-
- News
- Books
Featured Books
- pcb007 Magazine
Latest Issues
Current IssueInventing the Future with SEL
Two years after launching its state-of-the-art PCB facility, SEL shares lessons in vision, execution, and innovation, plus insights from industry icons and technology leaders shaping the future of PCB fabrication.
Sales: From Pitch to PO
From the first cold call to finally receiving that first purchase order, the July PCB007 Magazine breaks down some critical parts of the sales stack. To up your sales game, read on!
The Hole Truth: Via Integrity in an HDI World
From the drilled hole to registration across multiple sequential lamination cycles, to the quality of your copper plating, via reliability in an HDI world is becoming an ever-greater challenge. This month we look at “The Hole Truth,” from creating the “perfect” via to how you can assure via quality and reliability, the first time, every time.
- Articles
- Columns
- Links
- Media kit
||| MENU - pcb007 Magazine
Estimated reading time: 3 minutes
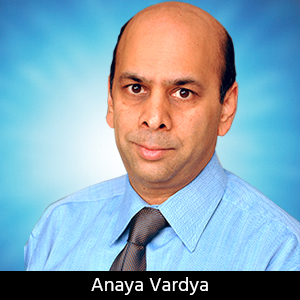
Standard of Excellence: The Advantages of Flex and Rigid-Flex Circuits
Since their introduction, flexible and rigid-flex circuits have been steadily moving from the fringe of electronic interconnection towards its center. Today, flex and rigid-flex circuits are found in countless products from the very simple to the highly complex. The reasons for this shift to the center are numerous; most of them are related to the advantages they offer. An examination of some of the benefits and advantages will make this clear.
A Remedy for Natural Packaging Problems
Flexible circuits are often chosen because they help to solve problems related to getting electronics inside the products they serve. They are a true three-dimensional solution that allows electronic components and functional/operation elements (i.e., switches, displays, connectors, and the like) to be placed in optimal locations within the product assuring ease of use by the consumer. They can be folded and formed around the edges to fit the space allowed without breaking the assembly into discrete pieces.
Reduced Assembly Costs
Prior to the broad use of flexible circuits, assemblies were commonly a collection of different circuits and connections. This situation resulted in the purchasing, kitting and assembly of many different parts. By using a flex design, the number of part numbers required for making circuit-related interconnections is reduced to one.
Eliminated Potential for Human Error
Because they are designed as an integrated circuit assembly with all interconnections controlled by the design work, the potential for human error in making interconnections is eliminated. This is especially true in the cases where discrete wires are used for interconnection.
Reduced Product Weight and Volume Requirements
Flexible circuits are appreciably lighter than their rigid counterparts. Depending on the components used and the exact structure of the assembly and the final product, they can save perhaps as much as 60% of the weight and space in the end-product as compared to a rigid circuit solution. Additionally, their lower profile can help a designer create a lower profile product than is possible with a nominal 1.5 mm-thick rigid board.
Facilitation of Dynamic Flexing
Nearly all flexible circuits are designed to be flexed or folded. In some unusual cases, even very thin rigid circuits have been able to serve to a limited degree. However, in the case where dynamic flexing of a circuit is required to meet the objectives of the design, flexible circuits have proven best. Modern disc drives, for example, require that a flexible circuit endure anywhere from tens to hundreds of millions of flexural cycles over the life of the product. Other products (laptop hinge circuits, for example) may only require thousands of the cycles, but it is the dynamic actuation capability enabled by the flex circuit that is key to its operation.
Improved Thermal Management for High-Temp Applications
High temperatures are experienced both in assembly with lead-free solder and in the operation of higher power and higher-frequency digital circuits. Polyimide materials are well suited to the management of high-heat applications. Not only can they handle the heat, their thinness allows them to dissipate heat better than other thicker and less thermally conductive dielectrics.
Improved Aesthetics
While aesthetics may seem a low-order advantage, people are commonly influenced by visual impressions and frequently make judgements based on those impressions. Flexible circuit materials and structures look impressive both to the seasoned engineer and the layperson. It can make a difference in the decisions made in some applications, especially those where the user gets exposure to the functional elements of the product.
Increased Intrinsic Reliability
Flexible circuits help to reduce the complexity of the assembly and can reduce the number of interconnections that might be otherwise required with solder. Reduction in complexity is a key objective of a reliable design. With respect to the minimization of the number of solder interconnections, reliability engineers know all too well that most failures in electronic systems occur at solder interconnections. It follows naturally that a reduction in the number of opportunities for failure should result in a corresponding increase in product reliability.
Conclusion
Flex and rigid-flex circuits have significant advantages. There are many additional advantages that go beyond the short list provided here. What is important to remember is that most of the advantages stem from the versatility and unique integrative abilities these important members of the electronic interconnect family can offer.
The information contained in this column was taken from American Standard Circuits’ new eBook, The Printed Circuit Board Designer’s Guide to Flex and Rigid-Flex Fundamentals, published by I-Connect007. To download the book, click here.
Dave Lackey is vice president of business development at American Standard Circuits.
More Columns from Standard of Excellence
Standard of Excellence: The Human Touch in an Automated WorldStandard of Excellence: Training Your Team to Excel in Customer Service
Standard of Excellence: Delivering Excellence—A Daily Goal
Standard of Excellence: The Role of Technology in Enhancing the Customer Experience
Standard of Excellence: Turning Negative Customer Feedback Into Positive Outcomes
Standard of Excellence: Anticipating Customer Needs Early and Often
Standard of Excellence: The Power of Personalization in Customer Care
Standard of Excellence: Building Trust with Customers—The Foundation of Excellent Service