-
- News
- Books
Featured Books
- pcb007 Magazine
Latest Issues
Current IssueInventing the Future with SEL
Two years after launching its state-of-the-art PCB facility, SEL shares lessons in vision, execution, and innovation, plus insights from industry icons and technology leaders shaping the future of PCB fabrication.
Sales: From Pitch to PO
From the first cold call to finally receiving that first purchase order, the July PCB007 Magazine breaks down some critical parts of the sales stack. To up your sales game, read on!
The Hole Truth: Via Integrity in an HDI World
From the drilled hole to registration across multiple sequential lamination cycles, to the quality of your copper plating, via reliability in an HDI world is becoming an ever-greater challenge. This month we look at “The Hole Truth,” from creating the “perfect” via to how you can assure via quality and reliability, the first time, every time.
- Articles
- Columns
- Links
- Media kit
||| MENU - pcb007 Magazine
Estimated reading time: 4 minutes
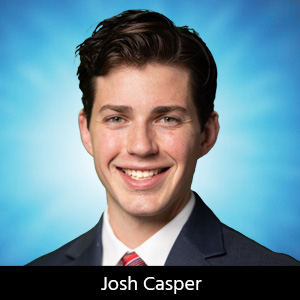
Smart Automation: The Growing Role of Additive Manufacturing
As additive manufacturing (AM) matures and reaches new business sectors throughout the manufacturing world, electronics manufacturing is beginning to reap the benefits of this ultra-flexible technology. AM (also known as 3D printing) capabilities have now expanded to support a wide range of applications in the electronics industry. The development of materials in additive manufacturing is meeting the demands of high-temperature environments and ESD protection necessary to become a viable solution in electronics manufacturing.
From the production of essential support items such as wave solder pallets and JEDEC trays to the creation of highly customized hand soldering fixtures and support tooling, AM is helping to reduce costs and improve efficiency. Here, we’ll explore AM’s impact on electronics manufacturing. From the improvements that have made it a viable solution, to some of the real-world applications existing today.
Advanced Materials for Higher Temperatures, Strength, and ESD Protection
One of the recent developments of additive manufacturing is the improvement in materials, allowing AM to meet the specific demands of the industry. As electronics manufacturing involves exposure to high temperatures, particularly during processes like wave soldering and reflow, AM materials have evolved to withstand these conditions.
Materials such as high-temperature-resistant carbon fiber peek, enable the production of parts that can endure the heat generated during processes like wave soldering. These materials retain their integrity even at temperatures exceeding 250°C, making them ideal for applications where traditional AM plastics might fail.
In addition to temperature resistance, the strength of additive manufacturing materials has significantly improved in recent years. Today, manufacturers have access to materials with enhanced strength and durability. This is particularly important in applications where support tooling needs to remain rigid and flat to hold products in place without the risk of warping. Materials like carbon fiber polymers offer significantly enhanced strength, allowing the production of parts that are both lightweight and capable of handling the forces encountered during production processes.
Additionally, with the importance of ESD protection in electronics, additive manufacturing has advanced to include materials with integrated conductive or dissipative properties. AM companies can produce parts that prevent electrostatic buildup and discharge, reducing the risk of damage to sensitive components. These materials can safely be used in applications ranging from JEDEC trays to wave solder pallets, ensuring that all parts remain safe during manufacturing and transport.
Additive Manufacturing and Wave Solder Pallets
Wave solder pallets are typically manufactured utilizing traditional subtractive manufacturing approaches, such as milling, drilling, cutting, etc. This involves the removal of material from a solid block to achieve the desired form. While capable of high precision, these methods can be time-consuming and expensive, particularly when producing intricate parts. These small inefficiencies can create a bottleneck in PCB manufacturing.
Additive manufacturing addresses these limitations by enabling the production of highly customized wave solder pallets. Manufacturers can use design and print pallets tailored to the unique dimensions of the PCB and the components being assembled. This not only provides greater flexibility in production but also allows for quicker turnaround times. Manufacturers can easily iterate and adjust the design of their solder pallets digitally.
In addition, customization can extend to features like ventilation channels and optimal support structures to further improve soldering quality, something that some traditional manufacturing methods struggle to accommodate.
JEDEC Trays
JEDEC trays play an essential role in the handling, storage, and transport of sensitive surface-mount components. Traditional manufacturing of these trays can be both time-consuming and expensive, particularly when manufacturers require customized designs to accommodate different component sizes.
Additive manufacturing provides a solution to these challenges by enabling the production of JEDEC trays with tailored dimensions, optimized for specific component types. As additive manufacturing technology continues to evolve, it is likely that manufacturers will increasingly rely on 3D printing to produce JEDEC trays that not only protect components but also reduce production costs and improve supply chain efficiency.
The reduction in lead times is another important benefit of additive manufacturing in JEDEC tray production. By printing trays on demand rather than waiting for mass production or custom molds, manufacturers can more quickly respond to changing production requirements and avoid inventory shortages.
Support Tooling: Cost-Effective and Customizable Solutions
Support tooling, such as jigs, guides, and holding fixtures, are used in several assembly processes, ensuring components are correctly positioned and securely held during operations like inspection, testing, or assembly.
Additive manufacturing provides a cost-effective and highly flexible solution. By designing and printing support tooling in-house, manufacturers can create custom tools that are specifically suited to the requirements of a particular job. Whether it's a jig designed to hold a complex PCB shape, or a guide that helps position a specific component, additive manufacturing makes it possible to quickly produce tools with tailored features.
This ability to design and produce custom support tooling can lead to significant cost savings, as it can significantly reduce the involvement and stress on a manufacturers labor force. Additionally, additive manufacturing supports rapid design iterations, allowing manufacturers to refine their tools quickly to improve performance and efficiency.
Additive manufacturing is quickly becoming an essential tool in electronics manufacturing. The ability to produce customized support items offers manufacturers greater flexibility, faster lead times, and reduced costs. As this technology continues to advance, additive manufacturing will play an even more significant role in shaping the future of electronics production, driving innovation, and improving efficiency across the industry.
This column originally appeared in the April 2025 issue of SMT007 Magazine.
Josh Casper is regional sales manager for Horizon Sales.
More Columns from Smart Automation
Smart Automation: Pick-and-place Machines—What Matters in 2025Smart Automation: What Industry 4.0 Means for Mid-sized Electronics Manufacturing
Smart Automation: The Power of Data Integration in Electronics Manufacturing
Smart Automation: AI—Revolutionizing Inspection in Electronics Manufacturing