-
-
News
News Highlights
- Books
Featured Books
- pcb007 Magazine
Latest Issues
Current IssueSales: From Pitch to PO
From the first cold call to finally receiving that first purchase order, the July PCB007 Magazine breaks down some critical parts of the sales stack. To up your sales game, read on!
The Hole Truth: Via Integrity in an HDI World
From the drilled hole to registration across multiple sequential lamination cycles, to the quality of your copper plating, via reliability in an HDI world is becoming an ever-greater challenge. This month we look at “The Hole Truth,” from creating the “perfect” via to how you can assure via quality and reliability, the first time, every time.
In Pursuit of Perfection: Defect Reduction
For bare PCB board fabrication, defect reduction is a critical aspect of a company's bottom line profitability. In this issue, we examine how imaging, etching, and plating processes can provide information and insight into reducing defects and increasing yields.
- Articles
- Columns
- Links
- Media kit
||| MENU - pcb007 Magazine
Estimated reading time: 6 minutes
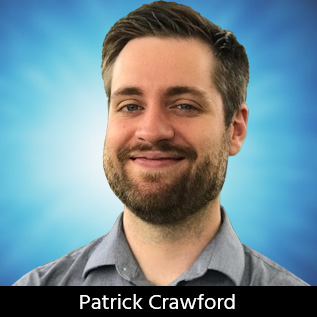
Design Circuit: The Cost of Compliance and How Data Transfer Standards Can Help
In the more than half-century since the rise of electronic devices, nearly every human being on the planet has, at some point in their life, come into contact with one. As this contact became an inevitability in most parts of the world, human health and safety also became a critical factor in the design of all electronics. From this need to protect users from the myriad deleterious effect of toxins in electronics there arose dozens of global regulations regarding hazardous substances.
(A necessary caveat: There are drivers for these regulations that have absolutely nothing to do with electronics. But seeing as this is a publication targeting the design of electronic circuits, I will not be spending too much time discussing leather for car seats or thermoset plastics for electric drill bodies, etc.)
One such regulation that I am sure most electronics manufacturing industry professionals are aware of is the EU Restriction of Hazardous Substances (RoHS), the most recent version of which bans the use of 10 substances in the EU which have been proven to have negative impacts on human health and safety. Perhaps most well-known to electronics is Pb (lead) which prompted the need for (and conversion to, in most cases) Pb-free solder. Need I go on?
Of course, EU RoHS is only one example of a restriction of substances, and that is not the only RoHS. However, this column is not intended to educate on the various regulatory agencies and their programs, nor provide instruction on which compounds and substances should or should not be used for fabricating boards. Resources already exist on such matters which far outpace both my understanding of the duties and nuance of these regulations and of the chemistries cited therein. Furthermore, this is not an opinion piece regarding the merits of these various regulations.
Rather, I want to look at one of the chief cost-burdens associated with complying with these regulations, specifically the cost of obtaining and communicating materials information throughout the supply chain.
As an example, let us consider the new reporting obligations associated with the European Chemicals Agency’s (ECHA) substances of concern in articles as such, or in complex objects (products) (SCIP) database. In brief, the European Union (EU) Directive 2008/98/EC on Waste, commonly referred to as the EU Waste Framework Directive (WFD), entered into force in July 2018. The WFD set requirements on waste management, recycling, and recovery of products manufactured in, supplied to, or imported to the European Economic Area. As part of these requirements, the WFD mandates that any article containing substances of very high concern (SVHCs) must be declared to the ECHA so that this information can be made available to waste operators and consumers. The database is now live with more than four million submissions available for review (Whew).
Even more, if your product contains a candidate list substance and you would like to manufacture or sell it in the EU, you have to notify ECHA and declare whether any of those candidate list substances are below threshold.
As I indicated, almost every engineer has heard of RoHS, and most have probably heard of REACH. But if you are not a compliance manager, or in some other kind of purchasing or procurement role where you are exposed to the immensity of your supply chain, you may not be aware of how onerous determining whether your product contains SVHCs (let alone their positions in product, percentage of total mass and whether they are above threshold, etc.) can be.
Let’s look at an example specific to the SCIP database, keeping in mind that I am making this as absolutely generic as I possibly can. Consider hypothetical Company A is an OEM producing inexpensive, low-complexity phones. In fact, these phones are so low-complexity, that Company A has only two suppliers—Company B and Company C.
Now, Company A is based in Canada but would like to sell into the EU. They find a distributor in Germany who will provide to convenience stores there and in a few neighboring countries. On top of other bureaucratic necessities—too many to name here—Company A learns that they may have obligations to report to ECHA.
A representative from Company A contacts Company B and C and asks them to provide chemicals information on their products. As it turns out, Company B’s supplier stream is a bit wider, and now they have to contact their suppliers—all 10 of them—to ensure their chemicals composition, and onward and upward the pipeline. Company C, feeling proud of their proactivity, provides Company A with an Excel sheet containing candidate list substances (and a few others for good measure). Of course, the information does not satisfy all requirements needed for SCIP; you get the idea.
Oh, and when Company B does get back to Company A a few months later, they hand over a PDF report.
What is critical in this overly-cartoonish example is that there are real humans performing real work to support every action verb in the above paragraph. Consider the very real complexity of your supply chain, even if you are not a tier one company, and you can understand how complying with even one global regulation can add to your costs.
I will pause here to reiterate that I am not making a judgment on the merit of these regulations, but rather pointing out that there are objective costs associated with compliance thereof. For more information on IPC’s official position on these regulations and how we are supporting industry going forward, please reach out to the IPC Government Relations department. You can find more information on IPC.org.
What can you or your company do to attempt to minimize costs? Three words can certainly help: data transfer standards.
Apart from design standards, my other hat is to manage the committees that are responsible for the IPC-1750 family of supplier declaration standards. These documents all describe xml file formats which enable companies to request data from their suppliers or push data to their customers that relate to various regulatory requirements: RoHS, REACH, data sufficient for a SCIP submission, etc. The beauty of the xml format is it’s standardized across submissions, so a company can eliminate the manpower associated with parsing various data formats from their suppliers or negotiating submission data formats with their customers. It’s all just IPC-1752 or IPC-1754 (material declarations and materials and substances declaration for aerospace, defense, and other industries, respectively); communicating data pursuant to SCIP; IPC-1755 (responsible minerals sourcing) communicating information pursuant to EU Conflict Minerals Legislation; or IPC-1753 (lab reports) communicating analytical lab report data. There are no miscellaneous data formats that must be reckoned with.
If a company does not have the resources to create an in-house system to receive and collate these files, then they can utilize one of the many solution providers who offer compliance tools that are capable of importing and exporting IPC-1750 family compliant files. Most of them will contact suppliers and communicate with customers on your behalf to collect and manage data. (These companies are all verified by IPC to ensure that their data is, indeed, compliant.) Of course, there are up-front costs associated with purchasing any given compliance tool or service, and you or your company should weigh this before making any decisions.
These standards help eliminate costs by “greasing the wheels” of communication between companies in a supply chain. They do not necessarily eliminate the amount of data that is required to submit to customers or regulatory agencies, but they can help ensure that your company has all the data necessary to complete a submission. In my example, Company C did not provide the correct data to Company A, which would prompt another round (or 20) of back-and-forth until the correct information was obtained.
In the end, there will likely be a cost associated with compliance. However, with the proper tools, any electronics manufacturing company can mitigate those costs to the fullest extent possible. As regulations continue to evolve, IPC standards will be revised to match those regulations and their various requirements.
This column originally appeared in the November 2021 issue of Design007 Magazine.
More Columns from Design Circuit
Design Circuit: Green Ambition for the Electronics Manufacturing IndustryDesign Circuit: The IPC PCB Design Desk Reference is On Its Way
Design Circuit: IPC-2231A—Insights from the IPC 1-14 DFX Subcommittee
Design Circuit: 2021 Updates to IPC Design
Design Circuit: Failures of Imagination—A Column of Caution
Design Circuit: IPC-2231 Captures Board Design Best Practices
Design Circuit: An Update on the Italian IPC Design Chapter
Design Circuit: There Is No Knowledge That Is Not Power