-
- News
- Books
Featured Books
- pcb007 Magazine
Latest Issues
Current IssueInventing the Future with SEL
Two years after launching its state-of-the-art PCB facility, SEL shares lessons in vision, execution, and innovation, plus insights from industry icons and technology leaders shaping the future of PCB fabrication.
Sales: From Pitch to PO
From the first cold call to finally receiving that first purchase order, the July PCB007 Magazine breaks down some critical parts of the sales stack. To up your sales game, read on!
The Hole Truth: Via Integrity in an HDI World
From the drilled hole to registration across multiple sequential lamination cycles, to the quality of your copper plating, via reliability in an HDI world is becoming an ever-greater challenge. This month we look at “The Hole Truth,” from creating the “perfect” via to how you can assure via quality and reliability, the first time, every time.
- Articles
- Columns
- Links
- Media kit
||| MENU - pcb007 Magazine
Estimated reading time: 5 minutes
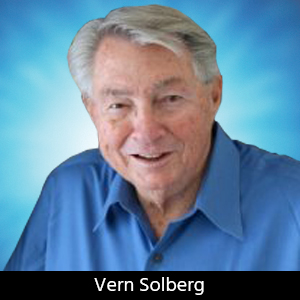
Flex and Rigid-Flex Circuit Design Principles, Part 2
Flexible circuits are commonly developed to replace ordinary printed circuit board assemblies that rely on connectors and hardwire for interconnect. Further, because of the base materials’ durability, flexible circuits have proven to be a more reliable solution for telecommunications, computers, automotive, medical, and aerospace, as well as a wide range of other important applications. The major benefit of the flex circuit over a hardwire interface is the reduction of weight, enhanced reliability and the potential for reduced cost over the life of the end product.
In preparation for developing the flexible or rigid-flex circuit, the PCB designer must gain a reasonably good understanding of the fabrication process and the design guidelines furnished by the potential supplier. Most fabricators welcome the opportunity to discuss the project prior to the actual design process. While they often furnish their companies’ unique capabilities and general design guidance, they will also likely recommend following the industry-established Design Standard for Flexible Printed Boards, IPC-2223 as well. This standard was actually developed by flexible circuit manufacturers, material suppliers and users. The document establishes the specific requirements for the design of flexible printed circuit applications and its forms for accommodating component mounting and interconnecting with associated structures.
Supplier Capability Assessment
Fabrication of flexible and rigid-flex circuits requires unique skills. A broad number of companies have specialized in flexible circuit manufacturing and understand the complexities of processing film-based products. Experience goes a long way. You may already have a business relationship with a reliable supplier for rigid PCBs. But a majority of companies working with traditional rigid organic materials have avoided flex because it is perceived as too complex, too hard to handle, etc.
The first step when researching alternative sources is to look for companies that are already producing quality flexible circuits. Review their technical capabilities and company history. Some specialize in fabricating only one and two metal-layer flex, while others are very comfortable with rigid-flex manufacturing. Some of the issues to consider when selecting the supplier are ease of communication and the physical location of their fabrication facility. The Internet is a good place to begin your search, but you may want to consult with other flexible circuit users for recommendations because they may have already qualified one or more suppliers.
In your search, look for companies that have published feature size capability, material variations, stack-ups and any unique process capabilities they may offer. In regard to feature size capability, features include lines and space recommendations, and via size range. Other physical issues include drilled-hole location tolerance to datum, minimum clearance from copper conductor to mechanically drilled or punched mounting holes, and minimum conductor to edge of board spacing. For rigid-flex applications, the designer will need to establish layer count limitation, ability for furnishing blind/buried vias and sequential lamination capability.
Flex Circuit Outline Planning
Prior to beginning the design phase of the flexible or rigid-flex circuit, the designer will need to develop a model, a non-functional mechanical mock-up of the circuit. The model will allow physical adjustment of the key features, connector to connector, connector to rigid board, rigid board-to-board and so on. Assuming that the designer is furnished with a wiring diagram or schematic of the circuit, conductor density between primary features can be established.
If the circuit includes solder attachment of components and/or connectors, the area(s) needed for mounting and interface must be estimated. Furthermore, it is common practice to furnish some form of reinforcement in the component mounting areas to minimize mechanical stress on the solder interface. Reinforcement may be as simple as an additional layer of the flexible film or non-functional rigid material laminated to the surface under the components mounting zone. Providing reinforcement material under the connector mounting area in particular will minimize stress on the solder interface when subjected to repeated use.
Factors to consider:
- Quantity of signal traces and surface area required across the flexible area
- Line widths required for current-carrying capacity
- Spacing required for voltage isolation
- EMI shielding and impedance control requirement
- Voltage drop limitations
Circuit routing principles
With regard to conductor density, the designer must first establish the general conductor width and space (L/S) in the flexible section between primary features. Although many designers will want to maximize conductor density in this area of the circuit, the actual minimum conductor width will be dictated by three factors: copper thickness, electrical current carrying capacity and the fabricators capability. Purely signal carrying conductors can rely on very narrow copper circuit topography, but when the electrical current reaches 0.5A or greater, a wider circuit path must be established, For example, a reliable flexible circuit supply source recommends that when conductors are carrying 0.5A using ½ oz. (17 micron) thick copper, the conductor width should be around 330 microns (0.013”). When 1 oz. (34 micron) thick copper is specified, the conductor width can be pared down to 200 microns (0.008”). When flexible circuits are designed for higher amperage loads for power distribution, these numbers will grow significantly.
Fabricators recommend that designers avoid unnecessary circuit thickness in the bend zone because it can hinder flexible capabilities. If a portion of the flex circuit needs to be thicker for supporting components or connectors, add a stiffener. Suppliers further note that calculating bend cycles over the projected life of the product is crucial to your design. If a circuit is flexed beyond the limits established, the copper foil may begin to stretch and crack. A general rule of thumb for estimating minimum bend radii is 6x material thickness for single metal circuits and 12x for two metal-layer circuits.
Furthermore, to avoid fatigue of the thin copper foils in the flex zone, conductors should be perpendicular to the bend and maintain a uniform width and spacing. When the conductor’s path must change direction, the designer must avoid sharp 90° turns. Ideally, the conductor paths will be designed with generous radii. Multiple conductor paths routed in parallel should also maintain uniform spacing with progressively larger radii from the center axis. Not all CAD software has the curved, nested conductor routing capability; however, most of the software specifically developed for flexible circuit design will.
Another fatigue potential lies in the transition of the narrow circuit geometry to a larger feature and connector mounting pads and land patterns provided for surface mount components. Reinforcement at the interface can be as simple as supplying a tear-drop-shaped fillet at the transition between the narrow conductor and the wider contact feature. For holes furnished for mounting pin-in-hole components it is good design practice to make the mounting pad area as large as possible. This will maximize adhesion area during the soldering process.
To further reduce adhesion concerns, the designer can provide additional anchor features. Anchors can be as simple as incorporating one or more outward copper spoke-like protrusions placed around the pads perimeter. Then, when the cover-layer film is laminated onto the flexible base it will overlap the reinforcement features and negate the potential adhesion failures.
More Columns from Designer's Notebook
Designers Notebook: Basic PCB Planning Criteria—Establishing Design ConstraintsDesigners Notebook: Layer Stackup Planning for RF Circuit Boards
Designers Notebook: Addressing Future Challenges for Designers
Designers Notebook: Impact of Advanced Semiconductor Packaging on PCB Stackup
Designers Notebook: Implementing HDI and UHDI Circuit Board Technology
Designer's Notebook: Heterogeneous Integration and High-density SiP Technologies
Designers Notebook: PCB Design and IPC-CFX for Assembly Automation
Designer’s Notebook: What Designers Need to Know About Manufacturing, Part 2