-
- News
- Books
Featured Books
- pcb007 Magazine
Latest Issues
Current IssueInventing the Future with SEL
Two years after launching its state-of-the-art PCB facility, SEL shares lessons in vision, execution, and innovation, plus insights from industry icons and technology leaders shaping the future of PCB fabrication.
Sales: From Pitch to PO
From the first cold call to finally receiving that first purchase order, the July PCB007 Magazine breaks down some critical parts of the sales stack. To up your sales game, read on!
The Hole Truth: Via Integrity in an HDI World
From the drilled hole to registration across multiple sequential lamination cycles, to the quality of your copper plating, via reliability in an HDI world is becoming an ever-greater challenge. This month we look at “The Hole Truth,” from creating the “perfect” via to how you can assure via quality and reliability, the first time, every time.
- Articles
- Columns
- Links
- Media kit
||| MENU - pcb007 Magazine
Estimated reading time: 4 minutes
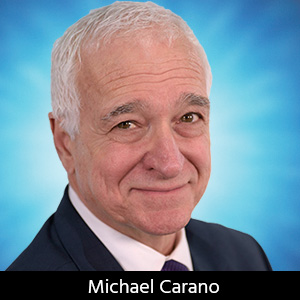
Contact Columnist Form
Trouble in Your Tank: A Process Engineer’s Guide to Etching Defects-Part 3
Introduction
While troubleshooting everyday processing issues, final etching touches on many downstream processes. These include surface preparation, imaging, and copper surface quality. There are concerns with the etching process itself and how process issues and operating parameters impact the circuit formation quality. In this month’s edition of “Trouble in Your Tank,” the subject of etch-outs, undercut, and line width reduction will be presented.
Overview-Etch Factor and Undercut
Electrical engineers and circuit board designers are not thrilled if, as fabricators, you don’t give them the line width and spacing (as well as the circuit geometry) that was initially intended. Issues such as undercut and over-etching will detract from the circuit trace quality. However, the constant battle is minimizing undercut while ensuring the unwanted copper is completely removed during the etching process.
Let’s discuss the difference between the undercut and etch factor. The undercut is the difference between the width of the developed resist line (it could also be the design line width) and the final width of the etched circuit across the top. Expressed another way, undercut is the amount of copper that was removed laterally as the etchant did its job of eliminating unwanted copper as it etches downward (Figure 1).
The etch factor is the ratio between the difference in the widths of the copper trace at the most expansive and narrowest parts of the feature after etching is completed and the metal's thickness (copper) etched. The etch factor can be easily expressed as a ratio by dividing the copper's thickness etched downward by the amount of copper removed laterally.
Please note that Figure 1 describes conditions related to print-and-etch (typically known as image-develop-etch); the same concepts apply, only with a slightly different twist where outer layer technology is concerned. With a metal etch resist and final etching as typically seen with outer layer technology, undercut continues to be an issue. However, excessive undercut and the overall etch profile (Figure 2) leads to the overhang of the plated etch resist. The concern here is the excessive undercut may allow a metal sliver to break off during processing and cause additional issues, such as a short. Regardless, the factors at play remain the same.
One can review the requirements in the IPC-A-600 detailing issues with metal overhang.
Again, process engineering needs to pay close attention to the etching process to minimize the undercut both on inner layers and outer layers.
The undercut is exacerbated when the thickness of the copper foil and plated copper is thick. Think of 1-ounce copper foil (typically 1.4 mils thick) along with a minimum 1.0 mil of electroplated copper. In practice, the electroplated copper is often considerably thicker than 1.0 mil, further increasing the undercut opportunity.
Alkaline Etching
What can be done then, from a process standpoint, to minimize undercut? And in a worst-case scenario, what can be done to reduce significant line width reduction or complete etch-out (open)? To answer these questions, one must consider all the factors that can influence undercut and overall etching speed.
It has been established that undercut factors are grouped into three categories: etching chemistry, etching equipment, and other effects that are not due to either chemistry or equipment. These include surface preparation, exposure, development, etc. More on that later.
The process control of the chemical and other operating parameters (temperature, specific gravity, pH, etc.) of alkaline etching is paramount to ensuring consistent quality and high yields. Cupric chloride etching (acid-based) has several other critical chemical parameters that affect undercut and etch rate.
There are two specific parameters concerning alkaline etching that have a significant (read: heavily weighted) effect on the undercut and etch rate. Unfortunately, the etch rate and undercut move in opposite directions. A slower copper etching rate, while a drag on productivity, allows for the reduced undercut. Keeping the pH in a tight range of 8.0-8.2 is ideal when alkaline etchants are employed for print-and-etch applications. Some formulated alkaline etchants can operate at a pH of 7.9. While this is ideal for minimizing undercut, if the pH drops further, there is the risk of the etchant sludging out.
Conversely, as copper concentration builds in the etchant chemistry, specific gravity increases. A combination of low pH and higher specific gravity provides a positive benefit in reducing undercut. However, the reduced undercut comes at the expense of slower copper etching speeds. Indeed, higher operating temperatures will increase etch rates with a corresponding increase in the undercut.
Outer Layer Etching
There are several additional concerns when employing etching as part of the strip-etch-strip process (in preparation for SMOBC—solder mask over bare copper). First, one cannot use cupric chloride as a final etchant on metal etch resist processed circuit boards. Thus, one can default to alkaline ammoniated etching technology. However, there are additional challenges related to etching pattern-plated outer layers. These include the need to etch through thicker copper (copper foil thickness plus the pattern-plated copper on top of the foil copper). As the reader recalls, the greater the copper thickness that the etchant must remove in the Z-axis, the greater the potential for undercut. As the plated copper increases or if the foils used are more than one-ounce foils, undercut increases. All the process engineer can do is maintain tighter controls on the operational and chemical parameters.
First and foremost, if undercut is minimized, there is less opportunity for overhang (Figure 3). In this case, the undercut is somewhat excessive. We can see how the etching solution affects the copper while leaving the tin plating intact. The strip of tin that is left floating at the edge of the feature represents the etching factor. The etching factor is the difference of dimension between the film and the final width of the features.
In a future column, we will delve further into the interrelationship of final etching, electroplating, surface preparation, and imaging.
This column originally appeared in the January 2021 issue of PCB007 Magazine.
More Columns from Trouble in Your Tank
Trouble in Your Tank: Metallizing Flexible Circuit Materials—Mitigating Deposit StressTrouble in Your Tank: Can You Drill the Perfect Hole?
Trouble in Your Tank: Yield Improvement and Reliability
Trouble in Your Tank: Causes of Plating Voids, Pre-electroless Copper
Trouble in Your Tank: Organic Addition Agents in Electrolytic Copper Plating
Trouble in Your Tank: Interconnect Defect—The Three Degrees of Separation
Trouble in Your Tank: Things You Can Do for Better Wet Process Control
Trouble in Your Tank: Processes to Support IC Substrates and Advanced Packaging, Part 5