In-Circuit Pin Testing: An Excellent Potential Source of Value Creation
June 17, 2015 | Mitch Holtzer, AlphaEstimated reading time: 2 minutes
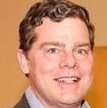
In-circuit pin testing (ICT) is a common method of inspecting electronic assemblies to measure the effectiveness of the assembly process and to predict electrical functionality. Test probes are put in contact with dedicated test points along the surface of an assembly, checking for electrical functions such as resistance, capacitance inductance and signal timing. Some circuit assemblers use functional testing for quality assurance as a substitute for ICT. In this example, the entire assembly either works or it doesn’t.
Unlike printing paste, placing components and reflowing solder, ICT is considered a non-value added process. In fact, ICT increases the cycle time of the assembly process. If the ICT is a fail, but the circuit being tested is actually good (known as a false negative), even more time is wasted trying to determine whether or not a good assembly will function properly.
The two basic types of ICT are commonly referred to as clamshell and flying probe. The clamshell ICT simultaneously tests dozens of points on a single board. One laboratory type of clamshell ICT device uses three types of pins and four different forces. A test vehicle is placed in the clamshell fixture. The clamshell is closed, and electrical resistivity is measured at each of the test pins.
Although clamshell devices are commonly used, they are somewhat impractical for testing solder paste and flux’s ability to be probed. Typically, there can be a 15-minute cycle time per test. Pin residue build up generally occurs after hundreds of tests. Cleaning flux build-up from pins is time-consuming, but necessary to minimize false negative readings.
Clamshell fixtures are quite expensive. A customized fixture must be fabricated for each unique assembly. This cost is only justified for the testing of high-value or high-volume assemblies.
Flying probe testing is also commonly used for lower value or lower volume assemblies. Flying probes test sequences are determined by easily changeable programming inputs. Clamshell fixtures are not required. Therefore, this type of test method is more suited for high mix circuit assembly applications.
In a common laboratory flying probe procedure, one pin type and one force are used, but the test runs for a total of 4,000 strikes. Flux build-up on the pins is an important part of the test. In addition, one common laboratory test vehicle contains four different types of pads. In this example, pad A is a 40 mil (1mm) square pad without vias, pad B is a 40 mil (1mm) square pad with 13 mil (0.33mm) vias, pad C is a 28 mil (0.7mm) round pad without vias, and pad D is a 28 mil (0.77mm) round pad with 13 mil (0.33mm) vias. There are 1,000 opportunities for each pad type.
Read The Full Article Here
Editor's Note: This article originally appeared in the June 2015 issue of SMT Magazine.
Testimonial
"We’re proud to call I-Connect007 a trusted partner. Their innovative approach and industry insight made our podcast collaboration a success by connecting us with the right audience and delivering real results."
Julia McCaffrey - NCAB GroupSuggested Items
MS2 Technologies, LLC/P. Kay Focuses on Central America with First Installation in Honduras
08/24/2025 | P. Kay Metal, Inc.This year MS2 Technologies has turned their focused to the growing electronics market in Central America. With that focus came the adaptation of MS2 and the Akila System from a Honduras-based corporation with manufacturing plants in both Honduras and Mexico.
BEST Inc. Provides High-Reliability BGA Reballing and Component Rework Services
08/22/2025 | BEST Inc.BEST Inc., a leader in electronic component services, is pleased to announce its component rework services are available for all types of area array devices including ball grid array, land grid array and quad flat no-lead SMT packages.
Indium Corporation Promotes Two Leaders in EMEA (Europe, Middle East, and Africa) Markets
08/05/2025 | Indium CorporationWith its commitment to innovation and growth through employee development, Indium Corporation today announced the promotions of Andy Seager to Associate Director, Continental Sales (EMEA), and Karthik Vijay to Senior Technical Manager (EMEA). These advancements reflect their contributions to the company’s continued innovative efforts with customers across Europe, the Middle East, and Africa (EMEA).
MacDermid Alpha Electronics Solutions Unveils Unified Global Website to Deepen Customer, Talent, and Stakeholder Engagement
07/31/2025 | MacDermid Alpha Electronics SolutionsMacDermid Alpha Electronics Solutions, the electronics business of Elements Solutions Inc, today launched macdermidalpha.com - a unified global website built to deepen digital engagement. The launch marks a significant milestone in the business’ ongoing commitment to delivering more meaningful, interactive, and impactful experiences for its customers, talent, and stakeholders worldwide.
KOKI to Showcase Analytical Services and New HF1200 Solder Paste at SMTA Guadalajara 2025
07/31/2025 | KOKIKOKI, a global leader in advanced soldering materials and process optimization services, will exhibit at the SMTA Guadalajara Expo & Tech Forum, taking place September 17 & 18, 2025 at Expo Guadalajara, Salón Jalisco Halls D & E in Guadalajara, Mexico.