-
- News
- Books
Featured Books
- pcb007 Magazine
Latest Issues
Current IssueInventing the Future with SEL
Two years after launching its state-of-the-art PCB facility, SEL shares lessons in vision, execution, and innovation, plus insights from industry icons and technology leaders shaping the future of PCB fabrication.
Sales: From Pitch to PO
From the first cold call to finally receiving that first purchase order, the July PCB007 Magazine breaks down some critical parts of the sales stack. To up your sales game, read on!
The Hole Truth: Via Integrity in an HDI World
From the drilled hole to registration across multiple sequential lamination cycles, to the quality of your copper plating, via reliability in an HDI world is becoming an ever-greater challenge. This month we look at “The Hole Truth,” from creating the “perfect” via to how you can assure via quality and reliability, the first time, every time.
- Articles
- Columns
- Links
- Media kit
||| MENU - pcb007 Magazine
Estimated reading time: 5 minutes
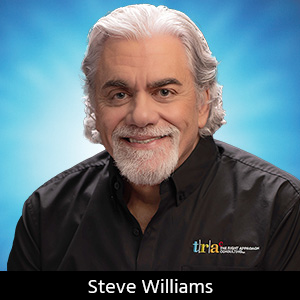
A Conversation With Prototron's Van Chiem
I recently spoke with Van Chiem, a process engineer with Prototron Circuits, about developing in-house flex and rigid-flex processes and capabilities at their facility in Tucson, Arizona.
Steve Williams: Van, you have a very diverse technical background in PCBs. Can you tell us a little bit about your past experience and what brought you to Prototron?
Van Chiem: I have over 25 years of experience in this field. I started as a process engineer at Unisys Corporation where we made computer chips and advanced component packaging for interconnections like wire bonding, flip chip, and tab bonding. This is my ninth job in the PCB industry. Another job I had was with Enthone in Connecticut at the time, which is now MacDermid Alpha Electronics Solutions. I was in the research group working on the formulation of solder mask to try and convert it to photodefinable dielectric material for microvia. Instead of drilling, we used a photo process to create a microvia, and then the electroless copper followed by plating the copper to form the microvia with smart circuitry. That was my second job in the industry. I have had seven more jobs, but that might be too much to talk about.
Williams: How about we save the other seven for the next interview (laughs). So, you’ve seen a lot of technology changes in the last 25 years in the industry and were actually one of the original technologists.
Chiem: Well, I don’t like to talk about myself, but I guess you could say that.
Williams: How long have you been at Prototron?
Chiem: About a year and a half.
Williams: And you have already accomplished quite a bit here. Prototron brought you on board for the specific purpose of upgrading their technology in a number of different areas, right?
Chiem: Yes, Kim O’Neil, the general manager here, brought me on especially to develop flex and rigid-flex processes.
Williams: So, you were kind of the R&D lead on developing that technology and getting it to become a viable technology here in Tucson. What was that process like, and what were the challenges?
Chiem: From a technology standpoint, there weren’t any major challenges, as this technology is 20–30 years old and very mature. I used to work at Honeywell back in the ‘90s where we built flex as a chip carrier every day and talked about 3-mil lines and spaces 20 years ago.
Williams: It may be new to Prototron, but it’s old to you?
Chiem: Exactly. We were doing some crazy PCB technology 20 years ago in Costa Mesa, California.
Williams: And did you have to do anything here from an equipment set standpoint, including changes to processes, or was it just a matter of using different raw materials?
Chiem: Of course, flex and rigid-flex require a different material set, but mainly, we just needed to develop custom frames, or material handling fixtures, to process the thin materials through Prototron’s standard, rigid PCB conveyorized equipment. The Tucson shop was set up for standard, rigid multilayer production, and the equipment set reflected that.
Williams: Were there any obstacles you had to overcome because the shop had never built flex here before? Did you have to re-educate the workers or develop new processes and retrain people on how to handle this type of material?
Chiem: We also had to modify our processes and procedures to adapt to flex processing. Then, it was just a matter of blending the current chemistry and equipment with the new frames to make flex a reality here at Prototron. As we’ve progressed, we’ve gained knowledge on how to develop the in-house flex capability. I also needed to train people, write specifications, upgrade the procedures, and make sure everybody was familiarized with the new processes.
Williams: Are you also looking at doing rigidflex?
Chiem: We have developed the processes and ran test orders successfully, so I am confident we can build rigid-flex here right now. It’s not difficult.
Williams: I love your confidence. I understand you’re currently working on another project with some very small mechanically drilled holes also.
Chiem: Correct. Kim wanted me to work on mechanically drilling 4-mil microvias using our current Schmoll drilling equipment.
Williams: And that would be controlled depth drilling of the microvias?
Chiem: Yes, 4-mil diameter by 5 mils deep.
Williams: Earlier, you mentioned that mechanically drilling 4-mil holes is not that big of a deal; it’s the fluid dynamics of getting the chemistry through a blind hole of that size hole.
Chiem: Therefore, we need to put in some new, different chemistry, as the current conventional chemistry that we have right now is not meant for this application.
Williams: So, it’s pretty standard microvia stuff, but you are doing it mechanically instead of laser drilling. Excellent. What else is on your to-do list for Prototron in advancing their technology levels?
Chiem: I think we are open to doing R&D collaboration with other companies on advanced technology. For instance, I am working with an organization in Toronto, Canada, to develop a very advanced PCB design. In that way, we have a mutual interest between the two companies. We can co-develop this PCB technology and process that can be applied at both companies.
Williams: Wow! As a fellow old board rat, I find this really interesting. What do you think the timeline is?
Chiem: All I can tell you is that it is an ongoing iterative process as design adjustments are made after each batch of PCBs are built and tested until the process is perfected.
Williams: It’s exciting to work with you. I know you’re doing a lot of great things here, and I’m looking forward to what you come up with next. Anyone who needs high-quality flex and rigid-flex PCBs can contact Van and the team at Prototron, and they will take care of you. Thanks for taking the time today to talk.
Chiem: Of course. I am always available to help.
Steve Williams is the president of The Right Approach Consulting.
More Columns from The Right Approach
The Right Approach: ‘Twas the Night Before Christmas (Harley-style)The Right Approach: I Hear the Train A Comin'
The Right Approach: Culture Change is Key to a QMS
The Right Approach: Leadership 101—Be a Heretic, Not a Sheep
The Right Approach: Leadership 101—The Law of Legacy
The Right Approach: Leadership 101: The Law of Explosive Growth
The Right Approach: Leadership 101—The Law of Timing
The Right Approach: The Law of Sacrifice