-
- News
- Books
Featured Books
- pcb007 Magazine
Latest Issues
Current IssueInventing the Future with SEL
Two years after launching its state-of-the-art PCB facility, SEL shares lessons in vision, execution, and innovation, plus insights from industry icons and technology leaders shaping the future of PCB fabrication.
Sales: From Pitch to PO
From the first cold call to finally receiving that first purchase order, the July PCB007 Magazine breaks down some critical parts of the sales stack. To up your sales game, read on!
The Hole Truth: Via Integrity in an HDI World
From the drilled hole to registration across multiple sequential lamination cycles, to the quality of your copper plating, via reliability in an HDI world is becoming an ever-greater challenge. This month we look at “The Hole Truth,” from creating the “perfect” via to how you can assure via quality and reliability, the first time, every time.
- Articles
- Columns
- Links
- Media kit
||| MENU - pcb007 Magazine
Estimated reading time: 1 minute
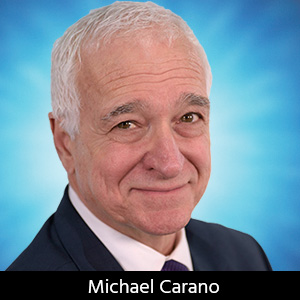
Contact Columnist Form
Trouble in Your Tank: Surface Preparation and Cleaning, Part 3
Surface preparation and cleaning are essential aspects of metal finishing and PCB fabrication. The PCB fabricator has several processes that fit the broad category of cleaning and surface preparation. However, the organization needs additional studies to enhance the broad portfolio of products for their respective fitness for use in today’s technology. In addition, this exercise will assess gaps in the RBP cleaning and surface preparation segment and make necessary process improvements through bench scale and field application trials.
Overview
In general, surface preparation is done to ensure good adhesion of metal, dielectric, photoresist, or solder mask to the prepared surface, although avoiding excessive adhesion could also be the objective. Take the example of surface preparation before dry photoresist lamination, such as failure to:
- Achieve good adhesion in a print-and-etch process, which will cause etchant attack under the resist and ultimately an open defect
- Achieve good adhesion in a plating process, which will cause tin and lead underplating, ultimately leading to shorting defects (shorts)
- Achieve a good release of unexposed resist during development, which can cause etch retardation in a print-and-etch process, ultimately leading to shorts
- Achieve a good release of unexposed resist during development in a plating process, which can cause poor adhesion of the plated copper to the copper base (copper-copper peelers)
- Achieve a good release of exposed resist in a print-and-etch process on inner layers, which can inhibit the formation of a multilayer bonder on such a copper surface
- Achieve a good release of exposed resist in a plating process, which can cause etch retardation
- Remove residues including chromates and organic soils (including resin spots), which will adversely affect inner layer bonding and plating quality
Figure 1 depicts an example of both an open and a short due to improper surface preparation leading to poor adhesion. To fully grasp some of the surface preparation issues, a primer on the copper foil manufacturing process will enhance the reader’s understanding with the composition and topography of standard electrodeposited (ED) and reverse-treated foils (drum-side-treated foils).
This article originally appeared in the December 2018 issue of PCB007 Magazine, click here.
More Columns from Trouble in Your Tank
Trouble in Your Tank: Minimizing Small-via Defects for High-reliability PCBsTrouble in Your Tank: Metallizing Flexible Circuit Materials—Mitigating Deposit Stress
Trouble in Your Tank: Can You Drill the Perfect Hole?
Trouble in Your Tank: Yield Improvement and Reliability
Trouble in Your Tank: Causes of Plating Voids, Pre-electroless Copper
Trouble in Your Tank: Organic Addition Agents in Electrolytic Copper Plating
Trouble in Your Tank: Interconnect Defect—The Three Degrees of Separation
Trouble in Your Tank: Things You Can Do for Better Wet Process Control