-
- News
- Books
Featured Books
- pcb007 Magazine
Latest Issues
Current IssueInventing the Future with SEL
Two years after launching its state-of-the-art PCB facility, SEL shares lessons in vision, execution, and innovation, plus insights from industry icons and technology leaders shaping the future of PCB fabrication.
Sales: From Pitch to PO
From the first cold call to finally receiving that first purchase order, the July PCB007 Magazine breaks down some critical parts of the sales stack. To up your sales game, read on!
The Hole Truth: Via Integrity in an HDI World
From the drilled hole to registration across multiple sequential lamination cycles, to the quality of your copper plating, via reliability in an HDI world is becoming an ever-greater challenge. This month we look at “The Hole Truth,” from creating the “perfect” via to how you can assure via quality and reliability, the first time, every time.
- Articles
- Columns
- Links
- Media kit
||| MENU - pcb007 Magazine
Estimated reading time: 4 minutes
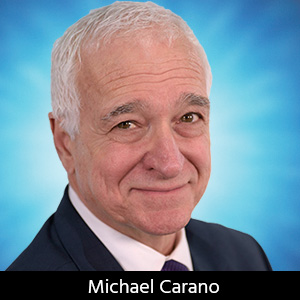
Contact Columnist Form
CASE STUDY: Pits and Mouse Bite Issues, Part 2
Introduction
In last month’s column, I introduced a case study that centered on plating pits and mouse bites. There were three areas in the process that raised concern as to the potential root cause of the defect. Of course, as with the case in all troubleshooting situations, it is best to look at the problem with wide open eyes. Just because one is looking at an issue that is visible after copper plating, this should not mean that is the only place to look. And this case study illustrates that point quite clearly.
The Problem
Again, keep in mind that there seems to be two very different types of plating defects. One particular pit seems to be random, and that there is no pattern that can be detected (Figure 1). In this case, these pits can be seen practically anywhere on the board. In addition, the characteristic of this type of pit essentially is found to go down to the base metal. In Figure 1, the reader can easily see that the plated copper is evident around the pitted area. The pit itself can be described as irregular in shape. Obviously not the same shape as a pit caused by an air bubble.
There can be several possibilities here. One issue may relate to organic contamination of the plating solution itself. Or, is it possible that the primary photoresist was improperly exposed and that allowed resist materials to leach onto the copper surface? In general, interactions between the photoresist and plating process are quite subtle.
Resists have been associated with a variety of plating failures. These failures increase in severity as the technology shifts to higher circuit densities and smaller vias and pads. There are some reasonably clear ties between plating problems and photoresist, as in the case of resist development residues causing copper-to-copper peelers, or stripping residues causing ragged plated lines after etching. One should ask if the pre-plate cleaning is effectively cleaning the copper surface (the area that is exposed after developing) prior to the electrodeposition of copper.
Now, remember the fabricator is also dealing with another type of pit that is more accurately described as a mouse bite. This defect is seen at the resist sidewall/copper interface. These pits are more spherical in shape and do not always lead to the base metal.
An inspection of the copper plating cells provided some additional information that should be noted: All the copper plating cells in the facility utilize air sparger agitation. An observation by a member of the tech team indicated that small air or gas bubbles in the copper plating cells were a potential cause of the spherical pits along the edges of the traces and pads. Further, the team felt that the air agitation created very small air or gas bubbles that would lodge onto the resist sidewall leading to the spherical pits. The agitation system for these plating cells required further scrutiny.
To test the theory that air bubbles could be causing the defect, the fabricator sent panels to another fabricator for processing through their pattern plating line. The agitation for the copper cells was provided by eductors, not air spargers. (Eductors move the plating solution in a more uniform way and eliminate air bubbles.)
After the panels were plated, inspectors noted that there was no evidence of pits or mouse bites along the resist/trace interface. However, there were still some random pits that indicated that residue on the base metal was inhibiting plating. This situation indicated two things: (1) air or gas bubbles at the fabricator were playing a role in the mouse bite defects and (2) there was a residue or contamination that led to the irregularly shaped pits (the subject of next month’s column).
Finally, another critical observation provided further insight to the mouse bite defect. Here one engineer noticed that plating solution was entering the filtration housing in two of the cells (Figure 2).
As this solution entered the housing, the air bubbles would become homogenized, so to speak, allowing the plating solution to become supersaturated with air bubbles. This situation allowed the bubbles to grow and eventually lodge onto the resist sidewall/trace interface(1). To prevent the air bubbles from entering the filtration housing, a system of baffles was installed. The baffles will prevent air bubbles from entering the filtration housing. Of course, a much wiser choice is to convert the agitation system to eductors.
Conclusion
The dominant cause of spherical or conical pits in copper plating is gas or air bubbles, which can be introduced into the plating solution from air spargers or through supersaturation of the plating solution with air bubbles. These bubbles grow on the copper traces at the photoresist sidewall, and thus inhibit plating. Some photoresists may contribute to air bubble (mouse bite) pits depending on the resist’s wetting characteristics, degree of hydrophobicity, and surface imperfections within the resist itself. In Part 3 of this case study, the development process will be reviewed and any possible parameters that may contribute to the pitting defects.
References
(1) “Reducing Copper Plating Pits in PWBs,” R. A. Olson, CircuiTree Magazine, August 1991, pg. 30.
Michael Carano is VP of technology and business development for RBP Chemical Technology. To reach Carano, or read past columns, click here.
More Columns from Trouble in Your Tank
Trouble in Your Tank: Metallizing Flexible Circuit Materials—Mitigating Deposit StressTrouble in Your Tank: Can You Drill the Perfect Hole?
Trouble in Your Tank: Yield Improvement and Reliability
Trouble in Your Tank: Causes of Plating Voids, Pre-electroless Copper
Trouble in Your Tank: Organic Addition Agents in Electrolytic Copper Plating
Trouble in Your Tank: Interconnect Defect—The Three Degrees of Separation
Trouble in Your Tank: Things You Can Do for Better Wet Process Control
Trouble in Your Tank: Processes to Support IC Substrates and Advanced Packaging, Part 5