-
- News
- Books
Featured Books
- pcb007 Magazine
Latest Issues
Current IssueInventing the Future with SEL
Two years after launching its state-of-the-art PCB facility, SEL shares lessons in vision, execution, and innovation, plus insights from industry icons and technology leaders shaping the future of PCB fabrication.
Sales: From Pitch to PO
From the first cold call to finally receiving that first purchase order, the July PCB007 Magazine breaks down some critical parts of the sales stack. To up your sales game, read on!
The Hole Truth: Via Integrity in an HDI World
From the drilled hole to registration across multiple sequential lamination cycles, to the quality of your copper plating, via reliability in an HDI world is becoming an ever-greater challenge. This month we look at “The Hole Truth,” from creating the “perfect” via to how you can assure via quality and reliability, the first time, every time.
- Articles
- Columns
- Links
- Media kit
||| MENU - pcb007 Magazine
Estimated reading time: 4 minutes
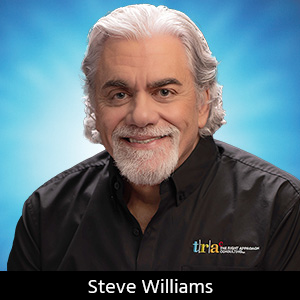
Manufacturing Advantage: Japan! Where is the Love for Kanban and Lot Size of One in the U.S.?
The Founding Fathers
Companies like Toyota are often touted (with good reason) as the gold standard for manufacturing. Toyota’s TPS (Toyota Production System) has been highly publicized and has gained increasing acceptance in American manufacturing operations over the last decade or so. What has not been highly publicized is the fact that many of these concepts originated in America, and quality pioneers like W. Edwards Deming had to take their show on the road to Japan only after being rejected by the leaders of American industry. The contributions of such legends as Dr. Deming, Dr. Juran, Philip Crosby, Dr. Ishikawa, Dr. Shewhart, and Shigeo Shingo had such an impact on the world that these men truly are the founding fathers of modern manufacturing. While many of these early techniques, models and methodologies have slowly been embraced in the U.S. recently, two major concepts that have propelled Japan to manufacturing dominance have struggled for acceptance: Lot Size of One and the Kanban Pull System.
Lot Size of One
The elusive Lot Size of One is a Lean strategy, and while a lot size of one may not be feasible for many organizations and industries, the practical application of this technique is that small lot sizes are better than large ones. Most U.S. manufacturing managers just will not buy into this concept, preferring to hold onto the bigger is better mentality in the face of voluminous data suggesting the opposite to be true. We tend to believe that the economies of scale theory that has been ingrained in all of us will always be achieved with large lot sizes.
A detailed look at most manufacturing processes normally reveals that most lot sizes are too large for any department to efficiently process without breaking into smaller sub-lots. Lots get broken up and separated, which creates many issues including traceability, duplicate or missing documentation, scrap and rework accountability and production scheduling difficulties. Small lot sizes reduce variability in the production system and also smooth out the overall production process. Small lots enhance quality, simplify scheduling, reduce inventory, encourage continuous improvement and enable the Kanban Pull System. While a Lot Size of One may seem impossible, integrated supply-chain programs that hold a small amount of finished goods inventory based on actual consumption patterns can make this a reality.
Kanban Pull System
A Kanban Pull System is another Lean strategy and one that is functionally diametrically opposed to the traditional methodology embraced here in the U.S. American manufacturing has long embraced the traditional push system, which uses forecasts to drive material and product through a production system regardless of whether the next department needs, or is ready for, the next lot of product. This overdrive is regardless of internal demand, and often, customer demand as well. On the other hand, a Kanban Pull System controls and balances the flow of product in a production process by replacing only what has been consumed. This system uses customer order-driven production schedules that are based on actual demand and consumption rather than forecasting.
Some of the benefits of implementing a Kanban Pull System include an overall reduction in inventory, reduction in WIP (work in process), reduced cycle time, increased customer satisfaction, and improved cash flow.
There are essentially two different types of pull systems: sequential pull and replenishment (or supermarket) pull. In sequential pull, the downstream customer pulls parts from the upstream process in a sequence. Sequential pull limits the amount of inventory between the two processes. In replenishment pull, the downstream customer pulls from a small inventory (supermarket) according to what is needed based on customer demand. The supermarket is then replenished based on actual consumption.
The word Kanban literally translates as “visual card,” which represents any visual signal method used to show the need for parts or products to be moved or produced. The Kanban concept is a requirement planning technique developed by Toyota as a part of the JIT (just-in-time) production strategy. While the signal itself can take many different forms, the actual signal is at the heart of any pull system. There are many different types of Kanban signals, including physical cards, electronic, min/max bins, and as many hybrid variations as the imagination can create.
All In
While great strides have been made here in America toward embracing Lean strategies, we really do need to be all in to truly begin to catch our competition in Japan and other countries that have a 50-year head start on us. The Lot Size of One and Kanban Pull System are two powerful concepts to move us down this path.
Editor's Note: This article originally appeared in the November 2012 issue of The PCB Magazine.
Steven Williams is a 35-year veteran in the electronics industry and an authority on manufacturing and management. He is currently the commodity manager for a large global EMS provider, a distinguished faculty member at several universities and author of the book Survival Is Not Mandatory: 10 Things Every CEO Should Know About Lean.
More Columns from The Right Approach
The Right Approach: ‘Twas the Night Before Christmas (Harley-style)The Right Approach: I Hear the Train A Comin'
The Right Approach: Culture Change is Key to a QMS
The Right Approach: Leadership 101—Be a Heretic, Not a Sheep
The Right Approach: Leadership 101—The Law of Legacy
The Right Approach: Leadership 101: The Law of Explosive Growth
The Right Approach: Leadership 101—The Law of Timing
The Right Approach: The Law of Sacrifice