-
- News
- Books
Featured Books
- pcb007 Magazine
Latest Issues
Current IssueInventing the Future with SEL
Two years after launching its state-of-the-art PCB facility, SEL shares lessons in vision, execution, and innovation, plus insights from industry icons and technology leaders shaping the future of PCB fabrication.
Sales: From Pitch to PO
From the first cold call to finally receiving that first purchase order, the July PCB007 Magazine breaks down some critical parts of the sales stack. To up your sales game, read on!
The Hole Truth: Via Integrity in an HDI World
From the drilled hole to registration across multiple sequential lamination cycles, to the quality of your copper plating, via reliability in an HDI world is becoming an ever-greater challenge. This month we look at “The Hole Truth,” from creating the “perfect” via to how you can assure via quality and reliability, the first time, every time.
- Articles
- Columns
- Links
- Media kit
||| MENU - pcb007 Magazine
Estimated reading time: 5 minutes
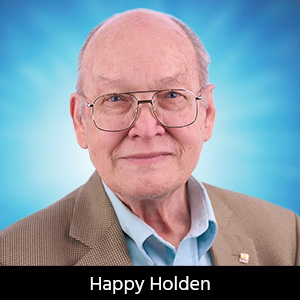
Contact Columnist Form
Happy’s Tech Talk #14: Palladium as a Final Finish
Introduction
The late Karl Dietz never wrote on the topic of palladium as a final finish, but he did write about gold plating as a final finish and had an excellent discussion on copper plating1–5. But palladium now has a renaissance as a final finish. It was very popular in the 1970s, as the only other final finishes were tin-lead reflow, nickel-gold, OSP, or immersion tin. Palladium was very popular with the automotive industry then and a major supplier of boards was Photocircuits of Glenn Cove, New York.
Final Finishes
As semiconductors (IC transistors) become smaller and have faster rise times, the signal is more sensitive to any ferromagnetic metal in its path. So many alternatives have been developed to remove nickel as a barrier metal on copper for final finishes, especially in ENIG to improve insertion loss.
Everyone has their favorites. The simplest and cheapest is OSP, followed by lead-free HASL, but they have their pros and cons. Immersion silver is quite popular in North America and immersion tin is popular in Europe. ENIG has been a long-time standard, but the nickel now comes into play because it does not dissolve in the solder as the others do. Enter palladium to replace the nickel as a barrier metal. The new finishes are Pd/Ag, Ni/Pd, Ni/Pd/Au, Pd/Au, and Au/Pd/Au—all developed to replace the ENIG for solderability, shelf-life, and wire bonding.
During development of ENEPIG, it was recognized that the addition of a palladium (Pd) layer between the nickel and gold enabled both gold and aluminum wire bonding operations, in addition to the normal soldering application. In addition, the Pd layer was found to limit the corrosion of the nickel by an overly aggressive immersion gold process. An electrolytic nickel/gold finish was typically the process of record (POR) for such wire bonding needs. ENEP investigations into the ENEP process, which is essentially the ENEPIG process without the immersion gold step, actually followed the introduction of ENEPIG to the market. In comparison to ENEPIG, ENEP appears to offer a surface finish with benefits like stronger solder joint reliability under Pb-free conditions, lower cost (by elimination of gold) and, as recently investigated, Cu wire bonding capability.
Palladium Finish Used in Automotive
Early in the 2010s, palladium reemerged as a final finish. Electronic chemicals company OMG introduced its new palladium finish, PallaGuard. (OMG is now part of MacDermid.) Some of its features were:
- Eliminates black pad
- A single coating on copper
- Excellent silver replacement
- Short process time of 15 minutes
- Excellent shelf life
- Can be used to replace carbon switches
- Excellent replacement for harsh environments
- High gold bond shear test results
Properties
The properties of palladium, which was discovered in 1803 by the English chemist William Hyde Wollaston, are many:
- Pure palladium deposit, atomic number 46
- Melting point is 2,830.82°F (1,554.90°C)
- Palladium deposit with 2-3% phosphorus (Pd-P)
- Pure palladium 50% softer than Pd-P (Figure 2)
- Specific gravity is 11.9
- Resistivity, microohm-cm at 0°C: 10.7
- Electrical conductivity, percent IACS: 16
- Thermal conductivity, CGS units: 0.17
- Deposit thickness of 2–5 microinches for soldering and 5–15 microinches for wire bonding
- Pd has a hardness in the range 300 to 400 V.P.N. and is relatively free from internal stress, so that the plate does not suffer from curling and peeling troubles
- When solder joint strength is critical, or gold wire bonding is required
- Pure Pd has a better wetting angle and reflow spread than Pd-P (Fig. 3)
New Applications of Palladium
For electronic assembly reliability especially for harsh environments, palladium has many advantages over nickel, except cost. For improved wire bonding reliability, a minimum of 5 microinches of electroless palladium over nickel or copper will eliminate any 0.7 mil gold wire surface failures and provide over 6 grams of pull strength.
Black Pad—Nickel Corrosion
The use of an electroless palladium (EP) layer between the electroless nickel and the immersion gold will eliminate any nickel corrosion (black pad) and the thicker the Pd, the less immersion gold is deposited, thus reducing costs. The explanation is that the gold ions, at the lower EP thickness, had access to the underlying nickel and deposited at an accelerated rate, producing nickel corrosion. Lacking access to the underlying nickel, the immersion gold (IG) reaction with phos-palladium becomes self-limiting to 2 µin (0.05 µm).
Summary
The resurgence of palladium as a final finish or a barrier over copper or nickel has solved a number of problems. This is especially useful when the PCB may operate in a hazardous, corrosive, or extreme environment, such as with vehicles.
When compared to its predecessors—ENIG and electrolytic Ni/Au—ENEPIG has been shown to offer stronger solder interconnects and wire bonds. Pull and shear forces needed for failures on ENEPIG were a minimum of 5% higher than ENIG and Ni/Au when SAC3xx solders were used. Furthermore, the failure modes in the ENEPIG/SAC3xx solder interconnects were primarily ductile in the bulk, while failure modes in ENIG/SAC3xx and Ni/Au/SAC3xx were primarily brittle in the IMC, even after preconditioning steps were taken. Ductile failure in the bulk implies that ENEPIG has better solderability with SAC3xx solders than ENIG and Ni/Au7. The use of electroless palladium is characterized in Figure 4.
References
- Tech Talk #54: Organic Additives in Copper Plating Baths (Part 1), by Karl Dietz, CircuiTree Magazine, February 2000.
- Tech Talk #55, Organic Additives in Copper Plating Baths (Part 2), by Karl Dietz, CircuiTree Magazine, March 2000.
- Tech Talk #145, Staying out of Trouble in Gold Electro-plating, by Karl Dietz, CircuiTree Magazine, Oct. 2007.
- Tech Talk #154, Advances in Copper plating (Part A), by Karl Dietz, CircuiTree Magazine, July 2008.
- Tech Talk #155, Advances in Copper plating (Part B), by Karl Dietz, CircuiTree Magazine, August 2008.
- “Benefits of pure palladium for ENEP and ENEPIG surface finishes,” by Mustafa Ozkok, ESTC Conference, October 2010.
- “Review of Capabilities of the ENEPIG Surface Finish,” by M. Ratzker, M. Pecht, G. Milad, Journal of Electronic Materials, Vol. 43, No. 11, 2014.
This column originally appeared in the November 2022 issue of PCB007 Magazine.
Happy Holden has worked in printed circuit technology since 1970 with Hewlett-Packard,?NanYa?Westwood, Merix, Foxconn, and Gentex. He is currently a contributing technical editor with I-Connect007, and the author?of?Automation and Advanced Procedures in PCB Fabrication, and?24 Essential Skills for Engineers.
More Columns from Happy’s Tech Talk
Happy’s Tech Talk #42: Applying Density Equations to UHDI DesignHappy’s Tech Talk #41: Sustainability and Circularity for Electronics Manufacturing
Happy’s Tech Talk #40: Factors in PTH Reliability—Hole Voids
Happy’s Tech Talk #39: PCBs Replace Motor Windings
Happy’s Tech Talk #38: Novel Metallization for UHDI
Happy’s Tech Talk #37: New Ultra HDI Materials
Happy’s Tech Talk #36: The LEGO Principle of Optical Assembly
Happy’s Tech Talk #35: Yields March to Design Rules