-
- News
- Books
Featured Books
- pcb007 Magazine
Latest Issues
Current IssueInventing the Future with SEL
Two years after launching its state-of-the-art PCB facility, SEL shares lessons in vision, execution, and innovation, plus insights from industry icons and technology leaders shaping the future of PCB fabrication.
Sales: From Pitch to PO
From the first cold call to finally receiving that first purchase order, the July PCB007 Magazine breaks down some critical parts of the sales stack. To up your sales game, read on!
The Hole Truth: Via Integrity in an HDI World
From the drilled hole to registration across multiple sequential lamination cycles, to the quality of your copper plating, via reliability in an HDI world is becoming an ever-greater challenge. This month we look at “The Hole Truth,” from creating the “perfect” via to how you can assure via quality and reliability, the first time, every time.
- Articles
- Columns
- Links
- Media kit
||| MENU - pcb007 Magazine
Estimated reading time: 3 minutes
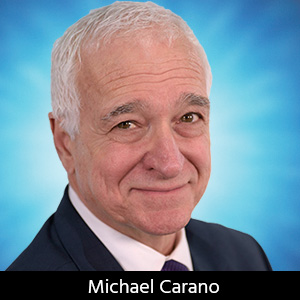
Contact Columnist Form
Trouble in Your Tank: Organic Addition Agents in Electrolytic Copper Plating
There are numerous factors at play in the science of electroplating or, as most often called, electrolytic plating. One critical element is the use of organic addition agents and their role in copper plating. The function and use of these chemical compounds will be explored in more detail.
Organic Addition Agents
The organic addition agents serve several functions with respect to acid copper electrodeposits. First and foremost, they mediate the electrodeposition process by influencing secondary current distribution (discussed in a previous column) and controlling the physical properties of the copper deposit. The key physical properties of the deposit are tensile strength and elongation.
What is the significance of tensile strength and elongation, otherwise known as ductility? During the normal performance of a printed circuit board, the copper deposit will undergo flexing. An example would be a satellite orbiting the globe, being intermittently heated and cooled as the device makes its way around the earth. The copper deposit within the PCB will undergo flexing, which leads to fatigue in the deposit. Cracking of the deposit within the barrel of the hole is the result of this fatigue. The deposit must have sufficient tensile strength to be able to withstand fatigue cracking. It is well understood that the organic addition agents utilized in acid copper plating processes influence the deposit’s physical properties.
One can think of tensile strength as the ability to withstand shock, vibration, and flexing. This is where tensile strength comes in. Certainly, you may surmise, there is a symbiotic relationship between tensile strength and elongation. These two properties greatly influence the performance of the copper plating especially under thermal stress and mechanical stress conditions. Essentially, it is not possible to achieve extremely high tensile strength and very high elongation values. There is a trade-off. As tensile strength increases, ductility declines, and vice versa. However, that is a good thing. There is the sweet spot as shown in Figure 1.
These organic addition agents influence the physical properties of the copper deposit. This includes grain refinement, and leveling of the deposit through the surface, and vias. When controlled properly, the addition agents add strength to the deposit. This added strength or robustness permits the deposit to withstand the thermal and mechanical excursions that the circuit board will be subjected to. This allows the deposit to achieve the sweet spot for reliability (Figure 1).
Let’s take a closer look at the functions of the various addition agents that make up most commercial addition agents’ systems.
Construction of the Acid Copper Addition Agent
Acid copper additives contain at least one material described as a brightener and a second material that is described as a high molecular weight polymeric compound. Optionally, the additive package also contains a leveling agent. Each of these materials will now be described in some detail:
Brightener
The brightener is classed as nitrogen or sulfur containing compound that by coulombic attraction, forms a layer on the copper surface where it enters—together with CI—in the one-electron transfers: Cu++ ® Cu+ ® Cu0. Brightener “masks” preferential growth sites on the planes. Even with the brightener, the growth of the plated copper shows little directional preference. The grain structure of the copper is semi-amorphous microcrystalline. This is why a carrier-type molecule is needed.
Carrier
This class of organic materials is a high molecular weight compound. These materials, such as polyvinyl alcohols and polyethylene glycols (PEGs), are designed to exert a strong plating suppression effect on the high current density areas of the cathode. These carriers aid in preventing overplating in the high current density areas. These high molecular weight polymers form a diffusion barrier along the cathode surface.
The Leveling Agents
Typical leveling agents indicated here are based on polyamine compounds. These are very low molecular weight. Leveling agents exert an influence over non-uniform areas within the via and on the surface. Working in synergistic fashion with the carrier, the leveling agent carries a positive charge and thus is able to migrate to the most negatively charged areas of the cathode—the highest current density areas. These higher current density areas, if unmitigated, will see more current than lower current density areas. These higher current areas are the edges of the circuit board, protrusions, and surfaces of the vias versus the holes. The leveling agent selectively slows down the deposition of copper and helps to shift some of the plating away from the high current areas to the lower current density areas.
So many people I have worked with over the years considered plating chemistry as black magic or foo-foo dust. The workings of plating chemistry are not magic, but based on science.
This column originally appeared in the March 2025 issue of PCB007 Magazine.
More Columns from Trouble in Your Tank
Trouble in Your Tank: Metallizing Flexible Circuit Materials—Mitigating Deposit StressTrouble in Your Tank: Can You Drill the Perfect Hole?
Trouble in Your Tank: Yield Improvement and Reliability
Trouble in Your Tank: Causes of Plating Voids, Pre-electroless Copper
Trouble in Your Tank: Interconnect Defect—The Three Degrees of Separation
Trouble in Your Tank: Things You Can Do for Better Wet Process Control
Trouble in Your Tank: Processes to Support IC Substrates and Advanced Packaging, Part 5
Trouble in Your Tank: Materials for PWB Fabrication—Drillability and Metallization