-
- News
- Books
Featured Books
- pcb007 Magazine
Latest Issues
Current IssueEngineering Economics
The real cost to manufacture a PCB encompasses everything that goes into making the product: the materials and other value-added supplies, machine and personnel costs, and most importantly, your quality. A hard look at real costs seems wholly appropriate.
Alternate Metallization Processes
Traditional electroless copper and electroless copper immersion gold have been primary PCB plating methods for decades. But alternative plating metals and processes have been introduced over the past few years as miniaturization and advanced packaging continue to develop.
Technology Roadmaps
In this issue of PCB007 Magazine, we discuss technology roadmaps and what they mean for our businesses, providing context to the all-important question: What is my company’s technology roadmap?
- Articles
- Columns
Search Console
- Links
- Media kit
||| MENU - pcb007 Magazine
Estimated reading time: 10 minutes
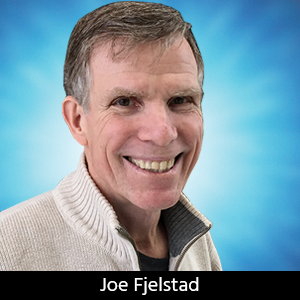
Stretching the Limits of Flex
Those steeped in flexible circuit design and manufacture for any length of time fully appreciate the long list of benefits that only flexible circuits can offer. Some of the most fundamental benefits of flex circuit technology have been exploited since the earliest days of the technology.
Chief among the basic benefits is probably the flexible circuits’ ability to provide a means and medium for reliably and cost-effectively manufacturing large numbers of circuits, each circuit being designed to make significant numbers of interconnections between electronic elements which are displaced from one another in three-dimensional space in a cost-effective manner, whether in static or dynamic applications. Other than wireless interconnection solutions, nothing else comes close. Admittedly, for the hobbyist some point-to-point wires are likely a better choice, but other than that, the field of prospective solutions that can provide such capability is extremely limited, including those of the wireless type.
Many of the other benefits of flexible circuits (reduced weight, low profile, etc.) can often be accomplished by judicious use of thin rigid materials, but there is an emerging branch of flexible circuit technology which shows promise as a means to stretch both figuratively and literally the limits of what flexible circuits can do. This evolving area involves not just flexing but stretching the circuit to provide a whole new range of capability and opportunity in the manufacture of interconnections.
Stretchable Circuits: Background
The desire to alternately increase and decrease the length of a flexible circuit is not a new idea in and of itself. Traditional flex circuit technology has been adapted to the basic task in a number of ways over the years. Perhaps the most obvious and visible are adaptations of flexible circuit technology to the interconnection of printheads on printers of every stripe. In such cases the flex circuit is not actually stretched but rolled back and forth over itself allowing the print had to move back and forth. Another way of accomplishing the same objective is to fold the circuit in accordion-like fashion. This allows the user to alternately stretch and compress the circuit over a prescribed distance. This "out-of-plane" solution was in fact adapted in the manufacture of miniature stretchable circuits by researchers at the University of Illinois where metal circuits interconnecting small pieces of silicon on a resilient polymer base were pre-buckled on the surface, thus allowing them to flatten as the circuit is stretched. Though clearly creative, the solution is rather specialized and thus more interest has been expressed and explored in finding solutions where the interconnections are in plane.
Stretching Conductors… Really? It's All in the Design
While there has been a significant effort in Europe over the last 5+ years to develop and exploit stretchable circuit technology, the earliest description of a stretchable circuit on an elastomeric base in patent form is one first filed in April of 2004, which was issued to researchers at Lawrence Livermore National Laboratory. The patent describes a stretchable electronic circuit having either sawtooth or sinusoidal circuit traces on an elastomeric base material (see Figure 1).
Figure 1. Stretchable circuit concept enabled by creating sawtooth metal circuit pattern diclosed in US patent 7,337,012.
In such constructions, the stretching of the circuit is enabled by adding additional circuit length in the meander pattern. Thus, when the base elastomer material is stretched, there is a sort of pseudo-elasticity in the metal circuits, owing to the fact that metals – aside from a few unusual alloys such as nickel titanium alloys – have almost no elasticity.
However because the elastomeric base material is much stronger than the thin metal circuits, it can mechanically overwhelm the circuits, allowing them to return to their approximate shape when force is applied to stretch the circuit are released. Thus in the process of stretching the circuit, some plastic deformation of the circuits can be expected and because of this, on repeated cycles, the circuits eventually begin to fail due to cracking of the metals. As a result, other researchers have made improvements to the basic concept by modifying the circuit traces so that they can be stretched to greater lengths and/or greater numbers of stretching cycles before the circuit eventually fails. The improved design approaches are in shown in Figure 2.
Figure 2. Improved conductor design for a stretchable circuit (left insert). On the right are shown finite element models of original (top) and improved (bottom) approaches to making in plane stretchable conductors. Photo courtesy of Technical University Berlin. FEMs courtesy of IMEC.
While design of the circuit pattern for the metal foil versions of stretchable circuits is clearly important, a great deal of effort has been put into the design and development of new composite materials that are both conductive and resiliently stretchable. Most of these solutions are mixtures of some conductive material such as metal mixed with a stretchable polymer. However, getting the material mix right is challenging.
Silver is the most conductive of commonly available metals and it has the added advantage that its various natural oxides are also conductive making is a natural choice. Moreover, with the advances in nanotechnology, silver powers are closing in on native silver in terms of conductivity. Moldable mixtures of silver and polymers/elastomers including NBR compounds filled with silver flakes or silver coated copper, EPDM (ethylene propylene diene monomer rubber) compounds similarly filled and various liquid elastomers also metal filled have been explored. The conductivity of these materials is of course lower than metals, but the resilience is better and they can be stretched linearly without the meander pattern required for metal which saves space. However, if overstretched, the circuit will fracture. One of the big challenges with this type of solutions is that they tend not to be solderable and thus must be post-processed to make them so (e.g., plate directly with a solderable finish).
Stretchable materials: What works?
Many different materials can be stretched to some degree, including metals. The amount they can be stretched varies. Some metals such as copper can be stretched up to 30% or more. In the parlance of metallurgy this is called plastic deformation and the deformation is permanent. In contrast resilience is a fundamental properly of rubbers and elastomers. Resilience is the ability of a material to stretch and recover fully when relaxed is a basic requirement for any base material to be used in the manufacture of a stretchable circuit.
To provide a little framework for this discussion, an elastomer is a polymer that has the property of elasticity, which is generally characterized by the material having a fairly low Young’s modulus, greater elongation at break and a higher Poisson’s ratio compared to other materials. The list of prospective candidate materials is thus, in general, limited by such rubberlike properties. Following is a brief look at some of the materials that have been used or investigated for use in the manufacture of stretchable circuits in recent years.
First is nitrile rubber, or more specifically acrylonitrile-butadiene rubber also called NBR or Buna N. This rubbery material is the primary workhorse of the industrial and automotive rubber products industries. The material has good elastic properties with lower acrylonitrile content, a good working temperature range (–40C to +125C) and resistance to oil, which explains its wide use in automotive applications. It is also used in non-latex glove applications. Sheet stock is available at thickness of 0.5mm and the material is available in powdered form, giving rise to the possibility of transfer molding circuits the material in a near net shape to reduce the stretching requirement for extreme stretch applications.
Next on the list is silicone rubber, which is widely used in many of today's products due to its many desirable properties. The elastomer can also be filled with other materials to change its properties. For example, conductive materials can be added to improve thermal or electrical conductivity for heat removal or electrical shielding needs respectively. Silicones maintain many of their properties over a wide range of conductions. High thermal resistance is one of its more attractive properties but it also has ability to retain flexibility at lower temperatures. Thin sheet materials are available in thicknesses ranging from 0.075mm to 1.0mm, which is a range suited to stretchable circuits.
Thermoplastic polyurethanes (TPU) are another candidate base material for stretchable circuits. Even in their thinnest form, the films are extremely tear resistant and highly stretchable. TPU materials have a number of properties that are attractive to some product investigators and developers including: abrasion resistance, good low-temperature performance, good mechanical properties combined with a high elasticity, good shear strength and high transparency. The list of properties along with relatively low cost has propelled their use. TPU film is readily available in thicknesses from 0.1mm to 0.8mm
The last material in this brief overview is spun, nonwoven polyurethane. Anyone who wears clothing will have noticed at some point in their lives that most woven fabrics have some degree of stretchability. The amount of material can stretch is predicated on the tightness of the strands in the fibers and the weave of the cloth. Non-woven materials are used alongside woven ones. Non-woven fibers offer some additional stretchability owing to the fact that the fibers are not as ordered or tightly bound. If the material used for the fibers themselves has some degree of elasticity, the fabric can be reasonably stretchable. In this regard, fabrics made of non-woven polyurethane have become materials of interest to some investigators. There use has been explored in one specific area where circuit were pattern plated directly to the surface of the material as can be seen in Figure 3.
Figure 3. An example of a copper metal pattern plated to a non-woven polyurethane cloth. The conductivity on when stretched relies on the copper plated fibers maintaining contact as connections are broken and remade in myriad places during stretching. Courtesy of Technical University Berlin and QPI.
Beyond the short list of resiliently stretchable materials, there are likely to be discovered, now and in the future, many applications where full recovery of the circuit to its original dimensions is not required. In such cases, low-modulus materials which also have low tensile strength could be employed to create circuits which stretch to some predetermined length and will not be predisposed to recover to their original dimension. While the application of heat serves to make nearly any material softer, more pliable and thus stretchable it would likely be preferable that the material chosen be able to stretch at room temperature without damage.
Market Opportunities for Stretchable Circuits
As a still nascent technology, stretchable circuit technology is being investigated for use in a number of applications in a few different markets. To date, most of the interest seems to be centered on products either related to fashion or to health and fitness. In the former case, stretchable circuit technology is being paired with LED technology to create fanciful clothing for the more trendy people in our midst. The latter areas of interest of health and fitness seem to be more compelling to a greater number of researchers, however.
In the same way that mechanical engineers and medical technologists combined their skills to create the field of biomechanics to improve the lives of countless individuals who might have been otherwise condemned to a life of pain and limited mobility due to crippling joint disease, electronic and medical technologists are joining forces allowing us to enter a new era of bioelectronics. It is here that stretchable circuit technology has captured the fancy of many researchers both in academia and in industry. The list of applications is limited at present but is growing.
Examples of products include various sorts of pliable monitors which can be strapped to our heads, arms, chests, legs, or feet to monitor any of a number of different conditions including temperature, breathing rate, blood pressure, heart rate, blood oxygen content and the like, allowing remote and nonintrusive monitoring of an individual's vital signs for either medical or physical training reasons. Doubtless these early applications will serve as a mental springboard for coming generations of product designers and developers will find value in stretchable interconnections in some of their future designs.
In summary, stretchable circuit technology is an emerging branch of the flexible circuit family tree and appears poised to bestow its own unique brand of fruit to those in the industry hungering for novel solutions for the next product design.
Those interested in reading more on the topic of stretchable circuits are invited to download a copy of the Fourth Edition of Flexible Circuit Technology available at www.flexiblecircuittechnology.com.
Verdant Electronics Founder and President Joseph (Joe) Fjelstad is a four-decade veteran of the electronics industry and an international authority and innovator in the field of electronic interconnection and packaging technologies. Fjelstad has more than 250 U.S. and international patents issued or pending and is the author of Flexible Circuit Technology.
More Columns from Flexible Thinking
Flexible Thinking: Rules of Thumb—A Word to the WiseFlexible Thinking: Musings on High Density Interconnections
Flexible Thinking: Integrated Passive Devices—Design Solutions With Many Benefits
Flexible Thinking: Mechatronics in a Flex World
Flexible Thinking: PCB Designers Still Wanted
Flexible Thinking: Embedded Design—A Term With Multiple Meanings
Flexible Thinking: What Matters When Designing Next-generation Products?
Flexible Thinking: The Simplest Way Is the Best Way