-
-
News
News Highlights
- Books
Featured Books
- pcb007 Magazine
Latest Issues
Current IssueSales: From Pitch to PO
From the first cold call to finally receiving that first purchase order, the July PCB007 Magazine breaks down some critical parts of the sales stack. To up your sales game, read on!
The Hole Truth: Via Integrity in an HDI World
From the drilled hole to registration across multiple sequential lamination cycles, to the quality of your copper plating, via reliability in an HDI world is becoming an ever-greater challenge. This month we look at “The Hole Truth,” from creating the “perfect” via to how you can assure via quality and reliability, the first time, every time.
In Pursuit of Perfection: Defect Reduction
For bare PCB board fabrication, defect reduction is a critical aspect of a company's bottom line profitability. In this issue, we examine how imaging, etching, and plating processes can provide information and insight into reducing defects and increasing yields.
- Articles
- Columns
- Links
- Media kit
||| MENU - pcb007 Magazine
Estimated reading time: 13 minutes
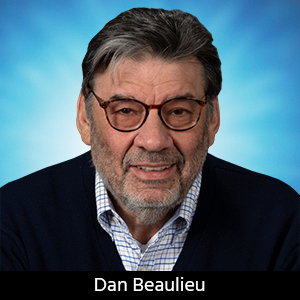
Conversations with...HSIO President Jim Rathburn
Rathburn: We were fortunate to have leading-edge customers who helped us define architectures needed for next-generation silicon. We also had a blank slate with an empty facility without legacy equipment that provided an opportunity to implement technology and capabilities beyond replicating currently available product. We did not want to be a “me too” company that produces what everyone else does. We also had the luxury of focus where the battle between production orders versus research and development of new technologies allowed us to take a different approach, while keeping in mind leveraging existing industry infrastructure. We worked with multiple partners that currently produce conventional circuits to provide opportunity for them to advance beyond commodity fabrication, with the support of material and plating suppliers to combine the best mix of design and production.
Beaulieu: This will be ideal for high-speed circuit fabrication.
Rathburn: Yes, the technology has proven to be a significant improvement over conventional fabrication with higher density and tighter control of the signal channel. One customer stated the approach is “an RF dream” and was able to test samples to validate performance.
Beaulieu: What are the plans for this technology?
Rathburn: We are not a circuit production shop. We are working with existing circuit fabrication companies that have the infrastructure to enable appropriate volume production availability in the flex circuit, rigid PCB, and package substrate markets. All of our high-speed socket and connector customers mate those products with a circuit of some kind, and can benefit from the high-performance circuit production. Many circuit customers may benefit from our socket and connector products by having the option to plug chips that are normally soldered to the circuit into a socket that has the same footprint as the package. In general, we plan to enable availability from multiple sources at the cost and volume to meet customer needs.
Beaulieu: So you're going to license it to existing board shops? How are you going to go about marketing this process?
Rathburn: Our current plan is to filter opportunities that are appropriate to the various production capabilities. We will license multiple circuit fabrication companies as needed to produce designs that we sell direct to end users, if possible bundled with connector and socket products that are appropriate to the application. We will also extend availability in a main stream fashion deployed to baseline circuit builds in the general market. An excellent example we are working on with a leading test equipment supplier is illustrated below where a silicon validation effort tuned for high-performance combines the base PCB, BGA sockets, and connector/cable interfaces to test equipment. The system level approach provides the best available signal performance from the silicon all the way to the test equipment.
Beaulieu: How about their customers? In what ways will they benefit from this?
Rathburn: The benefit to the supplier’s customers is they will have enabled production availability of very high speed, fine line and space multilayer rigid PCBs, flex, and package substrates with performance and density not typically available in conventional methods or domestic supply. Again, the adoption model is to replicate an existing design that may be 75 micron lines and spaces for validation, where the customer will see a significant improvement in performance compared to the existing design built with traditional pcb fabrication methods. Then we provide an instant path to 50 or 25 micron lines and spaces for example with higher routing density and potential layer count reduction. This adoption method makes it fairly easy to compare an existing design made with conventional construction to the new LCP construction. The follow-on issue once the performance is proven, is where can the customer buy production level circuits today with guaranteed supply in the future. Once the design rules are adopted, we want them to think of HSIO as the company of choice.
Beaulieu: So you will be teaching shops how to implement the process, correct?
Page 3 of 4
More Columns from It's Only Common Sense
It’s Only Common Sense: How to Win Back Lost CustomersIt’s Only Common Sense: Knowing When to Walk Away
It’s Only Common Sense: Customer Service Is Sales in Disguise
It’s Only Common Sense: Your Guide to Better Time Management
It’s Only Common Sense: Selling to Today's Generation of Buyers
It’s Only Common Sense: Why Sales Teams Fail (and How to Fix Them)
It’s Only Common Sense: Selling Without Selling
It’s Only Common Sense: The Power of Storytelling in Sales