-
- News
- Books
Featured Books
- pcb007 Magazine
Latest Issues
Current IssueInventing the Future with SEL
Two years after launching its state-of-the-art PCB facility, SEL shares lessons in vision, execution, and innovation, plus insights from industry icons and technology leaders shaping the future of PCB fabrication.
Sales: From Pitch to PO
From the first cold call to finally receiving that first purchase order, the July PCB007 Magazine breaks down some critical parts of the sales stack. To up your sales game, read on!
The Hole Truth: Via Integrity in an HDI World
From the drilled hole to registration across multiple sequential lamination cycles, to the quality of your copper plating, via reliability in an HDI world is becoming an ever-greater challenge. This month we look at “The Hole Truth,” from creating the “perfect” via to how you can assure via quality and reliability, the first time, every time.
- Articles
- Columns
- Links
- Media kit
||| MENU - pcb007 Magazine
Estimated reading time: 5 minutes
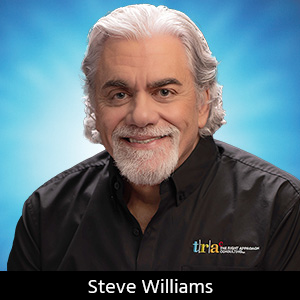
Will 'Old' PCB Technology Save American Manufacturing?
Editor's Note: This article originally appeared in the September 2012 issue of The PCB Magazine.
Full Additive PCB Fabrication
Many of us pre-1980s technology, old-school board guys remember actually running the additive PCB process back in the day, well before the subtractive process became the preferred methodology. The additive process was quite simple and had far fewer process steps than the complicated travelers seen in today’s PCB shops. There was neither a need for copper-clad raw laminate, nor current selective electroplating technologies. A negative image was defined on a resin substrate, and metal was selectively added, or built-up, to form the circuitry and interconnects.
Old is New Again
An article in the business section of my local newspaper caught my eye the other day. The piece focused on a Pennsylvania company called ExOne that was in the 3D printing business. My first thought was 3D labels or PoP (point-of-purchase) displays, but what really grabbed my attention was that this company was 3D printing large, stainless steel boat propellers! There has long been talk of utilizing this technology for PCB manufacturing, but it has never seemed to get out of the science-project phase.
If you walk into any sheet metal fabrication, machining, or die cast operation, you will be immersed in the raw environment of the trade: clanging machines, ground-shaking punch press thumping, grinding metal, and weld spark fireworks. You will also be treated to the earthy smell of oil, grease, molten metal, and let’s not forget sweat, created by hard, physical labor. Contrast that to the atmosphere in a 3D printing operation, which could easily be compared to a quiet, unrushed office environment.
America as an LCC
What a concept: America as a low-cost country! The biggest driver of low-cost countries is labor cost; and, a 3D operation requires only a few talented employees to run dozens of machines and hundreds of products. The equipment runs virtually on autopilot; a single person can manage a shop full of machines, literally, with the most important task being to keep each machine fully stocked with raw material.
3D printing is definitely a low-cost business model, needing only several employees and dozens of machines to match the production of traditional manufacturing operations employing hundred, if not thousands, of managers, engineers, operators and staff. 3D printing has been in limited use since the '80s in a variety of industries, but not in any widespread production environment. The demand for this technology is there; according to Terry Wohlers, president of the consulting firm Wohlers Associates, part production made up nearly a quarter of the $1.7 billion in sales of the 3D printing industry, and he is projecting this to rise to 80% of the industry’s forecasted $6.9 billion in revenue by 2019.
The Process
The machines are very similar in look and operation to document printers, and run automatically. A single operator can design the program for new parts, load and unload the machines, and occasionally add the raw material powder that feeds the machines. Using a metal part as an example, a computer-aided design, programmed into multiple cross-sections, is entered into the machine’s computer telling the printer precisely how to shape the part.
A roller puts down a layer of gray metal powder. A cartridge then quietly glides across the surface, much like an old dot matrix print head, depositing a chemical to bind together certain chemical particles, and forms multiple images of the part. It looks like a rough sketch of the part, but it’s actually a 1/4000-inch layer of it. The completed layer drops down and a new gray layer of powder is applied. 3D printers have evolved to make a variety of objects using a laser or extruder that travel along an X, Y, and Z path to build-up an object in three dimensions, layer by layer, sometimes only microns thick at a time, which can result in hundreds or thousands of layers to make a finished part. Other 3D printers follow different processes, depending on the material. For example, many plastic parts are formed by squirting successive layers of melted plastic through a precision nozzle.
Figure 1: 3D printed metal gear.
Think of the Possibilities
Self-sustaining equipment
The ability to generate replacement parts before they are needed. 3D printing is truly a lean process, since exactly the amount of raw material is being consumed that is required. There is no waste!
Bioprinting
Researchers at Wake Forest University developed this technology for U.S. troops serving in Afghanistan, which uses 3D technology to print new skin directly onto a burn wound. Within an hour, a precise topographical 3D image of a burn victim’s wound is scanned, and then the 3D printer prints new layers of cells directly onto the wound using the patient’s actual skin as the raw material. As far-fetched as it sounds, this technology could lead to the holy grail of medical science: the production of organs and body parts.
Transportation
What if a large ocean liner, train, or airplane had a 3D printer on board that could make replacement parts on the spot and avoid breakdowns, or more importantly, catastrophes? A vehicle’s computers may one day contain a database of 3D CAD images of every part from nuts to bolts to engine parts. If any of these should fail, a 3D printer could be able to manufacture immediate, OEM specification replacement parts on the spot.
Cloud Manufacturing
3D printing would allow the ultimate virtual manufacturing scenario: By investing in a single machine and a small amount of raw material, one could become a manufacturer of a diverse portfolio of products virtually (pun intended) overnight. With very little capital expense, one could receive CAD data electronically in the morning, 3D print almost any form of prototype parts overnight, and ship the order the next day.
Reshoring?
This minimalist factory exemplifies the latest chapter of the industrial revolution, one that could make U.S. manufacturing more competitive globally and bring more jobs back to the United States (reshoring). Will this technology really save American manufacturing? I don’t know, but creative and industrious Americans have always been the hallmark of our nation, and I would put our inventiveness and entrepreneurial spirit up against any country in the world. These are the traits that revolutions are built on, and the time may be quickly approaching for a new industrial revolution.
Steven Williams is author of the book Survival Is Not Mandatory: 10 Things Every CEO Should Know About Lean.
More Columns from The Right Approach
The Right Approach: ‘Twas the Night Before Christmas (Harley-style)The Right Approach: I Hear the Train A Comin'
The Right Approach: Culture Change is Key to a QMS
The Right Approach: Leadership 101—Be a Heretic, Not a Sheep
The Right Approach: Leadership 101—The Law of Legacy
The Right Approach: Leadership 101: The Law of Explosive Growth
The Right Approach: Leadership 101—The Law of Timing
The Right Approach: The Law of Sacrifice