-
- News
- Books
Featured Books
- design007 Magazine
Latest Issues
Current IssueProper Floor Planning
Floor planning decisions can make or break performance, manufacturability, and timelines. This month’s contributors weigh in with their best practices for proper floor planning and specific strategies to get it right.
Showing Some Constraint
A strong design constraint strategy carefully balances a wide range of electrical and manufacturing trade-offs. This month, we explore the key requirements, common challenges, and best practices behind building an effective constraint strategy.
All About That Route
Most designers favor manual routing, but today's interactive autorouters may be changing designers' minds by allowing users more direct control. In this issue, our expert contributors discuss a variety of manual and autorouting strategies.
- Articles
- Columns
- Links
- Media kit
||| MENU - design007 Magazine
Estimated reading time: 4 minutes
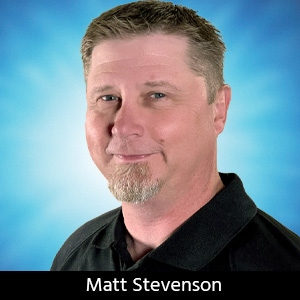
Connect the Dots: Best Practices for Ensuring PCB Design Manufacturability
It makes sense to optimize your board using design for manufacturability (DFM) techniques, but applying DFM best practices can be confusing without formal training. The results are designs that are often incomplete, poorly designed, or too complex.
When these issues arise, your PCB manufacturing partner rejecting the design can be considered a best-case scenario because it means they have your back. If your design is simply dropped into an automated queue without concern for manufacturability, the output can be a batch of unusable boards.
Expensive mistakes can be avoided by adopting practices that encourage design for manufacturability. In addition, carefully choosing a manufacturing partner and service level that align with your needs will help you achieve a quality result.
Let us examine some design best practices that will help reduce costs, increase yield, and improve manufacturability.
Study the Rulebook
It is up to you to be familiar with the design rules. Not every manufacturer prioritizes making DFM rule sets for popular design tools available, cost-effective, and current. Working with a manufacturer who does make rules available will save time and money.
Of course, using design rule checks (DRC) alone will not guarantee manufacturability, but performing them is a great way to ensure that you have created as close to an error-free design as possible.
Remember that error-free is an unattainable point on the horizon you can almost see, but never quite catch. The goal should be a design that lowers the risk of defects and can then be manufactured and assembled. The DRC will help you identify conflicts, such as issues with insufficient clearances between electrical conductors, that will affect electrical functions and create potential manufacturability issues.
Always Review Your Design
We strongly encourage you to always review your design. Take a second look for issues such as insufficient power trace widths, blind vias, and components that are laid out too close together. When a design pushes the manufacturer's tolerances, it is easy to accidentally cut holes or route slots too close to pads or traces.
Copper thickness is another important design consideration. Higher current may require thicker copper and narrow traces probably should be thinner. Be specific about what you need to ensure your design will not fail. Check land patterns against the part supplier’s manufacturer datasheets (MDS) as well. Often, that is all it takes to avoid common design issues.
Consider How Your End Product Will Be Used
Your manufacturing partner does not know what type of device the board will be part of, or the conditions in which it will have to perform. It’s common for harsh environments or exposure to interfere with a board’s performance. To avoid catastrophic failure down the road, you must call out materials that will tolerate the final product's operating environment. Be sure your board and components can tolerate thermal stress or solder joints risk breaking and damaging components.
Adhere to the Principles of DFM
We recommend integrating all these best practices into a design process that looks forward to the manufacturing process. Finding issues earlier makes them cheaper and easier to fix. From the outset, perform all design tasks while considering yield and other manufacturing issues that affect cost and quality.
Communicate with your manufacturing partner regularly throughout the design process. They can do more than just find problems. A good manufacturing partner has valuable insight into how design decisions impact manufacturability, yield, and quality of the boards.
Each manufacturer has unique capabilities and process requirements that can have a large impact on the manufacturability of your design, making an open line of communication critical. For example, your suppliers can confirm that you are using up-to-date footprint files throughout the design process.
Highly manufacturable designs exist within a range of specifications. Manufacturers can often help you tweak your design to make the best use of these ranges. Designer/manufacturer communication about DFM can help save time, reduce costs, and even improve the functionality of your board.
Help When You Need It
Choosing a manufacturing partner with readily available support staff can help you solve manufacturability puzzles during the design process, rather than after submission. It’s useful to ask a few questions of any potential manufacturing partner before deciding.
- Is competent technical support available when you need it?
- How quickly will they respond to your needs?
- Email is slow, so how can you get support for time-sensitive issues?
- What is their escalation policy for difficult support requests?
- What support packages are available and how much do they cost?
The real key to optimizing the manufacturability of your PCB designs is choosing the right tools, process, and manufacturer that meet the needs of your design. Treat your parts suppliers, PCB manufacturer, and PCB fabricator as members of your design team. Prioritize open and persistent collaboration with each of them.
Good communication and adherence to a DFM-focused process will ensure board quality, manufacturability, and cost-effectiveness.
Download The Printed Circuit Designer’s Guide to… Designing for Reality by Matt Stevenson. You can view other titles in the I-007eBooks library.
This column originally appeared in the November 2023 issue of Design007 Magazine.
More Columns from Connect the Dots
Connect the Dots: Sequential Lamination in HDI PCB ManufacturingConnect the Dots: The Future of PCB Design and Manufacturing
Connect the Dots: Proactive Controlled Impedance
Connect the Dots: Involving Manufacturers Earlier Prevents Downstream Issues
Connect the Dots: Stop Killing Your Yield—The Hidden Cost of Design Oversights
Connect the Dots: Designing for Reality—Routing, Final Fab, and QC
Connect the Dots: Designing for Reality—Surface Finish
Connect the Dots: Designing for Reality—Solder Mask and Legend