-
- News
- Books
Featured Books
- pcb007 Magazine
Latest Issues
Current IssueInventing the Future with SEL
Two years after launching its state-of-the-art PCB facility, SEL shares lessons in vision, execution, and innovation, plus insights from industry icons and technology leaders shaping the future of PCB fabrication.
Sales: From Pitch to PO
From the first cold call to finally receiving that first purchase order, the July PCB007 Magazine breaks down some critical parts of the sales stack. To up your sales game, read on!
The Hole Truth: Via Integrity in an HDI World
From the drilled hole to registration across multiple sequential lamination cycles, to the quality of your copper plating, via reliability in an HDI world is becoming an ever-greater challenge. This month we look at “The Hole Truth,” from creating the “perfect” via to how you can assure via quality and reliability, the first time, every time.
- Articles
- Columns
- Links
- Media kit
||| MENU - pcb007 Magazine
Estimated reading time: 4 minutes
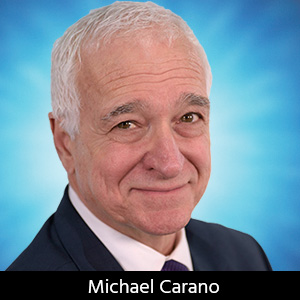
Contact Columnist Form
Trouble in Your Tank: Electrodeposition of Copper, Part 2
Introduction
If one thought that electroless copper and other metallization systems were complex and the deep dark secrets of these systems shrouded in black magic, the discussions on electroplating will seem like brain surgery.
In this next series of columns, the intricacies of electrodeposition technology and its function of building up the thickness of copper in the holes and on the surface will be presented in detail. Function of the active ingredients in the copper plating solutions will be presented. Process control limits for the various plating solution components and the effects on deposit integrity will be discussed.
Electrodeposition
In contrast to the classic initial through-hole metallization with electroless copper, the buildup of the conductive layer in the through-hole to the desired thickness is being achieved by the electrodeposition of copper. It is understood that these technologies overlap, i.e., some initial metallization processes use direct electroplating and, conversely, fully additive processes build up copper solely with the electroless process.
The historic preference for building up the copper deposit by electroplating has to do with the lower cost, faster deposition rate, and in general, better metallurgical properties of the electroplated copper. Improvements concentrated on the “throwing copper” of the electrolytes, i.e., their ability to deposit a relatively uniform deposit of copper on the board surface and in the through-holes. A shift to higher acid and lower copper concentrations, as well as improved organic additives systems (brighteners, carriers, levelers), gave improved throwing power. And let’s not underestimate the influence that plating cell design, cabling connections from the power supply to the buss bars, and solution movement have on plating distribution and the overall quality of the deposit.
Additional challenges and complications have been introduced due to the changes in circuit board design technology. Shifts in circuit designs toward higher density and ultra-high density have ushered in a new wave of improvements in process technology.
Several other electroplating processes are used in the fabrication of the printed wiring boards. Tin/lead or tin is electroplated, occasionally also electroless plated, to serve as a metal etch resist. Other electroplated metals include nickel/gold and palladium (also deposited from immersion baths or electroless baths) to form suitable surface finishes for insertion connectors or component attachment, e.g., wire bonding. An overview of these processes will be presented in a future column.
Focusing on the acid copper electroplating process, one would start with the preplate cleaning sequence of acid soak cleaner, micro-etch, and acid predip. The acid pre-dip is optional and if rinsing after micro-etching is sufficient, can be omitted. However, this only applies to using peroxide/sulfuric acid micro-etchants. Use of persulfate-based etchants indicates an acidic pre-dip. Critical acid cleaner variables are chemical composition, concentration, time, and temperature. Regarding the micro-etch, etch depth is the critical parameter, which in turn, is influenced by the chemical composition, concentration, time, and temperature. The acid predip, typically of the same acid and concentration as is used in the plating bath, protects the plating solution from undesirable drag-in, which might adversely affect the composition or concentration of the bath. Thus, chemical composition of the predip and its level of contaminants are critical.
Critical parameters of the acid copper bath include electrical, mechanical, physical, and chemical variables. Starting with the electrical parameters, current density and primary current density distributions affect plating rate, thickness distribution, and the metallurgical properties, e.g., ductility, roughness, and color of the deposit. Current density across the plating surface depends on the rectifier capacity, related anode and cathode sizes and spacing, shielding, cell efficiency, and solution conductivity. Current density distribution across the plating surface depends on some of the before-mentioned parameters and, in pattern plating, also on the circuit pattern.
Current density in the through-hole depends on the following additional variables:
- Through-hole diameter and aspect ratio
- Replenishment efficiency (in the holes) of plating solution (agitation)
- Throwing power of the bath, which is largely determined by the acid/copper ratio, the organic plating additives, and the level of impurities (leachants) that interfere with the organic plating additives.
In Figure 1, throwing power is defined for purposes of this and subsequent columns. The actual mechanics of the electrodeposition process and the influence of process parameters will be discussed in future columns.
The degree of difficulty for plating through-holes depends on board thickness as well as hole diameter. For example, given a choice of two holes, both 10:1 in aspect ratio, one prefers a design with a 100-mil thick panel and a via with a 10-mil diameter, vs. a 200-mil thick panel with 20-mil diameter holes. Both designs are of the same aspect ratio.
Figure 2 underscores the difficulty in maintaining throwing power as the aspect ratio and board thickness increase. It illustrates that the IR drop (or the electrical resistance through the via) increases as a squared factor, while via diameter only affects the resistance (or throwing power) in a linear fashion.
In my next column, I will continue to explore the electrodeposition process and the science behind the technology.
This column originally appeared in the July 2022 issue of PCB007 Magazine.
More Columns from Trouble in Your Tank
Trouble in Your Tank: Metallizing Flexible Circuit Materials—Mitigating Deposit StressTrouble in Your Tank: Can You Drill the Perfect Hole?
Trouble in Your Tank: Yield Improvement and Reliability
Trouble in Your Tank: Causes of Plating Voids, Pre-electroless Copper
Trouble in Your Tank: Organic Addition Agents in Electrolytic Copper Plating
Trouble in Your Tank: Interconnect Defect—The Three Degrees of Separation
Trouble in Your Tank: Things You Can Do for Better Wet Process Control
Trouble in Your Tank: Processes to Support IC Substrates and Advanced Packaging, Part 5