-
-
News
News Highlights
- Books
Featured Books
- pcb007 Magazine
Latest Issues
Current IssueThe Hole Truth: Via Integrity in an HDI World
From the drilled hole to registration across multiple sequential lamination cycles, to the quality of your copper plating, via reliability in an HDI world is becoming an ever-greater challenge. This month we look at “The Hole Truth,” from creating the “perfect” via to how you can assure via quality and reliability, the first time, every time.
In Pursuit of Perfection: Defect Reduction
For bare PCB board fabrication, defect reduction is a critical aspect of a company's bottom line profitability. In this issue, we examine how imaging, etching, and plating processes can provide information and insight into reducing defects and increasing yields.
Voices of the Industry
We take the pulse of the PCB industry by sharing insights from leading fabricators and suppliers in this month's issue. We've gathered their thoughts on the new U.S. administration, spending, the war in Ukraine, and their most pressing needs. It’s an eye-opening and enlightening look behind the curtain.
- Articles
- Columns
- Links
- Media kit
||| MENU - pcb007 Magazine
Estimated reading time: 15 minutes
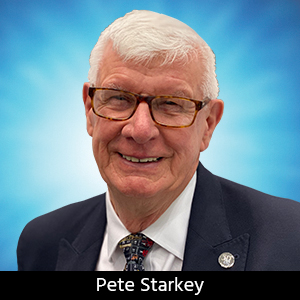
Contact Columnist Form
NPL/SMART Group Conformal Coating & Cleaning Experience
From a design point of view, it was necessary to carefully consider component layout, especially if dip coating was specified, to avoid features such as open through-hole vias, and to add tooling holes appropriate to the application method. The essential elements of a conformal coating drawing were definitions of: cleanliness requirements, areas to be masked and method of masking, conformal coating type, application method, thickness specification and inspection standards.
A good crowd gathered to hear Phil Atkinson of Fraser Technologies put his perspective on the need for cleaning before conformal coating. Having outlined the general benefits offered by conformal coating: Protection against moisture intrusion, humidity, shock, vibration, and corrosion, as well as electrical insulation, he summarised the properties and relative merits of the range of coatings available: Acrylics, urethanes, epoxies, silicones, and polyparaxylenes. There was no universal solution; it was a matter of intelligent selection in respect of performance requirements such as operating temperature, moisture resistance, chemical resistance, and whether formal qualification was required.
Why clean? He described the surface of a PCB assembly as a “chemical residue soup” which, before lead-free, did not generally present a significant problem and most conformal coatings could be successfully applied directly without cleaning. However, as technology had progressed with tighter packing densities, higher operating frequencies, and higher power, coating without cleaning was not recommended. Lead-free had been the real game-changer, with higher process temperatures and more tenacious residues, and he listed a whole range of contaminants that could be present--originating from the PCB and components as well as from the assembly process itself--and gave examples of failures that they could cause. In summary, he advocated that cleaning before coating was good practice, and recommended ionic cleanliness testing to prove its effectiveness. An appropriate cleaning process could promote optimum coating adhesion, whereas a poor cleaning process was the root cause of many coating defects.
The third presentation came from Willis himself, giving advice on selecting a coating based on product and environment. Why conformal coat? He listed several purposes: To prevent premature failure, to improve the performance of specific components, to improve environmental protection, as a possible alternative to a sealed enclosure to reduce the cost of the end product, and to ruggedize a product design. He then summarised the characteristics of available coatings and typical coating thicknesses. A golden rule was never to use conformal coating to overcome process problems by attempting to cover them up--it was vital to have a properly engineered and controlled assembly process in place before considering any conformal coating operation. He showed many examples of process and field failures, explained their causes, and recommended consulting the NPL Process Defect Database--freely available--as a point of reference to help identify and resolve problems.
Page 2 of 7
More Columns from The European Angle
CircuitData: A New Open Standard for PCB Fab Data ExchangeI Never Realised It Was So Complicated!
The European Angle: Institute of Circuit Technology 43rd Annual Symposium
Ventec International Group's Martin Cotton Celebrates 50 Years in PCB Design
Reporting on the Institute of Circuit Technology Spring Seminar
EuroTech: Raw Materials Supply Chain—Critical Challenges Facing the PCB Industry
EuroTech: ENIPIG—Next Generation of PCB Surface Finish
EuroTech: Institute of Circuit Technology Northern Seminar 2016, Harrogate