-
- News
- Books
Featured Books
- pcb007 Magazine
Latest Issues
Current IssueInventing the Future with SEL
Two years after launching its state-of-the-art PCB facility, SEL shares lessons in vision, execution, and innovation, plus insights from industry icons and technology leaders shaping the future of PCB fabrication.
Sales: From Pitch to PO
From the first cold call to finally receiving that first purchase order, the July PCB007 Magazine breaks down some critical parts of the sales stack. To up your sales game, read on!
The Hole Truth: Via Integrity in an HDI World
From the drilled hole to registration across multiple sequential lamination cycles, to the quality of your copper plating, via reliability in an HDI world is becoming an ever-greater challenge. This month we look at “The Hole Truth,” from creating the “perfect” via to how you can assure via quality and reliability, the first time, every time.
- Articles
- Columns
- Links
- Media kit
||| MENU - pcb007 Magazine
Estimated reading time: 1 minute
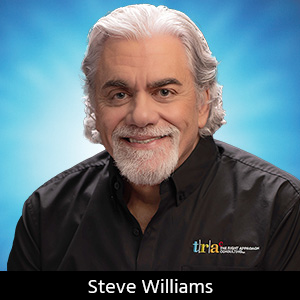
The Right Approach: Industry 5.0—Can We Learn From Other Industries?
The last few IPC APEX EXPO events have focused heavily on Industry 4.0, which is all about the Internet of Things (IoT), automation, and data exchange between machines.
Where do we go from here? Perhaps we can learn some lessons from the sheet metal and plastic industries.
Integration of 3D Printing
I first wrote about this burgeoning technology back in the September 2012 issue of The PCB Magazine with a column titled “Will ‘Old’ PCB Technology Save American Manufacturing?” which compared 3D printing to the original additive process of manufacturing PCBs.
Many of us old-school, pre-1980s technology board guys remember actually running the additive PCB process back in the day well before the subtractive process became the preferred methodology. The additive process was quite simple and had far fewer process steps than the complicated travelers seen in today’s PCB shops. There was neither a need for copper clad raw laminate nor current selective electroplating technologies. A negative image was defined on a resin substrate, and metal was selectively added, or built up, to form the circuitry and interconnects.
This was followed up in the October 2013 issue of The PCB Magazine with “Point of View: 3D Printing—Tales from the Road,” Industry 5.0: Can We Learn From Other Industries? which highlighted the successful utilization of 3D printing from my travels in a variety of industries, none of which were PCB manufacturing:
Medical
Peking University’s Dr. Liu Zhongjun has been using EBM 3D printing for the past nine years to develop new spinal implants (Figure 1). During that time, he has created hundreds of orthopedic implants that have been custom engineered to fit each specific patient’s body. He explains, “In the past, we used clinical titanium mesh, but with the growth of bone, titanium mesh could easily stick into the bone and cause collapse. 3D-printed implants fit the bone completely and allow the bone to grow into the implants.” Zhongjun continued, “In this aspect, 3D-printed implants are more reliable than traditional ones.”
Figure 1: 3D-printed spinal implant. (Source: Spinal Surgery News)
This article originally appeared in the December 2018 issue of PCB007 Magazine, click here.
More Columns from The Right Approach
The Right Approach: ‘Twas the Night Before Christmas (Harley-style)The Right Approach: I Hear the Train A Comin'
The Right Approach: Culture Change is Key to a QMS
The Right Approach: Leadership 101—Be a Heretic, Not a Sheep
The Right Approach: Leadership 101—The Law of Legacy
The Right Approach: Leadership 101: The Law of Explosive Growth
The Right Approach: Leadership 101—The Law of Timing
The Right Approach: The Law of Sacrifice