-
- News
- Books
Featured Books
- pcb007 Magazine
Latest Issues
Current IssueVoices of the Industry
We take the pulse of the PCB industry by sharing insights from leading fabricators and suppliers in this month's issue. We've gathered their thoughts on the new U.S. administration, spending, the war in Ukraine, and their most pressing needs. It’s an eye-opening and enlightening look behind the curtain.
The Essential Guide to Surface Finishes
We go back to basics this month with a recount of a little history, and look forward to addressing the many challenges that high density, high frequency, adhesion, SI, and corrosion concerns for harsh environments bring to the fore. We compare and contrast surface finishes by type and application, take a hard look at the many iterations of gold plating, and address palladium as a surface finish.
It's Show Time!
In this month’s issue of PCB007 Magazine we reimagine the possibilities featuring stories all about IPC APEX EXPO 2025—covering what to look forward to, and what you don’t want to miss.
- Articles
- Columns
Search Console
- Links
- Media kit
||| MENU - pcb007 Magazine
Flex Factory in Sorocaba, Brazil Admitted into World Economic Forum Global Lighthouse Network
October 12, 2022 | FlexEstimated reading time: 2 minutes
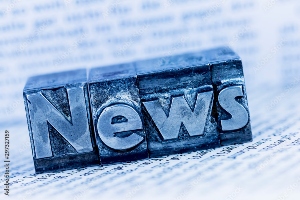
Flex announced its factory site in Sorocaba, Brazil has been admitted into the World Economic Forum’s Global Lighthouse Network (GLN). This recognition is a result of the Fourth Industrial Revolution (4IR) technology adoption journey this Flex factory embarked on in 2017 that put equal emphasis on sustainability, people and economic growth. The GLN is a community of manufacturers that are world leaders in the adoption and integration of cutting-edge 4IR technologies to maximize efficiency and competitiveness at scale, transform business models and protect the environment. Flex CEO Revathi Advaithi will participate as a guest expert/speaker on a virtual panel hosted by the World Economic Forum Global Lighthouse Network on October 13 at 14:00 CEST titled, “Unlocking Sustainable and Human Centric Operations Using 4IR Technologies.”
The site in Sorocaba is the second Flex factory to be admitted into the GLN. Through the rigorous admission process, the company demonstrated how it has deployed 4IR initiatives along the end-to-end value chain to increase agility and operational efficiencies. The site has deeply embedded sustainability into its operations with a circular economy ecosystem. People remain a focus, improving engagement by upskilling employees and increasing team member well-being through innovative digital health and safety measures. It has also increased customer satisfaction by providing improved transparency and quality.
“The Flex factory site in Sorocaba, Brazil is leading the way for the future of manufacturing by leveraging 4IR technologies to achieve not only efficiency and quality, but also prioritizing sustainability and employee care, which are critical elements for Global Lighthouse factories,” said Francisco Betti, Head of Shaping the Advanced Manufacturing and Production Platform, World Economic Forum. “Being part of the Lighthouse network, manufacturers can collaborate and share insights with like-minded peers, to unlock new levels of sustainability in their operations and to lead towards a cleaner future.”
“Flex is focused on delivering manufacturing excellence for its customers and the site in Sorocaba is a shining example. We are honored to be recognized as one of the first Global Lighthouse Network factories in Brazil,” said Hooi Tan, President, Global Operations and Supply Chain, Flex. “We look forward to our continued participation in the World Economic Forum’s Global Lighthouse Network, sharing our experiences and best practices in developing sustainable, advanced manufacturing capabilities at scale and collaborating with others in the industry to proliferate the adoption of Industry 4.0 technologies for advanced manufacturing.”
The nomination of the Sorocaba site showcased the following innovation areas:
- Implemented a real time, IIoT-enabled digital factory performance management system connected to 44 production lines. This provides real-time data and transparency, resulting in material loss reduction by 81% and an overall equipment effectiveness (OEE) increase of 23%.
- Developed a circular economy ecosystem, including reverse logistics of electronic waste leveraging IoT and cloud for real time tracking, resulting in a 94% reduction of material waste and a 38% reduction of plastic material costs. This reduced the need for resources equivalent to 44K carbon credits accredited by the Canadian Standard Association (CSA).
- Created an end-to-end ergonomics digital thread with real time monitoring of operators who are alerted when a job rotation or workstation ergonomics improvement needs to be made to ensure employee health and safety.
- Upskilled over 200 employees on developing and using low and no code digital tools and implemented Robotic Process Automation (RPA) solutions. This eliminated repetitive tasks for humans, resulting in a 38% reduction in nonvalue added work, and an increase of both employee and customer satisfaction.
- Implemented an advanced real time supply chain solution to accelerate product flow, creating on-demand transparency and enabling supply chain resiliency.
Suggested Items
Elephantech: For a Greener Tomorrow
04/16/2025 | Marcy LaRont, PCB007 MagazineNobuhiko Okamoto is the global sales and marketing manager for Elephantech Inc., a Japanese startup with a vision to make electronics more sustainable. The company is developing a metal inkjet technology that can print directly on the substrate and then give it a copper thickness by plating. In this interview, he discusses this novel technology's environmental advantages, as well as its potential benefits for the PCB manufacturing and semiconductor packaging segments.
Real Time With... IPC APEX EXPO 2025: Best Student Technical Paper Winner—Attila Rektor
04/10/2025 | Marcy LaRont, I-Connect007Attila Rektor, a Ph.D student from Boise State, won the best technical paper award at IPC APEX EXPO 2025. His paper explores enhancing the conductivity of laser-induced graphene for flexible circuits. The research, funded by SAIC, involved modulating surface energy to enable effective copper plating. This breakthrough has potential applications in flexible printed circuit boards, sensing, and biomedical devices.
Real Time with... IPC APEX EXPO 2025: Advancements for Flexible Circuit Technologies
04/11/2025 | Real Time with...IPC APEX EXPOMark Finstad and Chris Clark from Flexible Circuit Technologies discuss their new marketing campaign for catheter circuits, featuring larger formats and advanced specifications. They explain the development of in-house materials for high-density circuits, enhancing cost competitiveness. They highlight the opening of a new facility in China for advanced assembly services, along with focused training sessions to fill industry education gaps and promote early customer engagement for better project outcomes.
Adaptsys, APP Systems Services Announce Strategic Partnership in Singapore
04/08/2025 | AdaptsysAdaptsys has formed a strategic partnership with APP System Services, bringing our innovative Re-flex II inline carrier tape forming technology to customers in Singapore.
CEE PCB Appoints Markus Voeltz to Business Development Director Europe
04/02/2025 | CEE PCBCEE PCB, a leading manufacturer of printed circuit boards (PCBs) and flexible printed circuits (FPCs) with 3 production facilities in China, is expanding its presence in Europe and began providing local support in March 2025. With 25 years of experience in the industry, the company is enhancing its commitment to European customers by providing more direct collaboration for technical inquiries and advice.