-
- News
- Books
Featured Books
- pcb007 Magazine
Latest Issues
Current IssueInventing the Future with SEL
Two years after launching its state-of-the-art PCB facility, SEL shares lessons in vision, execution, and innovation, plus insights from industry icons and technology leaders shaping the future of PCB fabrication.
Sales: From Pitch to PO
From the first cold call to finally receiving that first purchase order, the July PCB007 Magazine breaks down some critical parts of the sales stack. To up your sales game, read on!
The Hole Truth: Via Integrity in an HDI World
From the drilled hole to registration across multiple sequential lamination cycles, to the quality of your copper plating, via reliability in an HDI world is becoming an ever-greater challenge. This month we look at “The Hole Truth,” from creating the “perfect” via to how you can assure via quality and reliability, the first time, every time.
- Articles
- Columns
- Links
- Media kit
||| MENU - pcb007 Magazine
Specially Developed for Laser Plastic Welding from LPKF
June 25, 2025 | LPKFEstimated reading time: 1 minute
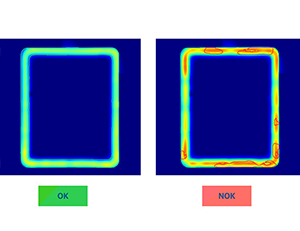
LPKF introduces TherMoPro, a thermographic analysis system specifically developed for laser plastic welding that transforms thermal data into concrete actionable insights. Through automated capture, evaluation, and interpretation of surface temperature patterns immediately after welding, the system provides unprecedented process transparency that correlates with product joining quality and long-term product stability. TherMoPro data enables welding process optimization to enhance component strength and long-term stability in a new dimension – completely non-destructively.
The system is designed for easy integration into existing production lines as a retrofit solution or as part of any new installation from the LPKF laser plastic welding product portfolio. Since thermographic analysis takes place directly after the welding process, usually cycle-time neutral, TherMoPro saves valuable space and time. Depending on the process, this inline approach can replace conventional quality control stations or reduce testing intervals for cost-intensive additional inspections, thus keeping production flow efficient – including full process transparency and traceability to every product ID.
"TherMoPro is far more than a standard thermal camera," explains Thomas Sontheimer, Senior Project Leader WeldingEquipment at LPKF. "Our solution approach offers real added value through the perfect synergy between specialized data acquisition and application-oriented analysis."
Developed in collaboration with experts specifically from the field of Automatic Optical Inspection (AOI), the system converts complex thermal data into more than 20 different quality parameters. This comprehensive analysis enables users to:
• Identify components that pass initial leak tests but would fail during temperature cycling tests
• Optimize processes for improved strength and reduced cycle times
• Monitor material property or process variations in real-time
• Achieve secure traceability with thermal data linked to each component ID
Benefits for markets with high quality requirements
For medical device manufacturers, the TherMoPro system provides the foundation for regulatory compliance, essential documentation requirements, and traceability while ensuring the long-term integrity of, for example, fluid-carrying components and sensitive enclosures. The ability to detect subtle thermal anomalies is particularly important for components with zero-defect tolerance.
Automotive suppliers benefit from TherMoPro's ability to monitor production variations in multi-cavity tools, ensuring consistent quality in high-volume production. As the industry increasingly incorporates recycled materials and flame retardants into plastic components, the system's ability to detect and compensate for varying material properties becomes crucial for maintaining quality standards while meeting sustainability goals.
Testimonial
"We’re proud to call I-Connect007 a trusted partner. Their innovative approach and industry insight made our podcast collaboration a success by connecting us with the right audience and delivering real results."
Julia McCaffrey - NCAB GroupSuggested Items
MacDermid Alpha Awarded for Innovation: Driving Process Optimization and Efficiency with Major Indian EMS Provider
08/28/2025 | MacDermid Alpha Electronics SolutionsMacDermid Alpha Electronics Solutions, a leading global supplier of integrated materials for the electronics industry, is recognized by one of India’s top EMS providers, Syrma SGS, with an award for innovation that advanced process optimization, enhanced operational efficiency, and yield gains.
Partnerships Drive Innovation for a Brighter Manufacturing Future
08/26/2025 | Barry Matties, I-Connect007When Schweitzer Engineering Laboratories (SEL) opened its greenfield facility in 2023, it did so with careful attention to choosing its suppliers. In this discussion, Collin Peters, electronics business director for North America at MKS’ Atotech, and Justin Kennedy, manager of engineering at SEL, explore their unique partnership that includes collaborative efforts to develop innovative solutions like the Uniplate® PLBCu6 line.
The Art and Science of PCB Floor Planning: A Comprehensive Guide
08/14/2025 | Cory Grunwald and Jeff Reinhold, Monsoon SolutionsPCB design is an intricate and crucial part of developing electronic products. One of the foundational stages of PCB design is floor planning, a phase where the placement of components and the flow of signals are meticulously mapped out. A good floor plan ensures that the PCB performs well, is easy to manufacture, and meets all mechanical and electrical requirements. We’ll explore the essential aspects of floor planning, from its objectives and process to the challenges that designers face.
Advint and SanRex Expand High-Performance DC Rectifier Access for North American PCB Fabricators
08/12/2025 | Advint IncorporatedAdvint Incorporated has entered a strategic partnership with SanRex Corporation, enhancing access to industrial-grade DC rectifiers for the US printed circuit board industry. With a legacy of power innovation and performance across the globe, SanRex rectifiers are available through Advint’s proficient distribution network.
Advint and Sayron Bring Advanced Rectifier Solutions to High-Reliability PCB Manufacturers
08/01/2025 | Advint IncorporatedAdvint Incorporated has partnered with Sayron, a leading global rectifier manufacturer, to supply cutting-edge IGBT-based DC rectifiers to high-performance PCB manufacturers across North America and beyond. Sayron’s precision-engineered rectifiers align with the stringent requirements of advanced PCB processes.