Estimated reading time: 5 minutes
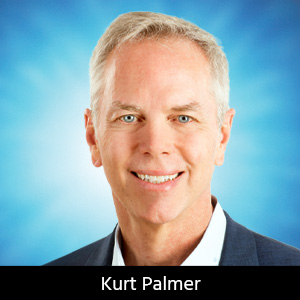
Driving Innovation: Schmoll—Decades of Technology Evolution
(Editor’s note: This is a new column by Kurt Palmer and Simon Khesin of Schmoll America. This column will appear regularly in PCB007 Magazine, and will be about overcoming challenges in mechanical and optical PCB fabrication with innovative solutions and always staying one step ahead.)
My name is Kurt Palmer, CEO of Schmoll America, and with my colleague Simon Khesin, we are launching this column about driving innovation in mechanical and optical process.
To begin, I will look back at Schmoll’s history, building a business of manufacturing PCB drilling machines, examining key technological milestones, and demonstrating how challenges were addressed over the years. In future columns, we will discuss current industry challenges, technological advancements, and anticipated trends shaping PCB manufacturing. Looking back at the past and reflecting on the lessons learned is always an insightful and valuable journey.
Before 1962: The Early Years
In its early years, Schmoll specialized in producing:
- Precision tools and stamping equipment
- Electric and pneumatic-controlled custom machinery
- Heating and cooling units
- TV and radio systems
- And more
These were challenging times for the company, and Schmoll continuously adapted to find its unique path.
By the late 1950s, PCB manufacturing began to emerge in Germany, creating demand for fast and precise drilling and routing machines.
1962–1993: Development of PCB Drilling Machines
In 1962, Schmoll introduced its first dedicated PCB drilling and routing machine. This machine was widely adopted in the industry, addressing the growing need for precise and reliable equipment in PCB production.
The transition to punched tape and card-based data transfer was shaping industrial machinery, and in 1966, Schmoll developed its first numerical control (NC) machine for PCB drilling. This technological shift made production more efficient, leading to an increase in PCB output.
By the 1970s, the company expanded globally, supplying equipment to both Western and Eastern markets. The growing number of installed machines highlighted the need for improved customer support, leading to the establishment of:
- A central spare parts warehouse
- A dedicated service department
- A training center for engineers
At that time, there was still a lot of manual labor in the industry, so, in 1976, Schmoll developed at 12-spindle drilling/routing machine with automatic tool change for Philips in Vienna. This innovation enhanced productivity by allowing automated tool change, reducing manual interventions.
As always, there was a need in the industry for better accuracy and larger capacity. How to achieve this? In 1979, the company made a huge step: We introduced granite machine bases and air bearings, which helped to improve accuracy and stability. At the same time, the transition from NC to computer numerical control (CNC) allowed operators and process engineers to adjust parameters such as infeed, outfeed, and spindle speed directly via a computerized interface—an important step enabled by the new computer era.
To gain additional labor savings, Schmoll introduced its first automated PCB drilling and routing system in 1989, allowing a second batch of PCBs to be prepared while the machine was still in operation. This marked an important step toward increased automation in PCB manufacturing.
That same year, Schmoll also expanded its portfolio by introducing its first X-ray machine, broadening its solutions for the PCB industry.
1993–2000: Growth and Global Expansion
The early 1990s brought significant market shifts, marking a critical moment for the company. During this time, Thomas Kunz acquired the company. While many businesses struggled during economic uncertainty, Kunz used this period to explore opportunities for growth.
Two key strategies for expansion:
- Advancing high-precision manufacturing technologies
- Expanding into both Western and Asian markets
One of the most significant advancements was the introduction of contact drilling technology, which enabled microvia drilling and supported the industry's move toward higher-density PCBs. This led to a major contract with an American company, Hewlett-Packard, requiring tight production schedules and further technological refinements.
To meet tight delivery schedules, extensive night shift testing was required to fine-tune the machines and perfect the technology, ensuring high reliability and performance.
During this period, key developments included:
- Development of laser drill bit inspection technology
- Enhancing of automation solutions
- Implementation of linear motors to enhance machine precision and efficiency
- Integration of high-speed spindles capable of reaching 180,000 rpm, increasing productivity
These technological improvements contributed to the growth of Schmoll and to industry development.
2000–2024: Diversification and Further Growth
In the early 2000s, Schmoll began developing optical machines, but a key moment came during the 2008 financial crisis. With a decline in orders that lasted for a period of nearly two years, the company invested in research and development, leading to the introduction of laser and direct imaging (LDI) technologies for PCB production.
What initially started as small departments within the company has grown into two of Schmoll’s core business segments, with the company becoming a recognized player in both laser processing and direct imaging.
The objective at Schmoll has always been to introduce innovative technological solutions to the market. The development approach focused on integrating emerging light sources—LEDs for direct imaging machines and PICO or COMBI (UV+CO2) for laser processing. Additionally, Schmoll prioritized the creation of fully in-house automated solutions to enhance efficiency and production consistency. The main goal was to refine both processes and machines to achieve even better results for customers.
The continued evolution of these technologies has made them a significant part of Schmoll’s product portfolio. At the same time, the company has continued to advance its drilling, routing, and X-ray machines, introducing new solutions to meet the ever-changing demands of the PCB industry.
Summary
Schmoll has consistently responded to market/industry challenges by developing new technologies and refining existing processes. Many of today’s standard industry ractices originated as technological advancements pioneered by Schmoll Maschinen.
By continuously innovating in mechanical and optical processes, we remain one step ahead and now, we have grown into a factory capable of producing 100 machines per month.
In future columns, Simon and I will explore the key technical challenges in mechanical and optical processes shaping the industry today, while looking into the future at the same time.
Kurt Palmer is President & CEO of Schmoll America.