-
- News
- Books
Featured Books
- pcb007 Magazine
Latest Issues
Current IssueInventing the Future with SEL
Two years after launching its state-of-the-art PCB facility, SEL shares lessons in vision, execution, and innovation, plus insights from industry icons and technology leaders shaping the future of PCB fabrication.
Sales: From Pitch to PO
From the first cold call to finally receiving that first purchase order, the July PCB007 Magazine breaks down some critical parts of the sales stack. To up your sales game, read on!
The Hole Truth: Via Integrity in an HDI World
From the drilled hole to registration across multiple sequential lamination cycles, to the quality of your copper plating, via reliability in an HDI world is becoming an ever-greater challenge. This month we look at “The Hole Truth,” from creating the “perfect” via to how you can assure via quality and reliability, the first time, every time.
- Articles
- Columns
- Links
- Media kit
||| MENU - pcb007 Magazine
Estimated reading time: 1 minute
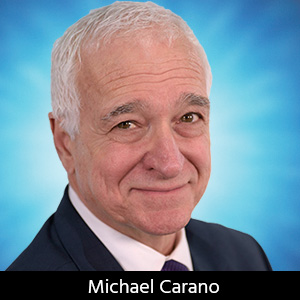
Contact Columnist Form
Trouble in Your Tank: Working With Flexible Circuits
Flexible circuits were first introduced as a replacement for wire harnesses. The earliest versions date back to World War II. Today, flex and rigid-flex circuits are filling an important role across multiple industries, including applications in the medical, automotive, and telecommunications fields.
Even though they are a smaller part of the circuit board industry, flex and rigid-flex circuits have been growing in popularity over the last decade, and for good reasons. These circuits are made to be thin, flexible, and durable. However, in addition to the opportunities that come with flex and rigid-flex circuits, there are also challenges. Generally, these occur with the processing part of the technology.
Characteristics of Flex and Rigid-flex Circuits
Flex and rigid-flex circuits have become a go-to solution for a variety of applications because they offer capabilities that simply aren’t available from alternatives. They can be manufactured to very thin specifications, and they will survive bending and folding without error.
These circuits can be run over long distances to make a connection. For example, some users have designed 14–18-foot flexible cables.
Some of the most sought-after features of flex and rigid-flex circuits include the following:
- Thin-core capability
- Improved dielectric constant
- Low dielectric constant (Dk) and dissipation factor (Df) critical concerns
- Ultra-fine line capable (L/S decreasing to less than 15 microns)
- Shorter interconnect distances
Flexible circuits have the same capabilities of their rigid counterparts, including repeatability, reliability, and high density. In addition, they have characteristics that make them more versatile than rigid circuits. For example, they are flexible, of course, and can resist vibration more effectively. One of the most popular features of flexible circuits is that they can be designed into three-dimensional configurations.
Rigid-flex circuits combine the best features of flexible and rigid circuits to meet a variety of needs. The rigid areas make it possible to mount stationary components while the flexible areas can be custom configured and serve as protection against vibration.
Despite the fact that flex boards can be extremely thin, they are remarkably durable. These circuits are capable of repeating the same bends through millions of cycles without interruption. This is a critical point when it comes to applications that face intense vibration and/or acceleration.
To read the full article, which appeared in the September 2019 issue of PCB007 Magazine, click here.
More Columns from Trouble in Your Tank
Trouble in Your Tank: Minimizing Small-via Defects for High-reliability PCBsTrouble in Your Tank: Metallizing Flexible Circuit Materials—Mitigating Deposit Stress
Trouble in Your Tank: Can You Drill the Perfect Hole?
Trouble in Your Tank: Yield Improvement and Reliability
Trouble in Your Tank: Causes of Plating Voids, Pre-electroless Copper
Trouble in Your Tank: Organic Addition Agents in Electrolytic Copper Plating
Trouble in Your Tank: Interconnect Defect—The Three Degrees of Separation
Trouble in Your Tank: Things You Can Do for Better Wet Process Control