-
- News
- Books
Featured Books
- pcb007 Magazine
Latest Issues
Current IssueInventing the Future with SEL
Two years after launching its state-of-the-art PCB facility, SEL shares lessons in vision, execution, and innovation, plus insights from industry icons and technology leaders shaping the future of PCB fabrication.
Sales: From Pitch to PO
From the first cold call to finally receiving that first purchase order, the July PCB007 Magazine breaks down some critical parts of the sales stack. To up your sales game, read on!
The Hole Truth: Via Integrity in an HDI World
From the drilled hole to registration across multiple sequential lamination cycles, to the quality of your copper plating, via reliability in an HDI world is becoming an ever-greater challenge. This month we look at “The Hole Truth,” from creating the “perfect” via to how you can assure via quality and reliability, the first time, every time.
- Articles
- Columns
- Links
- Media kit
||| MENU - pcb007 Magazine
Estimated reading time: 8 minutes
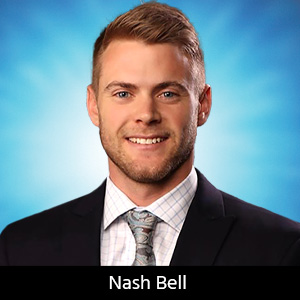
Knocking Down the Bone Pile: Addressing End-of-life Component Solderability Issues, Part 4
In 1983, the Department of Defense identified that over 40% of military electronic system failures in the field were electrical, with approximately 50% attributed to poor solder connections. Investigations revealed that plated finishes, typically nickel or tin, were porous and non-intermetallic.
This porosity allowed oxide penetration into the base metal, compromising solder joint integrity and leading to field failures. Consequently, the MIL-STD-883 solderability testing standard was established to ensure all components used in high-reliability applications would be reliably solderable. This shift in standards favored hot solder dip finishes, which produce a fused, homogeneous tin-lead (SnPb) coating, enhancing solderability and joint reliability.
Solderability testing evaluates how effectively molten solder wets the surface of electronic components, indicating how easily a strong and reliable solder joint can be formed. It provides a critical measure of the surface’s ability to adhere and create a solid electrical and mechanical connection. This testing is primarily used to assess the solderability of device package terminations, such as leads, pads, and terminal surfaces, which can vary significantly depending on the solder alloy used. Different alloys, including lead-based and lead-free solders, can exhibit distinct wetting behaviors, making accurate testing essential for ensuring reliable assembly.
Several industry-standard solderability testing methods are used to evaluate component surfaces. The most common are MIL-STD-883 Method 2003, IPC J-STD-002, and MIL-STD-202 Method 208. These standards define testing procedures, criteria, and pass/fail limits tailored to different types of components and applications. Two prevalent test techniques are the dip-and-look and wetting balance methods.
Dip-and-look Test Method
The dip-and-look method is a popular choice for routine solderability assessments. Its primary benefit lies in its simplicity: it is based on a straightforward comparative analysis, allowing personnel on the shop floor to assess solderability quickly with no need for complex equipment. It requires minimal training, making it accessible to a range of operators. It also involves significantly lower capital investment compared with the more sophisticated wetting balance system, making it suitable for high-volume production environments where cost and speed are critical.
Despite its advantages, the dip-and-look method has limitations. Since it is visually based, it is inherently subjective, relying on the operator's judgment to determine whether the solder coverage is sufficient and free of defects, such as bridging, misses, or insufficient wetting. This creates inconsistencies, particularly without proper operator training or standardized inspection, providing a qualitative, rather than a quantitative, measure of solderability.
For high-reliability applications, engineers may need to conduct additional testing to ensure long-term integrity and performance. For example, steam aging tests, which subject components to elevated temperatures and humidity, simulate extended storage or environmental exposure. These accelerated life tests help evaluate whether solder joints maintain their integrity over time, providing additional confidence for components destined for critical applications.
The dip-and-look method is ideal for rapid, cost-effective screening during production, but may require supplemental testing, such as visual inspections or environmental aging, to meet stringent reliability standards.
Wetting Balance Test Method
The wetting balance test method’s foremost advantage is its precision in measuring the forces involved in wetting molten solder onto a test specimen. Quantifying these forces as a function of time provides detailed, reproducible data on solderability that surpasses visual inspection methods, making it an invaluable tool for evaluating solderability in research and quality control environments, particularly when assessing subtle differences or the effects of process variations.
However, there are no established industry standard pass/fail criteria for wetting balance analysis, so engineers use it primarily as a tool rather than a routine production monitor. To establish a definitive pass/fail criterion, engineers perform a dip-and-look test to confirm solderability visually, since an acceptable wetting force alone does not guarantee a defect-free joint. For instance, after converting a RoHS-compliant device, such as a 20-mil pitch quad flat package (QFP) to tin-lead, a wetting balance test may show a bridge-free result (Figure 1). Inspectors must validate it visually.
Another disadvantage is needing skilled personnel to interpret the wetting curves accurately. The results can be easily misinterpreted if the system is not properly calibrated or if tests are performed improperly by untrained or inexperienced operators. For example, misreading the differences between the "before" and "after" solderability curves, such as those from a re-tinned component, can lead to incorrect conclusions about the component’s performance or the effectiveness of the re-tinning process (Figure 2).
This technique also demands a controlled laboratory environment to maintain consistent test conditions, including temperature stability and proper calibration of the testing equipment. Misalignment, improper specimen preparation, or inconsistent procedures can distort the wetting curves, undermining the reliability of the results. While the wetting balance method provides detailed and quantitative insights, it is best used by experienced personnel in a well-maintained testing environment. This is often part of development or qualification testing, rather than a routine production quality control method.
Both methods help ensure that the component's solderable surfaces are properly prepared and meet reliability standards. They are especially useful when switching between solder alloys, from lead-based to lead-free, or changing processing conditions. Note: There are no universally established industry pass/fail criteria based solely on wetting balance measurements. Engineers primarily use these tests for development and qualification rather than routine production monitoring. Verification with visual inspection or additional test methods is often necessary to confirm acceptable solderability.
Clarifying the Difference: Solderability Testing vs. Re-tinning
Although component re-tinning or preconditioning is not a formal solderability test, it is an effective method for reworking components with poor or degraded solderability. Severe oxidation of the component surfaces often causes this degradation, typically from prolonged storage in warehouse environments. Oxidation creates a barrier that hampers proper wetting and joint formation during soldering, thereby compromising reliability. Re-tinning involves applying a fresh layer of solder to restore surface conditions, ensuring better wettability and bonding during assembly.
This process is particularly valuable for high-reliability or end-of-life product builds, where salvaging existing components can be a cost-effective alternative to discarding and replacing them. For example, with a fine-pitch quad flat package (QFP) device, re-tinning with a side wave process can eliminate surface oxidation and bridge-free solder joints, ensuring the component meets the necessary quality standards (Figure 3). Proper re-tinning not only improves solderability but also enhances the overall reliability of the solder joints during operational life.
While re-tinning is a useful remedial step, it is important to verify the effectiveness of the process through visual inspection and, if necessary, additional solderability testing, especially for critical or high-reliability applications.
There is often confusion within the industry regarding solderability testing vs. component re-tinning. Solderability testing assesses how well molten solder will wet and adhere to a component’s surface, with common methods being qualitative (visual inspection after dipping) and quantitative (wetting balance measurements). Conversely, re-tinning involves physically applying a fresh layer of solder via immersion into a molten solder bath to create a highly solderable surface with a new intermetallic layer. This process restores and enhances the component’s surface condition, especially when original finishes have degraded.
Industry Applications of Component Re-tinning
Companies actively engaged in component re-tinning include defense, military, and aerospace OEMs, as well as medical device manufacturers and other high-reliability OEMs. Contract electronics manufacturers (CEMs) working within the defense, aerospace, medical, and high-reliability sectors frequently perform re-tinning, especially when dealing with legacy components or end-of-life builds. This process is critical for maintaining supply chain integrity and ensuring long-term reliability of critical assemblies.
Re-tinning Best Practices
To produce a high-quality intermetallic layer during re-tinning, it is essential to perform solderability testing both before and after the process—using tools like dip-and-look or wetting balance systems—to confirm that the surface is suitable for reliable solder joints. Proper pre-cleaning of components is also critical; organics and oxides must be removed to facilitate effective re-tinning.
Technicians typically perform the re-tinning in a dual solder pot setup. The first bath removes unwanted plating and oxides, while the second applies a controlled, uniform solder alloy coating. Technicians should also carefully control parameters such as immersion speed, dwell time, depth, and extraction speed to ensure consistency across components.
Flux Selection and Application
Flux choice is vital in the re-tinning process. Since rosin-based fluxes are generally specified for solderability testing rather than re-tinning, the recommendation is to use fluxes suited for the specific termination finish. When post-tinning cleaning is permitted, it is preferable to use water-based (low pH) fluxes, which help remove residual flux and oxides cleanly. For components that cannot undergo post-tinning cleaning, no-clean, alcohol-based fluxes are suitable. Minimize flux volume in all cases. The goal is to fully coat the termination without leaving excess residue, which could interfere with subsequent assembly or reliability.
Preheat Considerations for Re-tinning
For many through-hole and surface-mount components—particularly plastic-bodied parts—brief contact of the leads or terminations with solder for about five seconds is sufficient for re-tinning without preheating, simplifying the process. However, it’s essential that components with ceramic or glass bodies, or other thermally sensitive materials, be preheated to reduce thermal shock and prevent damage. Infrared preheating systems are effective, providing rapid, uniform heating, but can pose a risk of damage if not carefully controlled. Forced convection preheating offers a more uniform and controllable approach, minimizing thermal stress on sensitive components.
Additional Testing for High-reliability Applications
In certain high-reliability environments, supplemental solderability testing is often recommended to verify the robustness of the re-tinned surfaces, particularly after processes like steam aging, which simulates long-term storage conditions, exposing components to elevated humidity and temperature, accelerating the aging process. This method assesses how well the solderable surface maintains its integrity over extended periods, effectively reproducing a typical shelf life, often equating to about five years.
To ensure re-tinned components meet reliability standards, manufacturers recommend a minimum solder thickness of approximately 150 microinches (3.81 µm) before aging, which provides sufficient intermetallic layer growth to withstand environmental stressors. Non-destructive measurement techniques, such as X-ray fluorescence (XRF), verify solder thickness and composition, while scanning electron microscope (SEM) analysis can be employed to examine the intermetallic layer, if necessary.
Conclusion
Solderability directly affects the reliability and longevity of electronic systems. Since the recognition of high failure rates linked to porous finishes in the 1980s, standards and testing protocols have evolved to ensure high-quality, reliable joints. Industry-standard methods like dip-and-look and wetting balance testing play vital roles in verifying surface conditions. Re-tinning is an effective remedial technique for restoring solderability to oxidized or aged components, especially in high-reliability applications. Proper process control, thorough pre-cleaning, and appropriate testing, together with aging simulations such as steam aging, are essential to validate the long-term performance of soldered joints. Together, these practices contribute to robust, dependable electronic assemblies that meet stringent industry requirements.
This column originally appeared in the July 2025 issue of SMT007 Magazine.
More Columns from Knocking Down the Bone Pile
Knocking Down the Bone Pile: Tin Whisker Mitigation in Aerospace Applications, Part 3Knocking Down the Bone Pile: Gold Mitigation for Class 2 Electronics
Knocking Down the Bone Pile: Basics of Component Lead Tinning
Knocking Down the Bone Pile: Package on Package Rework—Skill Required
Knocking Down the Bone Pile: 2023’s Top Challenges in BGA Rework
Knocking Down the Bone Pile: Eliminating Solder Balls in Hand Soldering
Knocking Down the Bone Pile: Opening a Trace on the Surface of a PCB
Knocking Down the Bone Pile: Soldering for QFPs and Other Gull Wing Leaded Parts