. Although, with the development of new materials for the high frequency/low loss space and materials for improved longer-term reliability, adjustments in the desmear operation may be warranted. This would include the use of plasma desmear or a combination of plasma and permanganate. I will elaborate on this subject in a future column.
The use of alkaline permanganate for multilayer circuit boards has had a dramatic effect on copper coverage and adhesion in the plated through-hole. However, this process, if not controlled, can be a major cause of voids. First, the process consists of four main chemical process steps:
- A solvent conditioner designed to penetrate the polymer matrix of the resin system and weaken the polymer-polymer bonds of the cross-linked chain.
- The alkaline permanganate solution consisting of sodium or potassium permanganate and its corresponding hydroxide salt.
- A neutralizer (possibly in combination with glass etch) for removing manganese residues.
- Glass etch as a separate step to lightly roughen (frost) or more aggressively remove glass fibers that may be protruding into the hole due to etch-back.
If any of these four steps is not controlled, it can lead to voids. If this is the case, even the most robust electroless copper processes will not be able to compensate.
The effective alkaline permanganate process not only removes drill smear, but will micro-roughen the resin as shown in Figure 3. This texturing is often referred to as the honeycombed appearance. This is desirable for two reasons:
- The textured surface promotes palladium catalyst adsorption which in turn promotes electroless copper deposition and coverage.
- Surface improves copper adhesion.
This promotes improved solderability by minimizing or eliminating the occurrence of blowholes seen in the wave soldering operation. I will explain more about blowholes in a future column.
Regardless, if the texturing is inadequate, the possibility of voids exists. With insufficient catalyst anywhere on the via wall, the electroless copper deposition will fail to initiate, thus leading to a void in that area. Electroless copper processes require an adequate amount of catalyst on the hole wall in order to promote electroless copper deposition. Key questions to ask in the brainstorming session:
- Is the solvent conditioner (swellant) making sufficient penetration into the resin matrix and is the solvent system compatible with the resin? Note that some of the higher Tg resins do not react the same as standard FR-4. The higher degree of cross-linking of the polymer resin makes it more difficult for the solvent to penetrate and thus weaken the polymer-polymer bonds in the resin. This, in turn, reduces the action of the permanganate solution in terms of resin removal and texturing.
- Check the operating temperature of the alkaline permanganate solution, as well as the hydroxide and actual permanganate content. The hydroxide content aids in promoting the aggressiveness of the permanganate attack on the resin. The permanganate in the +7 oxidation state will perform the actual oxidization and breakdown of the resin. Manganate (+4) is a by-product of this reaction and will not participate in the resin oxidation. Manganate residue should be controlled and maintained below 20-25 grams/liter. Otherwise, as manganate builds up over time, the rate of resin removal and texturing will diminish. If solvent compatibility and degree of penetration is sufficient, then consider utilizing a higher concentration of permanganate. Sodium permanganate will allow for more actual permanganate in solution over the corresponding potassium salt.
- Finally, review the neutralizer and glass-etch. A major cause of voiding is due to manganate residues remaining on the hole wall resin and glass. One should frequently renew this solution to ensure fresh working chemistry. Also, check the acid concentration. Lower concentration reduces the effectiveness of neutralization. Often, in order to reduce process steps, fabricators will combine the neutralizer and glass etch in the same process tank. (I prefer separate steps as the process is more effective). As the glass etch weakens due to continued use, the ability of the glass etch to roughen the glass fibers (referred to as “frosting”) is reduced. This reduces the ability of the catalyst to adhere to glass. When this happens, voids are the result.
This column originally appeared in the April 2025 issue of PCB007 Magazine.
More Columns from Trouble in Your Tank
Trouble in Your Tank: Metallizing Flexible Circuit Materials—Mitigating Deposit StressTrouble in Your Tank: Can You Drill the Perfect Hole?
Trouble in Your Tank: Yield Improvement and Reliability
Trouble in Your Tank: Organic Addition Agents in Electrolytic Copper Plating
Trouble in Your Tank: Interconnect Defect—The Three Degrees of Separation
Trouble in Your Tank: Things You Can Do for Better Wet Process Control
Trouble in Your Tank: Processes to Support IC Substrates and Advanced Packaging, Part 5
Trouble in Your Tank: Materials for PWB Fabrication—Drillability and Metallization