Estimated reading time: 6 minutes
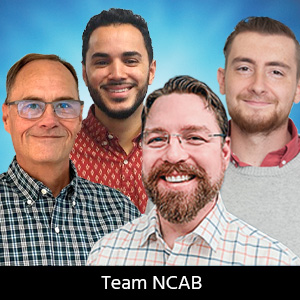
Fresh PCB Concepts: Key Considerations for Reliability, Performance, and Compliance in PCBs
As a field application engineer with many years of experience, I’ve conducted thousands of designs for manufacturing (DFM) analyses on printed circuit boards (PCBs). From basic one-layer boards to complex high density interconnect (HDI) designs, I’ve provided technical advice across a wide spectrum of technologies.
My point isn’t to boast, but to underscore the complexity hidden beneath the seemingly straightforward nature of medical PCBs. They come with their own set of challenges and requirements. This article covers those challenges, including key considerations like regulatory compliance, high reliability and durability, miniaturization, power management, signal integrity, material selection, and design for manufacturability. From diagnostic equipment to wearable health monitors, medical devices need these specialized boards to be reliable, precise, and to perform in demanding conditions.
Regulatory Compliance Standards
Regulatory compliance is the cornerstone of medical PCB design. Strict rules and regulations govern the medical field. In the U.S., FDA’s CFR Title 21 dictates that medical devices must meet guidelines on electrical/electronic safety and risk management. Moreover, medical PCBs must adhere to ISO 13485 for quality management systems and ISO 14971 for risk management.
Meeting these standards ensures medical device reliability, patient safety, and controlled, traceable manufacturing. Device manufacturers must document all design decisions and testing to meet regulatory standards. This often requires extensive testing to ensure compliance with EMC (electromagnetic compatibility) and safety requirements.
High Reliability and Durability
In medical applications, even a minor failure can have life-threatening consequences. Medical PCBs must function flawlessly in tough conditions because they’re often exposed to changing temperatures, humidity, and electrical noise. In critical devices like pacemakers, life-support machines, and diagnostic equipment, failure is not an option.
To ensure longevity and performance, medical PCB designs must be exceptionally durable, with components that resist degradation over time. This includes the ability to withstand physical stress, such as vibration, shock, and thermal variations. For wearable health devices, flexibility is equally important. The PCB must be resilient enough to endure repeated use, bending, and potential impacts without compromising functionality.
Achieving long-term reliability requires high-quality materials, precision-engineered components, and advanced manufacturing techniques. Partnership with a knowledgeable PCB supplier can enhance reliability, as they are well-versed in IPC-6010 series specifications. For example, if a medical PCB is designed to meet the IPC-6012, Class 2 standard, a supplier may recommend additional enhancements, such as Class 3 plating, to reinforce connections by increasing copper thickness in the holes. Moreover, incorporating extra quality checks, such as automatic optical inspection (AOI) on the internal layer, can detect circuit defects early in the manufacturing process, preventing costly failures. While these measures go beyond IPC standards, they ensure a robust and dependable PCB, reducing the risk of hidden flaws that could affect performance and delivery time.
Miniaturization and High Density Interconnect
The demand for smaller, more compact medical devices is increasing. Whether for portable diagnostic tools or wearable health monitors, miniaturization is essential to meet space constraints without compromising functionality. HDI technology allows designers to integrate more components into smaller spaces, significantly reducing PCB size while maintaining high performance.
HDI boards incorporate advanced features such as microvias, fine-pitch components, and multi-layer designs to optimize space. However, these dense layouts require manufacturing precision, as minor errors can impact reliability. Medical PCB designers must balance the push for miniaturization with the need for durability and compliance with stringent performance and safety standards.
Collaborating with a trusted PCB supplier is crucial in navigating miniaturization challenges. HDI designs introduce manufacturing complexities, including limitations on trace widths, spacing, and via sizes. By consulting with the supplier early in the design process, engineers can ensure their PCB is manufacturable and optimized for performance, preventing costly redesigns and production delays.
Power Management and Thermal Considerations
Power management is a critical challenge in medical PCB design, particularly for battery-powered or low-power medical devices. Pacemakers, hearing aids, and glucose monitors require precise power regulation to ensure stable performance while maximizing battery life. Efficient power management not only extends device longevity but also minimizes heat buildup, which can degrade components and compromise patient safety.
Thermal management is especially vital in medical PCBs that incorporate high-power components, as excessive heat can affect performance and durability. In compact designs, where heat dissipation is more challenging, it’s essential to implement advanced thermal management techniques. Strategies such as integrating copper coins, metal cores, or thermal vias help distribute heat more effectively, preventing localized hot spots. Additionally, copper planes can be used to enhance heat dissipation, ensuring the device remains within safe operating temperatures.
By prioritizing both power and thermal management in the design phase, engineers can create medical PCBs that deliver reliable, long-term performance while maintaining safety and efficiency.
Signal Integrity and Noise Reduction
Signal integrity is critical in medical applications, where accuracy and precision are paramount. Many medical devices rely on high-speed analog and digital signals for seamless communication between components. For instance, diagnostic equipment like MRI and ECG machines requires clean, noise-free signals to deliver precise readings. Any signal degradation or interference can lead to inaccurate data, potentially affecting patient care.
To preserve signal integrity, medical PCBs must be carefully designed with proper trace impedance control, robust power delivery networks, and effective grounding techniques. Techniques such as differential pair routing, minimizing crosstalk, and incorporating shielding or filtering components help reduce noise and electromagnetic interference (EMI). This is crucial in hospital environments, where multiple electronic devices operate simultaneously, increasing the risk of signal disruption.
Collaborating with a PCB supplier can enhance signal integrity by optimizing the PCB stack-up for both performance and manufacturability. A well-designed stack-up improves signal integrity and ensures compatibility with the supplier’s manufacturing process, expediting the tooling phase and reducing production delays.
Material Selection
Selecting the right materials for medical PCBs is crucial, as they must not only meet performance requirements but also comply with safety and environmental regulations. With medical devices placed inside bodies or that come into contact with patients, biocompatibility is a primary concern. Materials commonly used include medical-grade FR-4, polyimide, and ceramic, because of their stability, durability, and resistance to high temperatures and chemicals.
Devices exposed to harsh sterilization processes, such as autoclaving, must also be able to withstand repeated exposure to heat and pressure without degrading. Additionally, materials with low out-gassing properties are important in medical devices that operate in sensitive environments, such as in space, deep sea, or high-altitude applications.
Design for Manufacturability
DFM ensures efficient designs without compromising quality or function. In the medical industry, DFM involves early collaboration with manufacturers to address potential issues in the design phase.
DFM best practices for medical PCBs include simplifying complex designs, reducing the number of layers where possible, and ensuring the design is compatible with the manufacturer’s equipment and processes. This reduces the risk of manufacturing defects, such as misalignment of layers or improper hole sizes, which could compromise the performance of the PCB. Additionally, DFM allows for cost-effective manufacturing while maintaining the highest quality standards required for medical devices.
Conclusion
Designing PCBs for medical devices requires a careful balance between performance, compliance, and reliability. Regulatory compliance ensures devices are safe and effective for patient use, while high-reliability design principles ensure devices can function under the medical field’s demanding conditions. By considering factors like miniaturization, power management, signal integrity, material selection, and manufacturability, PCB designers can create medical devices that perform consistently and reliably. Don’t hesitate to reach out to your PCB supplier during the design phase.
As the medical device industry grows, so must PCB design strategies. With advancements in technology, there will be more opportunities for miniaturization and enhanced functionality, but the core principles of reliability, compliance, and safety will remain at the forefront of PCB design for medical applications.
Ryan Miller is a field applications engineer with NCAB Group.
More Columns from Fresh PCB Concepts
Fresh PCB Concepts: The Power of a Lunch & Learn for PCB ProfessionalsFresh PCB Concepts: Traceability in PCB Design
Fresh PCB Concepts: Tariffs and the Importance of a Diverse Supply Chain
Fresh PCB Concepts: PCB Stackup Strategies—Minimizing Crosstalk and EMI for Signal Integrity
Fresh PCB Concepts: PCB Plating Process Overview
Fresh PCB Concepts: PCB Design Essentials for Electric Vehicle Charging
Fresh PCB Concepts: The Critical Nature of Copper Thickness on PCBs
Fresh PCB Concepts: The Journey of a PCB—A Tale of Sustainability and Circularity