All-Inclusive: PRIDE Industries Helps Employees With Disabilities to Succeed
May 1, 2024 | Sandy Gentry, IPCEstimated reading time: 1 minute
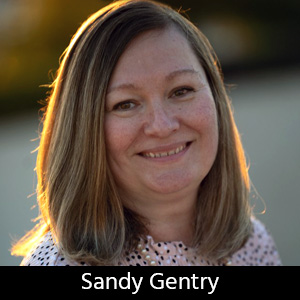
PRIDE Industries is the leading employer of people with disabilities and those with other barriers to employment in the United States, including veterans and former foster youth. The company offers job training, placement, on-the-job coaching, and skills development for independent living. It has held IPC membership since 2000.
Darelyn Pazdel is vice president of workforce inclusion at PRIDE Industries and provides an overview of the company’s breadth and depth for employees with disabilities in its manufacturing services division.
What is the size of the PRIDE Industries staff?
Darelyn Pazdel: PRIDE Industries has nearly 4,500 employees. About 2,000 have a disability. We have a team of 425 people who assist individuals with disabilities in securing employment both within PRIDE Industries and in the community.
PRIDE Industries operates across several states. How many of these companies include electronics manufacturing facilities?
PRIDE Industries has 37 offices in 17 states throughout the United States. In some communities, we operate as a true integrated model, meeting people in their communities. Our flagship electronics manufacturing facilities are in Roseville, California, where we are unique in the industry because we produce quality electronics supported by a disability-inclusive team.
How did PRIDE Industries create employment specific to electronics manufacturing for individuals with disabilities?
Individuals with disabilities are successful in many industries. Given our nearly 60 years of experience with our mission to create employment for people with disabilities, it’s what we do naturally. Our team works with our employees to provide tools for accommodation. It is our experience that the learning curve may be a little steeper for individuals with disabilities; however, once they learn tasks and have the tools necessary, they deliver high-quality services and products. Electronics manufacturing for individuals with disabilities has been a natural fit for our organization.
To read the rest of this article in the Spring 2024 issue of IPC Community, click here.
Suggested Items
Collaborative Robots: Shaping the Future of Automation
02/19/2025 | Transparency Market ResearchCollaborative robots, or cobots, have revolutionized the way industries approach automation. Unlike traditional robots, which require safety cages and are separated from human workers, cobots are designed to work safely alongside humans. This fundamental shift allows businesses of all sizes to harness automation in a flexible, cost-effective, and scalable manner.
Zhen Ding Selected for the 2025 S&P Global Sustainability Yearbook
02/17/2025 | Zhen DingZhen Ding Technology Holding Limited was honored with international recognition for sustainability as it was selected for the S&P Global Sustainability Yearbook for the third consecutive year.
Cofactr Acquires AI to Streamline Electronics Supply Chains
02/06/2025 | BUSINESS WIRECofactr, a supply chain and logistics management platform that streamlines parts sourcing, production and processes for high-compliance and agile hardware manufacturers, announced the acquisition of AI-based solution Factor.io.
A3 Reports North American Robotics Market Holds Steady in 2024 Amid Sectoral Variability
02/05/2025 | BUSINESS WIREThe North American robotics market demonstrated minor overall growth in 2024, reflecting resilience and adaptability as automation strengthened its role across industries.
RIKEN Adopts Siemens' Emulation And High-Level Synthesis Platforms for Next-Generation AI Device Research
01/16/2025 | SiemensSiemens Digital Industries Software announced today that RIKEN, a national research and development agency in Japan, is enhancing its research on next-generation AI devices with Siemens' comprehensive Veloce™